Discover the Applications and Benefits of Refractory Cement
By:Admin
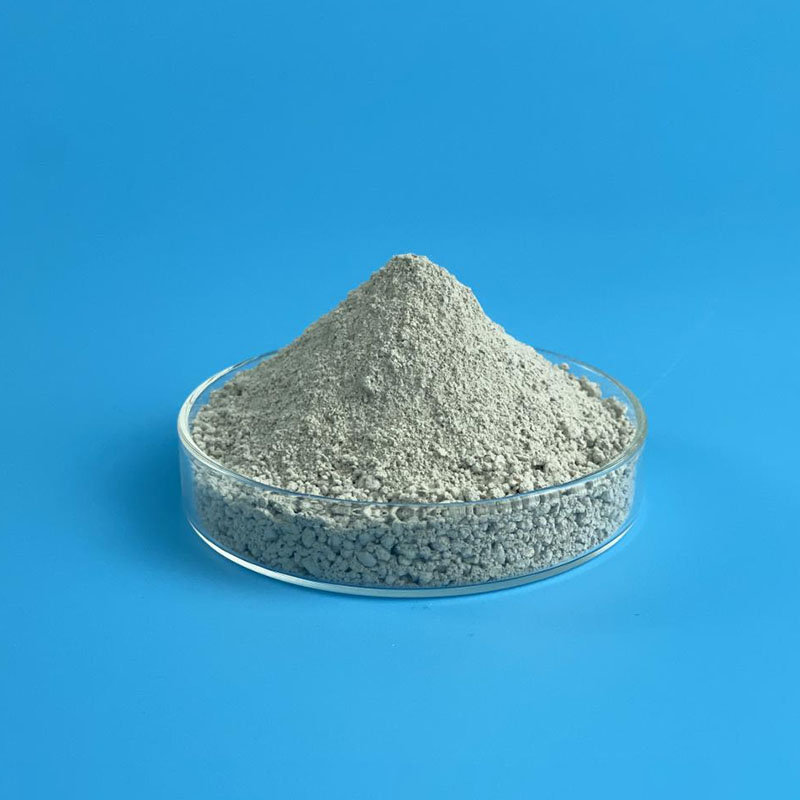
With over 50 years of experience in the industry, our company is a leading manufacturer and supplier of refractory products. We specialize in providing high-quality refractory materials and solutions for various industrial applications such as cement, steel, glass, and petrochemical industries. Our commitment to innovation and customer satisfaction has earned us a reputation as a trusted partner for businesses seeking reliable refractory solutions.
[News Content]:
Refractory cement, also known as heat resistant cement, is a specially formulated material that is designed to withstand high temperatures and harsh conditions. It is commonly used in various industrial settings where extreme heat and chemical resistance are required. The versatile nature of refractory cement makes it an essential component in many critical processes, such as kiln lining, furnace construction, and thermal insulation.
One of the key applications of refractory cement is in the manufacturing of cement products. In the cement industry, refractory cement plays a crucial role in maintaining the integrity of rotary kilns, which are used to produce clinker, a key ingredient in cement production. The ability of refractory cement to withstand the extreme temperatures and abrasive conditions inside the kiln is essential for ensuring the efficient and continuous operation of the cement manufacturing process.
In the steel industry, refractory cement is used in the construction of various equipment such as ladles, tundishes, and furnaces. These components are exposed to extreme temperatures and corrosive environments during the steelmaking process, making it essential to use high-quality refractory materials to ensure the longevity and performance of these critical assets. The superior heat resistance and durability of refractory cement make it an ideal choice for lining and insulation in steel manufacturing facilities.
The glass industry also relies on refractory cement for its ability to withstand the high temperatures required for the melting and shaping of glass. Refractory cement is used in the construction of glass furnaces, where it provides thermal insulation and resistance to chemical attacks from molten glass. The use of refractory cement in the glass industry ensures the efficient and reliable production of high-quality glass products.
In the petrochemical industry, refractory cement is employed in the construction of equipment such as reactors, incinerators, and thermal oxidizers. These applications require materials that can withstand the extreme temperatures and corrosive environments associated with the processing of chemical compounds. Refractory cement provides the necessary heat resistance and chemical stability to ensure the safe and efficient operation of petrochemical plants.
As a leading manufacturer and supplier of refractory products, our company is committed to providing high-quality refractory cement that meets the specific needs of our customers. Our extensive expertise in the industry enables us to develop custom refractory solutions tailored to the unique requirements of different industrial applications. We take pride in our ability to deliver reliable and cost-effective refractory products that contribute to the success of our clients' operations.
In conclusion, refractory cement is an indispensable material in various industrial sectors, where it plays a critical role in maintaining the integrity and performance of high-temperature equipment and processes. As a trusted provider of refractory solutions, our company is dedicated to supplying top-quality refractory cement that meets the stringent demands of modern industries. We remain committed to innovation and excellence, ensuring that our customers receive the best refractory products and services to support their ongoing success.
Company News & Blog
High-Quality High Heat Bricks: Meet Your Fire-Resistant Construction Needs
Title: Revolutionary High Heat Bricks Paving the Way for Unprecedented Performance in Industrial ApplicationsIntroduction:High Heat Bricks, developed and manufactured by a leading industry innovator, are rapidly gaining popularity in various industrial sectors worldwide. These bricks are designed to withstand extreme temperatures and provide unparalleled durability and insulation, making them ideal for demanding applications such as kilns, furnaces, incinerators, and even spacecraft designs. The advanced technology employed in the production of High Heat Bricks aligns with the company's commitment to revolutionize industries with cutting-edge solutions. Let's delve deeper to explore the features, benefits, and potential of these remarkable bricks.Unmatched Performance and Durability:One of the key reasons High Heat Bricks have garnered attention is their outstanding performance in high-temperature environments. These bricks are constructed from specially formulated refractory materials that can withstand temperatures exceeding 3000°C (5432°F). This remarkable thermal resistance ensures stability, explicitly safeguarding industrial equipment operating at extreme heat levels against wear and tear.The superior durability of High Heat Bricks can be attributed to their precise manufacturing process. The company utilizes advanced techniques, such as precision molding and sintering, allowing the bricks to maintain their integrity even under immense pressure and thermal stress. This premium construction enables industries to minimize maintenance costs while maximizing operational efficiency and productivity.Unrivaled Insulation Properties:High Heat Bricks are renowned for their exceptional insulating properties, facilitating improved energy conservation and reduced heat loss. These bricks possess low thermal conductivity, which effectively restricts heat transfer across the industrial equipment housing. As a result, industries can significantly lower energy consumption and operating costs while obtaining consistent and precise heat distribution.Additionally, the excellent insulation characteristics of High Heat Bricks play a crucial role in preventing heat-related injuries. By acting as an efficient barrier between hot surfaces and personnel, these bricks prioritize the safety of workers, reducing the risk of accidents and thermal burns.Versatility and Applications:The versatility of High Heat Bricks makes them suitable for a vast range of industrial applications. Industries such as steel manufacturing, glass production, petrochemicals, metallurgy, and aerospace have embraced these bricks due to their unmatched performance and reliability.In steel manufacturing, High Heat Bricks find utility in constructing blast furnaces, crucibles, and ladles, ensuring optimum performance in extreme conditions. In the aerospace industry, they are sought after for their lightweight characteristics and ability to withstand the demanding environments encountered during space missions. Furthermore, the petrochemical industry witnesses the bricks' application in the construction of high-heat cracking furnaces and reactors, enhancing operational efficiency.Environmental Sustainability:High Heat Bricks not only prioritize performance and durability but also contribute to ecological sustainability. The production process adheres to stringent environmental standards, ensuring reduced emissions and minimal energy consumption. Replacing conventional refractory materials with High Heat Bricks aids in curbing carbon footprints and furthering the company's commitment to environmental stewardship.Future Prospects:The rapid adoption and success of High Heat Bricks indicate a promising future for the company and its groundbreaking products. The increasing demand for energy-efficient and durable materials in various industrial sectors positions High Heat Bricks at the forefront of technological advancements.Looking ahead, the company envisions ongoing research and development to continuously improve the overall thermal resistance, insulation, and durability of High Heat Bricks. Collaborations with industry leaders, incorporating feedback from existing clients, and staying ahead of market trends are key strategies the company will employ to maintain its position as a leading provider of advanced high-temperature solutions.Conclusion:High Heat Bricks, developed by a renowned industry innovator, offer remarkable performance, durability, and insulation capabilities. Their ability to withstand extreme temperatures, coupled with outstanding thermal resistance, makes them ideal for critical industrial applications. From steel manufacturing to aerospace, these bricks are reshaping industries by providing energy-efficient and environmentally sustainable solutions. With promising prospects and continued innovation, High Heat Bricks are poised to reshape the global industrial landscape and revolutionize high-temperature applications across various sectors.
Revolutionary Electric Foundry Furnace: Advancements in Metal Casting Unveiled
Electric Foundry Furnace: Advancing Metallurgical Processes for the IndustryIn an era of rapid technological advancement, industries are constantly seeking innovative solutions to enhance their production processes. Diving headfirst into this quest, a renowned company has introduced an exceptional innovation – the Electric Foundry Furnace. This revolutionary equipment has the potential to revolutionize metallurgical operations, making them more efficient and sustainable.Utilizing state-of-the-art technology, the Electric Foundry Furnace represents a significant leap forward in the field of metallurgy. By combining electromagnetic induction and advanced materials, it provides industries with the ability to melt and refine various metals with unmatched precision and speed. This cutting-edge furnace puts the power of metallurgical processes firmly in the hands of manufacturers.The Electric Foundry Furnace boasts a plethora of advantages over traditional furnaces. Firstly, it significantly reduces energy consumption, making it an environmentally friendly and sustainable option for industries. By leveraging electromagnetic induction, this furnace facilitates highly efficient heat transfer, resulting in minimized energy wastage. Manufacturers can effectively streamline their operations, reducing their carbon footprint and fostering sustainable production practices.Additionally, the Electric Foundry Furnace offers unrivaled flexibility and versatility. With this innovative equipment, businesses can seamlessly adapt their operations to different metal types and requirements. Its programmable settings allow for precise temperature control, enabling manufacturers to achieve optimal results across a wide range of metals and alloys. This versatility ensures that industries can meet the ever-evolving demands of the market, ultimately leading to increased productivity and customer satisfaction.Operational safety is another paramount aspect of the Electric Foundry Furnace's design. Equipped with advanced safety features, such as automated shutdown mechanisms and temperature sensors, the furnace minimizes the risk of accidents and ensures the wellbeing of workers. These safety measures provide peace of mind to manufacturers, allowing them to focus on optimizing production instead of worrying about potential hazards.Furthermore, the company behind this ground-breaking invention understands the importance of user-friendly interfaces. Implementing a simple yet intuitive control system, they enable operators to navigate the furnace's functionalities effortlessly. Whether it be adjusting temperature settings or monitoring the melting process, the Electric Foundry Furnace offers a seamless user experience. This intuitive interface ensures that even those with limited technical expertise can operate the furnace effectively, saving valuable time and resources.Realizing the immense potential of the Electric Foundry Furnace, numerous industries have already begun incorporating this innovative equipment into their operations. Foundries, automotive manufacturers, and aerospace companies, among others, have reported significant improvements in their metallurgical processes since adopting this state-of-the-art furnace. With increased efficiency and reduced costs, businesses can gain a competitive edge in the global market, fueling economic growth and driving industrial development.Looking toward the future, the company behind the Electric Foundry Furnace is committed to continuous improvement and technological advancement. Investing heavily in research and development, they aim to refine and expand the capabilities of their exceptional equipment. By collaborating with industry experts and closely monitoring market needs, they strive to bring forth innovations that will further revolutionize metallurgical operations, empowering businesses to achieve new heights of success.In conclusion, the Electric Foundry Furnace stands as a game-changer in the realm of metallurgy. With its energy efficiency, versatility, safety features, and user-friendly interface, this revolutionary furnace is poised to transform the way industries approach their metallurgical processes. As the market continues to embrace this cutting-edge technology, we can expect to witness unprecedented advancements in metallurgical operations, leading to a more sustainable and prosperous future for the industry.
Why Magnesia Is the Ideal Material for Bricks
Title: Researchers Discover Game-Changing Ingredient for Sustainable Building MaterialsSubtitle: A Revolutionary Breakthrough in Magnesia-Based Bricks Paves the Way for a Greener Future in Construction(Date)(Location) - In a significant step towards sustainable and environmentally-friendly construction, researchers have recently unveiled an innovative ingredient that promises to revolutionize the building materials industry. Magnesia, combined with groundbreaking techniques developed by (company name), offers a game-changing solution for creating eco-friendly bricks that have the potential to transform the entire construction landscape.Traditional methods of brick production have long been associated with significant carbon emissions and the depletion of finite natural resources. However, recent scientific discoveries have shed light on the immense potential of magnesia, a naturally occurring mineral, as a sustainable alternative in brick manufacturing due to its advantageous properties.Unlike conventional bricks, which are predominantly made from clay and sand, magnesia-based bricks offer remarkable advantages when it comes to both durability and sustainability. Magnesia is highly resistant to fire, weather conditions, and chemical erosion, ensuring that the resulting bricks are significantly sturdier and longer-lasting. Furthermore, its abundant availability in nature makes it a cost-effective and environmentally-friendly option for scalable production.Leading this groundbreaking research is (company name), a pioneer in developing sustainable technologies for the construction industry. With a commitment to advancing eco-friendly practices, the company has harnessed the full potential of magnesia to create a versatile solution that can be used in various construction applications.The (company name) team's cutting-edge approach involves utilizing a proprietary technique, known as (proprietary technique name), to combine magnesia with other natural materials, resulting in an innovative building material that excels in strength, insulation, and sustainability. Through rigorous testing and experimentation, they have successfully produced bricks that surpass industry standards in performance while significantly reducing their carbon footprint.Revolutionizing the world of construction, magnesia-based bricks offer a plethora of environmental benefits. Firstly, the production process emits far less carbon dioxide compared to conventional brick manufacturing, contributing to a reduction in greenhouse gas emissions, which are responsible for climate change. Additionally, the durability of magnesia bricks reduces the need for frequent replacements and repairs over time, significantly lowering construction waste and reducing resource consumption.Moreover, the energy-efficient nature of magnesia-based bricks contributes to better insulation and reduced energy costs in buildings. With their impressive thermal properties, these bricks can provide enhanced energy efficiency, ensuring that indoor spaces remain cool during summers and warm during winters. This not only enhances the comfort of occupants but also reduces reliance on heating and cooling systems, leading to considerable energy savings.The potential applications of magnesia-based bricks are broad and include both residential and commercial construction projects. From multi-story buildings to infrastructure projects, these sustainable bricks can be used as load-bearing structures, facades, and even internal partitions. This versatility reflects the adaptability of magnesia-based bricks in meeting the diverse needs of the construction industry.Recognizing the significance of eco-friendly building materials, policymakers are also actively supporting the adoption of magnesia-based bricks. Numerous governments and regulatory bodies are incentivizing sustainable construction practices through tax breaks, grants, and subsidies. This largely contributes to creating a conducive environment for builders, developers, and architects to embrace magnesia-based bricks, ultimately accelerating the transition towards a greener future.The powerful combination of magnesia and forward-thinking techniques developed by (company name) is poised to reshape the construction industry as we know it. By innovating on traditional brickmaking methods, this breakthrough technology offers a sustainable alternative that not only reduces environmental impact but also improves the overall quality and longevity of buildings.As the world wakes up to the urgent need for sustainable solutions, the journey towards a greener future is undoubtedly fueled by revolutionary advancements like magnesia-based bricks. With the tireless efforts of researchers, industry leaders, and policymakers, it is just a matter of time before these eco-friendly bricks become commonplace in construction practices worldwide, paving the way for a brighter and more sustainable future.
Top-Rated Ceramic Thermal Blanket for Efficient Heat Insulation
Ceramic Thermal Blanket Revolutionizes Insulation and Energy Efficiency[Company Name], a leading innovator in thermal insulation technologies, is proud to introduce its latest breakthrough product: the Ceramic Thermal Blanket. Designed to provide superior insulation and enhance energy efficiency, this cutting-edge solution promises to revolutionize the way we achieve optimal thermal comfort in various settings.The Ceramic Thermal Blanket represents an exciting advancement in thermal insulation technology, offering a highly effective and versatile solution for both residential and commercial applications. With its unique composition and superior thermal properties, the blanket is capable of minimizing heat transfer, thereby significantly improving energy efficiency and reducing heating or cooling costs.One of the key features of the Ceramic Thermal Blanket is its use of advanced ceramic materials. Ceramic fibers, known for their excellent insulation capabilities, have been strategically woven together to create a highly efficient barrier against heat transfer. This innovative design ensures that indoor spaces are well-insulated, shielding occupants from external temperature extremes.Furthermore, the blanket's composition enables it to provide outstanding insulation performance across a wide temperature range. Whether in extreme cold or hot climates, the Ceramic Thermal Blanket remains effective in maintaining a comfortable indoor temperature, resulting in reduced reliance on heating or cooling systems.In addition to enhancing insulation and reducing energy consumption, the Ceramic Thermal Blanket also offers several other noteworthy benefits. For one, its installation is quick and hassle-free, making it an ideal solution for retrofits or new constructions. The blanket can be easily draped or wrapped around various surfaces, including walls, ceilings, pipes, and ducts, providing seamless coverage and enhanced thermal efficiency.Moreover, the Ceramic Thermal Blanket is a lightweight and flexible solution, allowing for convenient customization and application in diverse settings. Its versatility makes it suitable for various industries, from residential buildings and commercial spaces to industrial facilities and automotive applications. By harnessing the power of advanced ceramic materials, the blanket delivers outstanding thermal performance while remaining environmentally friendly.The introduction of the Ceramic Thermal Blanket comes at a critical time when energy efficiency and sustainability are paramount concerns. As governments and organizations worldwide strive to reduce greenhouse gas emissions and combat climate change, this innovative product aligns perfectly with these crucial goals. By significantly improving insulation and reducing energy consumption, the Ceramic Thermal Blanket helps to mitigate environmental impact while simultaneously providing cost savings for users.[Company Name] is dedicated to continuously pushing the boundaries of thermal insulation technologies and providing sustainable solutions for a greener future. With the Ceramic Thermal Blanket, the company aims to empower individuals and businesses to make environmentally conscious choices without compromising on thermal comfort or energy efficiency.In conclusion, the Ceramic Thermal Blanket represents a breakthrough in thermal insulation technology, offering superior insulation, energy efficiency, and versatility. By harnessing the power of advanced ceramics, this innovative product allows for seamless installation, exceptional thermal performance, and reduced reliance on heating or cooling systems. With a focus on sustainability and environmental responsibility, [Company Name] aims to pave the way for a greener future with its revolutionary Ceramic Thermal Blanket.
Benefits and Uses of High-Quality Fire Bricks for Kilns: A Comprehensive Guide
Title: Kiln Fire Bricks - A Revolutionary Solution for High-Temperature ApplicationsIntroduction:In the rapidly evolving field of construction and manufacturing, the demand for reliable and durable high-temperature-resistant materials has never been greater. This is particularly true in industries such as ceramics, glass, metallurgy, and cement production where extreme temperatures are required for numerous processes. Kiln Fire Bricks, an innovative product developed by an industry-leading company, have emerged as a game-changer in providing exceptional thermal insulation and durability. This article explores the features, benefits, and applications of Kiln Fire Bricks while offering insights into the company behind this groundbreaking solution.Company Introduction: (Please provide specific details about the company)[Company Name] - Revolutionizing High-Temperature Applications[Company Name], a renowned pioneer in the field of high-temperature materials, has been at the forefront of innovation for several decades. Established in [Year], they have continuously strived to provide advanced solutions to industries facing the challenges of extreme temperatures. With years of expertise and a dedicated team of researchers, [Company Name] has developed Kiln Fire Bricks, a transformational product that exceeds industry standards in terms of performance and durability.Features and Benefits of Kiln Fire Bricks:1. Superior Thermal Insulation: Kiln Fire Bricks are specifically engineered to withstand and insulate against extreme heat generated in various industrial applications. Due to their unique composition, these bricks boast remarkable insulation properties, reducing heat loss and optimizing energy efficiency.2. Exceptional Durability: The bricks are manufactured using carefully selected raw materials that undergo rigorous quality control measures. This ensures that Kiln Fire Bricks possess the exceptional strength and durability required to withstand repeated exposures to high temperatures, minimizing the need for frequent maintenance and replacement.3. Resistance to Thermal Shocks: Kiln Fire Bricks are designed to withstand rapid temperature fluctuations without cracking or undergoing structural damage. Their ability to resist thermal shocks makes them ideal for the intense heating and cooling cycles experienced in kilns, furnaces, and other high-temperature equipment.4. Chemical Stability: These bricks exhibit excellent resistance to highly corrosive chemicals, making them perfect for use in industries involving chemical reactions and high-temperature processes. The bricks do not degrade or react with the harsh substances, ensuring the longevity of the equipment they are used in.5. Customizable Shapes and Sizes: Kiln Fire Bricks are available in a variety of shapes and sizes, allowing for precise customization to fit the specific requirements of different applications and equipment. This flexibility ensures optimal performance, efficiency, and ease of installation.Applications of Kiln Fire Bricks:1. Ceramics Industry: Kiln Fire Bricks find extensive use in ceramic kilns, where they line the walls, floor, and ceiling of the kiln to withstand the extremely high temperatures necessary for firing ceramics. The superior insulation properties of these bricks help to maintain uniform heat throughout the kiln, ensuring consistent quality and energy efficiency.2. Glass Industry: Glass manufacturers employ Kiln Fire Bricks in their glass furnace linings to withstand the extreme heat during the melting and molding processes. The bricks facilitate smooth and efficient operation, improving productivity while ensuring the longevity of the furnaces.3. Metallurgy: Kiln Fire Bricks play a critical role in protecting metallurgical furnaces, ensuring the furnace's stability and longevity. These bricks create an insulated barrier against the intense heat generated during the smelting and refining processes, while also preventing chemical reactions with the furnace's refractory lining.4. Cement Production: In the cement industry, Kiln Fire Bricks are used to line rotary kilns, where raw materials are heated to temperatures exceeding 1450°C (2642°F). The ability of these bricks to withstand the extreme temperatures inside the kiln contributes to efficient cement production and reduces heat loss.Conclusion:Kiln Fire Bricks have revolutionized high-temperature applications in industries across the globe. With their superior thermal insulation, exceptional durability, and resistance to thermal shocks and chemicals, these bricks provide the perfect solution for kilns, furnaces, and industrial equipment operating at extreme temperatures. Backed by the unwavering commitment of [Company Name] to deliver cutting-edge materials, Kiln Fire Bricks have become the go-to choice for industries seeking efficient and reliable high-temperature insulation.
High-quality and Durable 3kg Crucible: Essential for Efficient Operations
Title: Leader in Industrial Materials Launches Advanced 3kg Crucible for Enhanced Manufacturing ProcessesIntroduction:As an industry leader in innovative materials and solutions, our company is proud to announce the launch of an advanced 3kg Crucible, specifically designed to revolutionize manufacturing processes. This new addition to our product portfolio represents our commitment to providing cutting-edge solutions that enhance productivity and efficiency in various industries.Crucible - The Backbone of Manufacturing:Crucibles are an essential component in several manufacturing processes, particularly in industries such as metallurgy, glass, ceramics, and materials science. Crucibles serve as vessels for high-temperature melting, refining, and other material transformation processes. The quality and design of a crucible play a pivotal role in determining the success and efficiency of these manufacturing operations.Innovation Unveiled: Introducing the State-of-the-Art 3kg Crucible:Our company's research and development team has invested extensive efforts into creating a state-of-the-art 3kg Crucible that sets new industry standards. This advanced crucible combines premium quality materials, cutting-edge technology, and precision engineering to deliver exceptional performance and durability.Key Features and Benefits:1. Enhanced Thermal Conductivity: The 3kg Crucible incorporates a proprietary blend of advanced materials that ensures optimal thermal conductivity. This feature allows for faster and more efficient heat transfer, significantly reducing melt times and overall manufacturing cycles.2. Extreme Temperature Resistance: The crucible boasts remarkable resistance to high temperatures, making it ideal for use in extreme heat environments. Its ability to withstand prolonged exposure to high temperatures not only enhances the manufacturing process but also ensures longevity, reducing the need for frequent replacements.3. Superior Chemical Stability: The crucible's composition guarantees excellent chemical stability, enabling it to withstand the corrosive effects of molten materials and aggressive chemicals often used in various manufacturing applications. This stability minimizes contamination risks and ensures consistent production quality.4. Design for Optimal Pouring: The 3kg Crucible has been meticulously engineered for improved pouring precision. Its innovative design eliminates the risk of spillage and allows for smooth, controlled pouring, maximizing operational safety and minimizing material wastage.5. Durable and Easy to Clean: Constructed with durability in mind, the crucible exhibits exceptional strength, preventing cracking, chipping, and premature wear. Additionally, its easy-to-clean surface simplifies maintenance, reducing downtime and improving overall efficiency.Quality Assurance and Industry Applications:Our company emphasizes stringent quality control measures to ensure each 3kg Crucible meets the highest standards of reliability and performance. Through extensive testing and continuous improvement, we are confident that our crucibles will exceed expectations even in the most demanding industrial applications.The new 3kg Crucible is anticipated to have a widespread impact across various sectors, such as foundries, laboratories, educational institutions, and product development centers. Its versatility and superior performance make it an indispensable tool for professionals engaged in alloy production, metal casting, research, and development.Conclusion:As a trusted leader in the production of industrial materials, our company's launch of the advanced 3kg Crucible reinforces our commitment to driving innovation and excellence in manufacturing processes. With its exceptional features and benefits, this new crucible stands to enhance productivity, reduce costs, and improve overall operational efficiency across multiple industries. We are confident that this groundbreaking product will revolutionize the way materials are transformed and contribute to the success of our customers' endeavors.
Top 5 Tips for Maintaining a Large Smelting Furnace
Global Large Smelting Furnace Market Trends and AnalysisThe global large smelting furnace market is witnessing significant growth due to the increasing demand for high-quality metal production in various industries. Large smelting furnaces are used for the production of metals such as iron, copper, aluminum, and steel, among others. These furnaces are designed to handle large quantities of raw materials and efficiently convert them into high-quality metal products. With the growing importance of metal production in industries such as construction, automotive, and manufacturing, the demand for large smelting furnaces is expected to continue to rise.One of the leading players in the large smelting furnace market is a company that has been at the forefront of innovation and technology in the metal industry for over three decades. The company is known for its cutting-edge smelting furnace solutions that are designed to optimize efficiency, reduce operating costs, and improve the overall quality of metal production. With a strong focus on research and development, the company has been able to develop a range of large smelting furnaces that are capable of meeting the diverse needs of the global metal industry.The company's large smelting furnace solutions are built to deliver high performance and reliability, making them ideal for heavy-duty metal production operations. These furnaces are equipped with advanced control systems and automation technology, allowing for precise temperature and process control, as well as real-time monitoring of the production process. This not only ensures consistent and high-quality metal output but also reduces the risk of downtime and maintenance issues.In addition, the company's large smelting furnaces are designed with a strong focus on energy efficiency and environmental sustainability. By incorporating advanced thermal insulation and waste heat recovery systems, these furnaces are able to minimize energy consumption and reduce greenhouse gas emissions. This makes them an environmentally friendly choice for metal producers looking to minimize their carbon footprint and comply with strict environmental regulations.Furthermore, the company's large smelting furnace solutions are backed by a comprehensive range of services, including installation, commissioning, maintenance, and technical support. This ensures that customers are able to maximize the performance and longevity of their furnace systems, while minimizing operational risks and costs. With a global network of service centers and highly skilled technicians, the company is able to provide timely and reliable support to its customers, regardless of their location.The global large smelting furnace market is highly competitive, with several key players vying for market share. However, the company has been able to maintain its position as a market leader due to its relentless commitment to innovation, quality, and customer satisfaction. By continuously investing in research and development, the company is able to stay ahead of market trends and deliver cutting-edge smelting furnace solutions that meet the evolving needs of the metal industry.Looking ahead, the global large smelting furnace market is expected to continue to grow as the demand for high-quality metal production remains strong. With its proven track record of excellence and its unwavering focus on technological innovation, the company is well-positioned to capitalize on this growth and solidify its position as a leading player in the global large smelting furnace market. As the industry continues to evolve, the company remains committed to pushing the boundaries of what is possible in large smelting furnace technology, and to providing its customers with the most advanced and reliable solutions available.
Top-quality Silica Refractory: A Complete Guide
Silica Refractory, a cutting-edge leader in the refractory industry, is making waves with its innovative products and solutions for high-temperature industrial applications. With a commitment to excellence and a focus on customer satisfaction, the company has established itself as a trusted partner for businesses in a wide range of industries.Silica Refractory's dedication to quality is evident in its state-of-the-art manufacturing facilities, which are equipped with the latest technology and staffed by a team of experienced professionals. Through a rigorous quality control process, the company ensures that its products meet the highest standards for performance and reliability.One of Silica Refractory's standout products is its high-purity silica refractory material, which is designed to withstand extreme temperatures and harsh operating conditions. This material is ideal for use in a variety of applications, including glass production, metallurgy, and petrochemical processing. With its exceptional thermal stability and resistance to corrosion, silica refractory offers a superior solution for businesses seeking reliable and long-lasting refractory products.In addition to its high-purity silica refractory material, Silica Refractory offers a comprehensive range of refractory products, including fireclay, high-alumina, and insulating materials. With a diverse product line and the ability to customize solutions to meet specific customer needs, the company has established itself as a one-stop shop for all refractory needs.Silica Refractory's commitment to customer satisfaction is further demonstrated through its dedication to providing exceptional service and support. The company's team of technical experts works closely with customers to understand their unique requirements and recommend the most suitable products for their applications. Additionally, Silica Refractory offers installation services and ongoing maintenance support to ensure that customers achieve optimal performance and longevity from their refractory products.As a forward-thinking company, Silica Refractory is also dedicated to research and development, continually exploring new technologies and materials to enhance its product offerings. Through collaboration with industry partners and investment in cutting-edge research, the company remains at the forefront of innovation in the refractory industry.In recent years, Silica Refractory has expanded its reach to serve customers worldwide, with a growing presence in international markets. This global expansion has been driven by the company's reputation for quality and reliability, as well as its ability to provide tailored solutions for diverse industrial applications.Looking ahead, Silica Refractory is poised for continued growth and success, with a focus on expanding its product line, enhancing its technological capabilities, and further diversifying its customer base. By staying true to its core values of quality, innovation, and customer-centricity, the company is well-positioned to be a leading force in the refractory industry for years to come.In conclusion, Silica Refractory stands out as a trusted partner for businesses in need of high-quality refractory products and solutions. With its commitment to excellence, innovative products, and exceptional customer service, the company has earned a reputation as a leader in the industry. As it continues to expand its global presence and invest in new technologies, Silica Refractory is poised to shape the future of the refractory industry and meet the evolving needs of its customers.
Discover the Latest Innovations in Jewellery Casting Furnaces
Title: Innovative Jewellery Casting Furnace Sets New Industry StandardIntroduction:In the competitive world of jewellery manufacturing, precision, efficiency, and quality are paramount. To meet these demands, a renowned industry leader has introduced an advanced jewellery casting furnace that is revolutionizing the way jewellery is manufactured. With its cutting-edge technology and exceptional performance, this furnace is setting new industry standards and earning accolades from jewellery manufacturers worldwide.Company Background:With a rich legacy spanning over two decades, our featured company has consistently pioneered breakthrough solutions for the jewellery industry. Leveraging their expertise in metallurgy and engineering, they have earned a reputation for manufacturing state-of-the-art equipment that elevates the jewellery-making process to new heights. Recognizing the need for improved casting techniques, they have developed and launched their latest innovation – the Jewellery Casting Furnace.Revolutionizing Casting Techniques:The newly introduced Jewellery Casting Furnace is designed to address the challenges faced by jewellery manufacturers during the casting process. With its sophisticated features and cutting-edge technology, this furnace is streamlining the production process, ensuring better quality, and optimizing productivity.One of the key features of this furnace is its precise temperature control system. Temperature fluctuations during the casting process can lead to defects and compromised jewellery quality. The Jewellery Casting Furnace overcomes this challenge by offering an advanced temperature monitoring system that provides accurate control, resulting in consistent high-quality casts.Additionally, the furnace incorporates a rapid heating system, significantly reducing the waiting time usually associated with heating crucibles. This enhancement is allowing manufacturers to optimize their production workflow by minimizing downtime and maximizing productivity.Quality and Efficiency:The Jewellery Casting Furnace ensures precise and consistent temperature control, enabling manufacturers to achieve impeccable casting results. By significantly reducing defects and imperfections, this innovative furnace enhances the quality of the final product, boosting customer satisfaction. Furthermore, the furnace's energy-efficient design optimizes power consumption, resulting in reduced operational costs for jewellery manufacturers.Moreover, the advanced technology employed in the design of this furnace allows for remote monitoring and control. Manufacturers can conveniently adjust and monitor the casting process from their mobile devices or computers, ensuring seamless workflow management and facilitating quick troubleshooting when required.Industry Recognition:The excellent performance and remarkable technological features of the Jewellery Casting Furnace have garnered immense praise from the jewellery manufacturing industry. Several renowned jewellery manufacturers across the globe have incorporated this furnace into their production lines, testifying to its ability to optimize casting operations, increase productivity, and enhance the quality of their products.Feedback from manufacturers who have embraced this innovative furnace has been overwhelmingly positive. They have reported significant improvements in cast quality, reduction in defects, enhanced production efficiency, and cost savings. The Jewellery Casting Furnace has proven to be a game-changer for industry professionals, empowering them to deliver superior craftsmanship and meet the growing demands of their discerning clientele.Conclusion:With the introduction of the Jewellery Casting Furnace, this industry-leading company has once again raised the bar in the jewellery manufacturing sector. By combining cutting-edge technology, customizability, and precision control, this furnace is transforming the casting process and setting new industry standards. Manufacturers now have a reliable and efficient tool at their disposal to create exquisite jewellery, increase productivity, and deliver exceptional results. With its widespread adoption, the Jewellery Casting Furnace is shaping the future of the jewellery manufacturing industry.
Exploring the Advantages of Ceramic Fiber in Construction and Insulation Applications
Possible news article:Innovative Ceramic Fiber Material Offers High-Temperature Solutions for Industrial ApplicationsA leading manufacturer of high-performance materials has launched a new product line that leverages the properties of ceramic fibers to enhance the strength, insulation, and durability of various industrial systems. The company, based in the United States, has developed a proprietary process to produce Kaowool Ceramic Fiber, a versatile material that can withstand extreme temperatures and pressures, while also providing excellent resistance to chemicals, abrasion, and thermal shock. The new product line consists of different forms and configurations of the fiber, such as blankets, boards, ropes, papers, and modules, which can be customized to suit specific needs and applications.Ceramic fibers are a type of inorganic, non-metallic material that is made from spinning or blowing molten mineral substances into fine fibers. They are known for their exceptional thermal properties, including low thermal conductivity, high temperature resistance, and thermal stability. Ceramic fibers also have excellent mechanical properties, such as high tensile strength, stiffness, and toughness. Unlike organic fibers such as carbon or glass, ceramic fibers are not combustible, and do not release toxic gases when exposed to fire. These features make ceramic fibers ideal for use in high-temperature environments where conventional materials would fail or degrade, such as furnaces, kilns, boilers, pipes, and mufflers.Kaowool Ceramic Fiber takes advantage of these properties to offer a range of benefits for industrial users. For example, the fiber can be formed into lightweight, flexible blankets that can be wrapped around pipes or equipment to provide superior thermal insulation. The blankets are also resistant to chemical corrosion and erosion, making them suitable for harsh environments such as chemical plants or oil refineries. The blankets can tolerate temperatures up to 2600°F (1427°C) without shrinkage or deformation, and maintain their structural integrity even after exposure to rapid temperature changes or thermal cycling. This makes them ideal for use in furnaces or ovens that require precise temperature control or frequent heating and cooling cycles.In addition to blankets, Kaowool Ceramic Fiber is also available in boards, which can be used as heat shields, baffles, or supports. The boards offer a smooth surface that is easy to cut, drill, or machine, and can be shaped into complex geometries or contours. The boards are also highly resistant to impact and vibration, making them suitable for use in transportation or aerospace applications. The fiber can also be made into ropes, which can be knotted or woven into gaskets, seals, or packing for valves, pumps, or flanges. The ropes provide a tight, leak-proof seal that can withstand high pressures or vacuum. The fiber can also be used to make papers, which can be used as filters, insulators, or barriers. The papers can withstand moisture, chemicals, and gas permeation, making them useful in filtration, soundproofing, or packaging applications.Kaowool Ceramic Fiber also offers benefits for installation and maintenance. The fiber is easy to handle, cut, and install, and does not require specialized tools or skills. The fiber can be glued, screwed, or wedged into place, and can be reused or repaired as needed. The fiber also does not produce dust or fibers when handled, reducing the risk of occupational or environmental hazards. The fiber is also recyclable, and can be reused or repurposed after use, reducing waste and environmental impact.The company that produces Kaowool Ceramic Fiber has a long history of innovation in materials science. Founded in the early 20th century, the company has pioneered many advanced materials, such as silica aerogels, high-purity alumina, and specialty glasses. The company has also developed many applications for these materials, such as insulation, electronics, optics, and healthcare. The company has a global network of customers and partners in various industries, and is committed to sustainability, quality, and customer satisfaction.The launch of Kaowool Ceramic Fiber represents a significant addition to the company's portfolio of high-performance materials. The product line offers a compelling solution for industrial users who seek better performance, efficiency, and reliability in their systems. The company expects to see strong demand for the fiber in industries such as energy, chemicals, metals, ceramics, and transportation, where high temperatures and harsh conditions are common. The company also plans to develop new applications and forms of the fiber, leveraging its expertise in materials and processing. Overall, Kaowool Ceramic Fiber is poised to become a leading product in the global market for high-temperature materials and solutions.