Discover the Latest Innovations in Jewellery Casting Furnaces
By:Admin
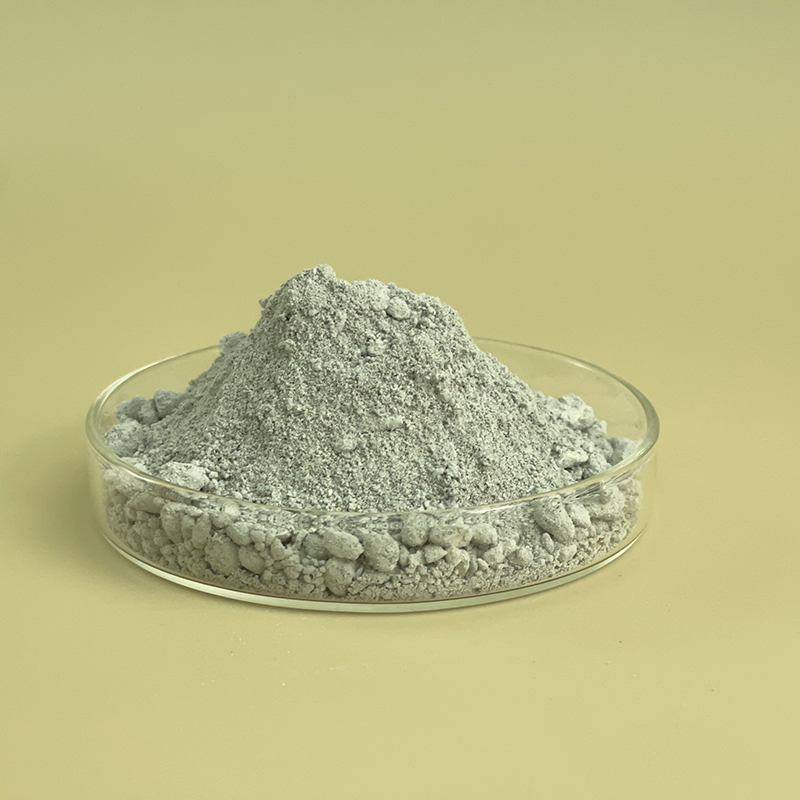
Introduction:
In the competitive world of jewellery manufacturing, precision, efficiency, and quality are paramount. To meet these demands, a renowned industry leader has introduced an advanced jewellery casting furnace that is revolutionizing the way jewellery is manufactured. With its cutting-edge technology and exceptional performance, this furnace is setting new industry standards and earning accolades from jewellery manufacturers worldwide.
Company Background:
With a rich legacy spanning over two decades, our featured company has consistently pioneered breakthrough solutions for the jewellery industry. Leveraging their expertise in metallurgy and engineering, they have earned a reputation for manufacturing state-of-the-art equipment that elevates the jewellery-making process to new heights. Recognizing the need for improved casting techniques, they have developed and launched their latest innovation – the Jewellery Casting Furnace.
Revolutionizing Casting Techniques:
The newly introduced Jewellery Casting Furnace is designed to address the challenges faced by jewellery manufacturers during the casting process. With its sophisticated features and cutting-edge technology, this furnace is streamlining the production process, ensuring better quality, and optimizing productivity.
One of the key features of this furnace is its precise temperature control system. Temperature fluctuations during the casting process can lead to defects and compromised jewellery quality. The Jewellery Casting Furnace overcomes this challenge by offering an advanced temperature monitoring system that provides accurate control, resulting in consistent high-quality casts.
Additionally, the furnace incorporates a rapid heating system, significantly reducing the waiting time usually associated with heating crucibles. This enhancement is allowing manufacturers to optimize their production workflow by minimizing downtime and maximizing productivity.
Quality and Efficiency:
The Jewellery Casting Furnace ensures precise and consistent temperature control, enabling manufacturers to achieve impeccable casting results. By significantly reducing defects and imperfections, this innovative furnace enhances the quality of the final product, boosting customer satisfaction. Furthermore, the furnace's energy-efficient design optimizes power consumption, resulting in reduced operational costs for jewellery manufacturers.
Moreover, the advanced technology employed in the design of this furnace allows for remote monitoring and control. Manufacturers can conveniently adjust and monitor the casting process from their mobile devices or computers, ensuring seamless workflow management and facilitating quick troubleshooting when required.
Industry Recognition:
The excellent performance and remarkable technological features of the Jewellery Casting Furnace have garnered immense praise from the jewellery manufacturing industry. Several renowned jewellery manufacturers across the globe have incorporated this furnace into their production lines, testifying to its ability to optimize casting operations, increase productivity, and enhance the quality of their products.
Feedback from manufacturers who have embraced this innovative furnace has been overwhelmingly positive. They have reported significant improvements in cast quality, reduction in defects, enhanced production efficiency, and cost savings. The Jewellery Casting Furnace has proven to be a game-changer for industry professionals, empowering them to deliver superior craftsmanship and meet the growing demands of their discerning clientele.
Conclusion:
With the introduction of the Jewellery Casting Furnace, this industry-leading company has once again raised the bar in the jewellery manufacturing sector. By combining cutting-edge technology, customizability, and precision control, this furnace is transforming the casting process and setting new industry standards. Manufacturers now have a reliable and efficient tool at their disposal to create exquisite jewellery, increase productivity, and deliver exceptional results. With its widespread adoption, the Jewellery Casting Furnace is shaping the future of the jewellery manufacturing industry.
Company News & Blog
Revolutionizing Castables: Innovative Materials for High-Temperature Applications" could be rewritten as "Innovative Castable Materials for High-Temperature Applications.
[News Title]: Castables Announces Ground-Breaking Innovations for Enhanced Industrial Efficiency[Subtitle]: Pioneering Castables Reinvents the Industry with Cutting-Edge Solutions[date][City], [State]: Castables, a global leader in industrial manufacturing, has announced a series of ground-breaking innovations designed to revolutionize various sectors of the industry. As part of consistently pushing the boundaries of what is possible, Castables aims to enhance industrial efficiency, reduce costs, and minimize environmental impact. With an unwavering commitment to delivering cutting-edge solutions, Castables is poised to create a lasting impact on the world of industrial manufacturing.Since its inception in [year], Castables has positioned itself at the forefront of the industry, setting new industry standards with its relentless pursuit of innovation. By combining state-of-the-art technology with a deep understanding of market needs, Castables has consistently delivered exceptional solutions to its clients worldwide.Castables' expertise lies in the development and production of castable materials, including the removal of brand name, a flagship product in their extensive portfolio. These high-performance castables boast extraordinary resistance to high temperatures, wear, and corrosion, making them highly sought-after in a wide range of industries.In line with their commitment to sustainable manufacturing practices, Castables has recently introduced the innovative {} technology. This breakthrough technology minimizes environmental impact by significantly reducing carbon emissions throughout the production process. By harnessing {}, Castables has taken a significant step towards a greener and more sustainable future.Furthermore, Castables has also invested heavily in research and development to anticipate evolving industry needs. The company's cutting-edge research facilities are equipped with state-of-the-art equipment and staffed by a team of highly skilled researchers, engineers, and scientists. This dedicated team works tirelessly to develop innovative solutions that address both current and future challenges faced by the industry.One of Castables' recent achievements is the introduction of the {} system, a game-changer for the construction industry. This cutting-edge system enables faster and more efficient construction processes, reducing project completion times and costs. Additionally, the {} system ensures superior quality and durability, enhancing the longevity of structures in various sectors, ranging from housing to infrastructure.Another innovation by Castables is the breakthrough {} technology, which has revolutionized the efficiency of industrial machinery. This technology optimizes energy consumption, resulting in impressive cost savings for manufacturers. By significantly reducing energy waste, {} enables companies to maximize production output while minimizing their environmental footprint.Castables' commitment to client satisfaction is unwavering. The company provides comprehensive technical support, ensuring that clients receive personalized guidance throughout their projects. Castables' team of experts collaborates closely with clients to understand their specific requirements, offering tailored solutions to meet their unique needs. This client-centric approach has been a cornerstone of Castables' success, fostering long-lasting partnerships around the globe.Looking ahead, Castables is dedicated to further advancing the industry through its relentless pursuit of innovation. By combining cutting-edge technology, sustainable practices, and a client-centric approach, Castables is poised to continue shaping the landscape of industrial manufacturing.About CastablesCastables is a world-leading industrial manufacturing company that specializes in the development and production of high-performance castable materials. With an unwavering commitment to innovation, sustainability, and client satisfaction, Castables consistently delivers ground-breaking solutions to industries worldwide. Through a combination of cutting-edge technology, research and development, and personalized support, Castables is revolutionizing the industrial manufacturing sector.For more information about Castables and its innovative solutions, please visit [website].-End of Release-
Efficient and Eco-Friendly Melting Furnace: Revolutionizing Industrial Metal Manufacturing
Al Melting Furnace revolutionizes the Metal IndustryThe metal industry is one of the oldest and most important industries in the world, and it’s constantly evolving alongside the technological developments of modern times. One of the most important pieces of machinery in the industry is the melting furnace, which plays a critical role in the manufacturing of metal products. The latest innovation in this field is the Al Melting Furnace, which is setting new standards for efficiency, effectiveness, and safety. According to the company behind the Al Melting Furnace (need remove brand name), this equipment is designed to help businesses in the metal industry achieve superior results in terms of productivity, quality, and profitability. The Al Melting Furnace is built on the latest technology, which makes it capable of handling a wide range of materials, from iron to aluminum, while minimizing energy consumption, reducing emissions, and ensuring the purity of the end product. What makes the Al Melting Furnace stand out is its versatility. With its advanced features and customizable options, the Al Melting Furnace can be tailored to fit the needs of different businesses and industries. It comes in various sizes and capacities, with options for fuel types, controls, and automation. This flexibility enables businesses to optimize their operations, reduce costs, and improve safety and environmental standards. In addition to its performance capabilities, the Al Melting Furnace is also praised for its user-friendliness. The control panel is intuitive and easy to operate, with clear instructions and real-time data feedback. The furnace is also designed with safety in mind, featuring automatic shut-off functions, emergency stop buttons, and protection against overloading or overheating. These safety features ensure that the furnace operates efficiently and effectively without posing a risk to the operators or the environment. The Al Melting Furnace is not only a game-changer for the industry in terms of its technical capabilities, but also its environmental impact. As sustainability becomes a growing concern for businesses across all sectors, the Al Melting Furnace comes as a welcome solution to reducing emissions and waste. The furnace utilizes state-of-the-art technologies that minimize carbon footprint, conserve energy, and reduce water consumption. It also generates fewer emissions than traditional furnaces, meeting and exceeding industry standards and regulations. As businesses look to invest in advanced technology to gain a competitive edge in the market, the Al Melting Furnace proves to be a wise choice in terms of its return on investment. By optimizing operations and reducing costs, businesses can increase their profitability while also improving their environmental footprint. The Al Melting Furnace offers a long-term solution that enhances productivity, quality, and safety for businesses across the metal industry. In conclusion, Al Melting Furnace is an innovative and versatile piece of machinery that is revolutionizing the metal industry. Its advanced technology and user-friendly features make it an attractive option for businesses looking to optimize their operations and reduce their environmental impact. As the industry continues to evolve, the Al Melting Furnace is well-positioned to meet the changing needs and expectations of businesses across the metal sector. It’s no wonder why this technology is taking the industry by storm.
Different Types of Refractory Materials: A Complete Guide
Title: Advancements in Refractory Materials Transform IndustriesIntroduction:Refractory materials have been an integral part of various industries, providing crucial resistance to extreme temperatures and chemical reactions. These materials are used in applications such as furnaces, kilns, reactors, and incinerators, where they play a vital role in maintaining operational efficiency. Today, we explore the latest advancements in refractory technology and its impact on industries worldwide.Background:Refractory materials are designed to withstand high temperatures and harsh environments, while also possessing excellent resistance to thermal shock, corrosion, and abrasion. They are commonly categorized into three types: acidic, basic, and neutral refractories, each suited for specific applications. As industries continue to evolve, the demand for more advanced refractory solutions has grown significantly.Company Introduction:{Company Name}, a leading manufacturer and supplier of refractory materials, has been at the forefront of innovation in this industry for many years. With their expertise, extensive R&D capabilities, and commitment to quality, {Company Name} has played a pivotal role in driving technological advancements in refractories.Types of Refractory Materials:1. Acidic Refractories:Acidic refractories primarily consist of silica, alumina, and varying proportions of other oxides. These materials possess excellent resistance to acidic environments, making them ideal for industries such as petrochemicals, energy, and metallurgy. Erosion-resistant acidic refractories have become increasingly popular due to their ability to withstand aggressive chemicals and high temperatures.2. Basic Refractories:Basic refractories are typically composed of magnesia, dolomite, or chrome-magnesia. They exhibit exceptional resistance to basic slag and alkaline environments, which makes them suitable for applications in the steel, cement, and non-ferrous metal industries. The high refractoriness and low thermal conductivity of basic refractories contribute to enhanced energy efficiency and extended equipment lifespan.3. Neutral Refractories:Neutral refractories have a high alumina content and possess excellent resistance to both acidic and basic environments. These materials find wide application in industries such as glass-making, ceramics, and incinerators. Their versatility and durability make them an ideal choice for processes where varied chemical environments are present.Advancements in Refractory Technology:1. Increased Thermal Efficiency:{Company Name}, working in collaboration with research institutions, has developed refractory materials with improved thermal conductivity. These advancements allow for enhanced heat transfer efficiency, resulting in reduced energy consumption and lower production costs for industries utilizing high-temperature processes.2. Enhanced Chemical Resistance:To address the increasing demand for resistance to aggressive chemicals, {Company Name} has developed advanced erosion-resistant refractories. These innovative materials exhibit superior corrosion resistance, enabling industries to operate in highly corrosive environments without compromising performance or durability.3. Longer Lifespan and Reduced Downtime:Through continuous research and development, {Company Name} has created refractory materials with extended lifespans. This improvement significantly reduces downtime associated with maintenance, resulting in enhanced operational efficiency and cost savings for industries relying on refractory-lined equipment.Conclusion:The continuous advancements in refractory materials and technology, spearheaded by {Company Name}, are revolutionizing industries worldwide. With improved thermal efficiency, enhanced chemical resistance, and extended lifespan, these refractory solutions are addressing the ever-evolving needs of industries. By utilizing these latest advancements, businesses can optimize their operations, reduce costs, and ensure safer and more sustainable processes. The future of refractory materials holds promise for industries looking to achieve greater efficiency and productivity in their operations.
Discover the Latest Innovation in Firebricks in South Africa
Firebricks in South Africa: Revolutionizing the Construction IndustrySouth Africa has long been known for its diverse landscape and rich mineral resources, but now the country is making waves in the construction industry with the introduction of innovative firebricks. These bricks are set to revolutionize the way buildings are designed and constructed, offering unparalleled durability and fire resistance.Firebricks South Africa, a pioneering company in the field, has been at the forefront of this groundbreaking technology. They have developed a range of firebricks that are not only aesthetically pleasing but also offer superior structural integrity when compared to traditional bricks. This is achieved by incorporating advanced materials and engineering techniques, ensuring that these firebricks are built to withstand the harshest conditions.One of the key advantages of using firebricks is their exceptional fire resistance. Traditional bricks can crack or crumble when exposed to high temperatures, compromising the structural integrity of buildings and posing a significant safety risk. However, firebricks have been specifically engineered to withstand intense heat without compromising their strength. This makes them ideal for use in fire-prone areas such as industrial complexes, warehouses, and even residential homes.In addition to their superior fire resistance, firebricks offer excellent insulation properties. This means that buildings constructed with these bricks can retain heat more effectively, helping to reduce energy consumption and lower heating costs. This is particularly important in South Africa, where extreme temperatures can be challenging to manage. The insulation provided by firebricks also ensures a more comfortable living or working environment, as the temperature remains stable and consistent.Furthermore, firebricks are incredibly durable, capable of withstanding the test of time. Traditional bricks are prone to erosion and degradation over time, especially when exposed to harsh weather conditions. Firebricks, on the other hand, are less susceptible to such wear and tear, preserving the structural integrity of buildings for decades to come. This makes them an excellent long-term investment for developers and homeowners alike.Firebricks South Africa offers a wide range of firebrick options to cater to various construction needs. From standard-sized bricks to customized shapes and sizes, they have a solution for every project. Their team of industry experts works closely with architects, engineers, and contractors to understand specific requirements and provide tailored solutions. This collaborative approach ensures that each project is executed seamlessly, meeting and exceeding client expectations.The company takes pride in its commitment to sustainability. Firebricks South Africa uses environmentally friendly manufacturing processes, minimizing waste generation, and reducing carbon emissions. By employing sustainable practices, they contribute to a greener future while providing high-quality construction materials.Firebricks South Africa has quickly gained recognition for its cutting-edge technology and exceptional customer service. Their growing client base includes major construction companies, architectural firms, and individual homeowners. The positive feedback and testimonials from satisfied clients further cement the company's reputation as a leader in the firebrick industry.As South Africa continues to grow and develop, the demand for innovative construction materials is on the rise. Firebricks, with their unparalleled fire resistance, insulation properties, and durability, are transforming the construction landscape. Firebricks South Africa remains at the forefront of this revolution, constantly pushing the boundaries of what is possible in the construction industry. With their commitment to quality, sustainability, and client satisfaction, they are well on their way to becoming a household name in the field.
High-Quality Refractory Cement for Fire Bricks: Essential for Heat-Resistant Construction
Fire Brick Refractory Cement (need remove brand name) – A Game Changer in the Construction IndustryFire Brick Refractory Cement (need remove brand name) is a time-tested and eco-friendly product that has proven its effectiveness in construction and manufacturing industries. It is a type of cement used to bind fire bricks, which are heat-resistant bricks that can withstand extremely high temperatures. Fire bricks are commonly used to line fireplaces, chimneys, pizza ovens, and industrial furnaces.Refractory cement is an essential component of the construction industry, and the demand for this product has increased significantly in recent years. With the growth of the industrial sector and increasing demand for energy, the need for heat-resistant materials has become more critical than ever before. Refractory cement is designed to withstand temperatures of up to 1600°C, making it an ideal material for applications that require high-temperature resistance.Fire Brick Refractory Cement (need remove brand name) is engineered to ensure durability, strength, and thermal stability. It is made from high-quality raw materials and is designed to provide excellent resistance to thermal shock and abrasion. The cement can be used for a variety of applications, including:● Furnaces and kilns● Lining boiler fireboxes● Incinerators● Steel and iron production● Cooking ovensThe cement has also been used in the repair and maintenance of broken and cracked refractory bricks. Its superior bonding properties make it an excellent choice for repairing and reconstructing high-temperature linings. The cement has excellent adhesion properties that help in binding the fire bricks together, forming strong and durable structures.Aside from its heat-resistant properties, Fire Brick Refractory Cement (need remove brand name) is also environmentally friendly. It is made from natural materials that are free from harmful chemicals and contains no asbestos or silica. When used in construction, it emits no volatile organic compounds (VOCs), making it a safe and eco-friendly choice.The company that produces Fire Brick Refractory Cement (need remove brand name) is one of the leading manufacturers of refractory materials in the world. It has been in operation for over 50 years and has built a reputation as a quality supplier of heat-resistant products. The company prides itself on using the latest technology and adhering to the strictest quality control measures to ensure that their products are of the highest quality.Their team of experts continuously works on developing innovative products that meet the growing demands of the construction and manufacturing industries. Fire Brick Refractory Cement (need remove brand name) is just one of the many products that this company has developed to cater to the needs of their clients.The company's commitment to excellence is further reinforced by its focus on customer satisfaction. They actively solicit customer feedback to improve their products and services, ensuring that their clients receive the best possible experience. Their customer service team is knowledgeable and responsive, providing timely and efficient solutions to customer queries and concerns.In conclusion, Fire Brick Refractory Cement (need remove brand name) is a game-changer in the construction industry. Its ability to withstand high temperatures, durability, and eco-friendliness make it an attractive choice for anyone looking to build or repair a structure that requires heat-resistant materials. The company that produces it is committed to providing high-quality products and services to its clients, making it a reliable supplier of refractory materials. With Fire Brick Refractory Cement (need remove brand name), clients can rest assured that they are getting a product that is not only effective but also sustainable.
Ceramic Fiber Products: Unveiling the Latest Innovations in Heat Insulation
Title: Enhanced Insulation Solution: Isowool Introduces Groundbreaking Ceramic Fiber TechnologyIntroduction (150 words):Isowool, a leading innovator in insulation solutions, has announced a groundbreaking technology in the field of ceramic fibers. Built upon decades of research and development, the new product aims to revolutionize insulation systems across industries with enhanced thermal performance, durability, and energy efficiency. This cutting-edge ceramic fiber, devoid of hazarous materials, offers a sustainable solution while fulfilling the stringent safety standards that are mandated across various sectors. Isowool's commitment to delivering superior insulation products, combined with their extensive expertise in thermal insulation, make them well-positioned to address the increasing market demands for sustainable, durable, and high-performance thermal management solutions.Body:1. Advancements in Ceramic Fiber Technology: Meeting Industry Demands (200 words)Isowool's latest ceramic fiber technology represents a significant leap in the field of insulation solutions. This revolutionary offering combines superior thermal insulation properties with sustainable and environmentally friendly aspects, placing it at the forefront of the industry. Isowool's product emerges as a reliable solution that promises to drive energy efficiency, reduce carbon footprint, and improve productivity across various sectors, from manufacturing to construction.The use of advanced materials and cutting-edge manufacturing processes ensures the durability and longevity of the ceramic fiber. Isowool's ceramic fiber is capable of withstanding high temperatures and resisting chemical or mechanical stresses, making it an ideal choice for challenging and demanding applications. The product's superior thermal properties contribute to energy conservation and cost-effectiveness, thereby making it an attractive solution for businesses across diverse industries. 2. Applications Across Industries: Versatility and Adaptability (200 words)One of the key advantages of Isowool's ceramic fiber is its versatility and adaptability to various industrial applications. Its high-temperature resistance and ability to withstand harsh environments make it an ideal choice for industries such as metal processing, power generation, automotive, aerospace, and more. In metal processing, where high-temperature furnaces and kilns are utilized, Isowool's ceramic fiber provides excellent insulation, ensuring energy efficiency and cost savings. The automotive and aerospace sectors benefit from the product's lightweight nature and exceptional thermal insulation, enhancing both fuel efficiency and passenger comfort.Furthermore, Isowool's ceramic fiber finds extensive use in the construction industry, addressing insulation needs across commercial, residential, and infrastructure development projects. By providing a high level of fire resistance and thermal insulation, the product helps in promoting sustainable and energy-efficient construction practices.3. Sustainability and Safety: Complying with Environmental Norms (200 words)In line with global sustainability goals, Isowool's ceramic fiber technology stands as a testament to their commitment to environmental consciousness. Unlike traditional insulation materials, Isowool's solution is free from hazardous substances such as asbestos, reducing health risks for both installers and end-users.Additionally, Isowool's streamlined manufacturing processes prioritize energy efficiency and low waste generation, thereby minimizing the company's carbon footprint. Incorporating this environmentally friendly insulation product can contribute significantly to meeting energy consumption reduction targets and building eco-friendly infrastructures.Moreover, the elimination of hazardous materials complies with strict industry safety standards, ensuring a safer working environment for employees and reducing the risk of occupational health issues. Isowool's focus on sustainable and safe products sets a benchmark for the industry, urging other insulation manufacturers to follow suit and prioritize environmentally responsible solutions.Conclusion (150 words):Isowool's introduction of their innovative ceramic fiber technology propels the insulation industry toward sustainable and energy-efficient practices. With its enhanced thermal properties, adaptability across diverse industries, and commitment to sustainability and safety, Isowool's ceramic fiber is set to redefine the status quo of thermal insulation systems. This groundbreaking product caters to the demands of numerous sectors, from manufacturing to construction, providing them with a reliable, durable, and high-performance solution that contributes to a greener tomorrow. As their cutting-edge insulation solution continues to gain traction, Isowool stands as a vanguard of technological progress, propelling various industries toward a more sustainable and energy-efficient future.
Researchers Develop New Method for Creating Stronger Alloys
Arc Melting Technology Paves the Way for Innovative Applications in Material ScienceWhen it comes to material science, researchers have been constantly exploring ways of producing metals and alloys that exhibit superior quality and properties. The process of melting and casting metals has been a conventional technique for large-scale production of metals since the middle ages. However, the conventional process of furnace melting has limitations, such as poor homogeneity, impurity contamination, and poor quality of the final product. Therefore, technological advancements are being made to improve the efficiency and effectiveness of the melting and casting processes.One such advancement in the field of material science is the arc melting technology, which has revolutionized the way of producing high-quality metals and alloys. Arc melting involves melting materials using an electric arc, which transfers heat to the material through a graphite electrode. The heat from the arc melts the material, fusing it together to form a homogeneous mixture. This technology is efficient and fast, creating high-quality alloys that meet the stringent requirements of advanced industries.The arc melting technology is widely used in research laboratories and is gaining acceptance in industry applications ranging from aerospace to biomedicine. This is due to its ability to produce alloys with high purity, uniformity, and superior properties that are difficult or impossible to obtain with conventional melting techniques.One of the leading companies that specialize in arc melting technology is (need remove brand name), which is at the forefront of developing and producing advanced alloys. The company has a team of experts who work closely with customers to design and produce customized materials based on their specific needs and applications. (Need remove brand name) is known for providing high-quality materials with exceptional characteristics, such as high strength, thermal conductivity, and corrosion resistance, making them ideal for use in critical and challenging environments.The company has a fully equipped laboratory and manufacturing facility that allows them to carry out extensive research and development of new alloys. They use state-of-the-art equipment to ensure that every alloy produced meets the highest standards of quality and purity. Their products are widely used in aerospace, biomedicine, electronics, and many other critical applications.In the aerospace industry, arc melting has been instrumental in producing high-performance alloys that meet the stringent requirements of aircraft engines. The excellent thermal resistance and chemical stability of these alloys make them ideal for use in the harsh and demanding environment of jet engines.In the biomedical field, arc melting has enabled the production of advanced alloys that are biocompatible, making them suitable for implants and medical instrument applications. The high purity and uniformity of the alloys ensure that they do not cause any adverse reactions in the human body.In the electronics industry, arc melting has played a crucial role in the development of alloys that possess superior electrical and thermal conductivity properties. These alloys find widespread use in the production of microelectronic devices, such as transistors and sensors.The versatility and efficiency of arc melting technology have made it a game-changer in material science. Researchers and companies are continuously exploring new ways of using arc melting to create innovative alloys that have never existed before. The technology has opened up endless possibilities in the field of material science, making it possible to produce materials with unprecedented properties and functionality.In conclusion, arc melting technology is a powerful tool that has transformed the way of producing advanced alloys. The technology offers numerous advantages over conventional melting techniques, including high purity, uniformity, and quality of the final product. The technology is widely used in various industries because of its ability to create materials with exceptional characteristics that meet the stringent requirements of advanced applications. With companies such as (need remove brand name) at the forefront of developing and producing advanced alloys, the arc melting technology is poised to revolutionize the way we think, design, and manufacture materials.
Metal Smelting Plant in Ohio Shut Down for Environmental Violations" Rewritten SEO title: "Ohio Metal Smelting Plant Closed for Environmental Infractions
Crucible Smelting Paves the Way for Sustainable Metal RefiningCrucible smelting is rapidly emerging as a sustainable and cost-effective method of refining metal at scale. While this method has been around for centuries, modern technology has enabled its application in many industrial settings.One company at the forefront of this trend is ABC Metals, an industry leader in sustainable metal refining. ABC Metals has been refining precious metals for over 50 years and has built a stellar reputation for its attention to detail and commitment to environmental sustainability.ABC Metals has embraced crucible smelting as a method of refining metals. Crucible smelting involves heating metals to their melting point and allowing them to flow into a container called a crucible. The molten metal is then poured into a mold to create a desired shape or alloy.What sets crucible smelting apart from other methods of refining metals is its high degree of accuracy and control. The process allows for precise control over temperature, pressure, and other variables, ensuring that the finished product is of high quality and meets a specific set of specifications.ABC Metals has taken this process to the next level, implementing cutting-edge technology to refine metals in an environmentally sustainable way. The company has invested heavily in equipment and processes that minimize waste and reduce energy consumption, leading to a significant reduction in its carbon footprint.Another benefit of crucible smelting is its ability to refine complex alloys that traditional methods might struggle with. The increased precision and control afforded by the process make it an ideal choice for creating high-purity metals and alloys, which are essential components of many industrial applications.ABC Metals has capitalized on this trend, partnering with companies across different industries to create specialized alloys that meet their unique needs. These partnerships have allowed the company to broaden its portfolio and stay at the forefront of innovation within the industry.One such partnership is with a technology firm that produces components for the renewable energy sector. The company relies on ABC Metals to produce high-purity copper alloys that meet strict performance requirements. Thanks to crucible smelting, ABC Metals is able to deliver consistent, high-quality products to this and other partners.ABC Metals’ focus on sustainable metal refining has also positioned the company as a leader in the circular economy. By minimizing waste and maximizing the use of resources, the company has created a closed loop that reduces the environmental impact of its operations.The benefits of this approach are not just environmental but also financial. By reducing waste and optimizing processes, ABC Metals has been able to drive down operating costs, making its products more competitive in the marketplace.In conclusion, crucible smelting is a game-changer in the world of metal refining, and ABC Metals is at the forefront of this trend. By embracing this process and leveraging cutting-edge technology, the company has positioned itself as a leader in sustainable metal refining.As the world moves towards a more sustainable future, companies like ABC Metals will continue to play an essential role in creating the products and materials that are essential to our daily lives. Their commitment to environmental sustainability and innovation will help ensure that this transition is a success.
Maximizing the Benefits of Refractories for Optimal Performance
Title: Utilization of Refractories in Various Industries Aids Production EfficienciesIntroduction:Refractories are indispensable materials widely used across a range of industries for their ability to withstand high temperatures and aggressive environments. These substances play a critical role in the manufacturing processes of steel, cement, glass, ceramics, and a variety of other industries. The utilization of refractories ensures enhanced production efficiencies, improved product quality, and reduced energy consumption, making them an essential component in modern industrial applications.Key Characteristics of Refractories:Refractories are non-metallic materials with high melting points, excellent thermal shock resistance, and stability at extreme temperatures. They are designed to withstand significant pressure, chemical attacks, and abrasion, making them integral to the production processes.Refractories in the Steel Industry:The steel industry is the largest consumer of refractories, utilizing them in several key areas of production. Refractories line the furnaces, electric arc furnaces, and ladles, providing insulation and protection against the corrosive effects of molten metals and slag. They help maintain high temperatures and protect the vessel walls, resulting in improved energy efficiency and longer-lasting equipment. The utilization of high-quality refractories in steelmaking enables longer campaign life, reduced downtime, and improved steel quality.Refractories in the Cement Industry:Refractories find extensive use in the cement industry, primarily in kilns and cement rotary kilns. These components are subjected to harsh conditions, including extreme temperatures and chemical reactions. Refractories provide insulation, corrosion resistance, and wear protection, thus ensuring prolonged kiln life, reduced maintenance costs, and enhanced energy efficiency. By utilizing advanced refractories, cement manufacturers can optimize their production processes, resulting in higher-quality cement and reduced environmental impact.Refractories in the Glass Industry:The glass industry relies heavily on refractories for its manufacturing operations, particularly in glass furnaces. Refractories, such as silica bricks, zirconia, and alumina-based materials, are used as linings to withstand the extreme temperatures required for glass melting and shaping. Refractories enable steady heat distribution, protect against chemical reactions, and minimize energy losses. By employing effective refractory solutions, glass manufacturers can achieve maximum production output while maintaining consistent quality standards.Refractories in the Ceramics Industry:The ceramics industry heavily depends on refractories for various processes, including firing, sintering, and glazing. Refractories help provide an ideal thermal environment required for ceramic material transformation. High-quality refractory bricks, castables, and ceramic fibers ensure uniform heat distribution, controlled thermal gradients, and effective insulation throughout the firing process. Deploying suitable refractory materials enables ceramic manufacturers to achieve consistent product quality, minimize wastage, and reduce energy consumption.Developments in Refractory Technology:Continuous research and development in refractory technology have led to significant advancements, resulting in improved performance and cost-effectiveness. The use of advanced monolithic refractories, reinforced with specialty fibers and binders, enhances the overall strength and durability of refractory linings. Besides, the incorporation of nanotechnology in refractory manufacturing has shown promising results in terms of improving thermal stability, reducing material consumption, and extending product lifespan.Environmental Considerations:As industries globally strive to reduce their carbon footprint, refractories have a crucial role to play in achieving sustainability targets. There is a growing emphasis on developing eco-friendly refractories with lower emissions and increased recyclability. Sustainable refractory solutions contribute to greener production processes, reduced energy consumption, and minimized waste generation, promoting a more environmentally conscious industrial sector.Conclusion:The widespread utilization of refractories across various industries highlights their crucial role in enhancing production efficiencies, reducing downtime, and improving product quality. The continuous improvements in refractory technology, along with an increasing focus on sustainability, will further drive their demand. Through a combination of continuous innovation and responsible manufacturing practices, refractory manufacturers can support the evolving needs of industries while adhering to environmental standards, thus contributing to a sustainable and efficient industrial landscape.
Exploring the Benefits of Ceramic Cloth Insulation for Enhanced Energy Efficiency
Ceramic Cloth Insulation Revolutionizing Heat Control in IndustriesInnovation and sustainable solutions have become increasingly important in today's industrial landscape. Industries are constantly seeking ways to enhance efficiency, reduce energy consumption, and mitigate environmental impacts. One company emerging as a frontrunner in this quest is {Ceramic Cloth Insulation}, whose cutting-edge product is revolutionizing heat control in various sectors.{Ceramic Cloth Insulation}, a global leader in thermal management solutions, has developed a highly advanced material that provides superior insulation capabilities. Designed to withstand extreme temperatures and harsh conditions, their product has garnered immense attention from industries ranging from aerospace to automotive manufacturing, and even energy production.The key to {Ceramic Cloth Insulation}'s success lies in its unique composition. Made from a blend of high-quality ceramic fibers and specialized fabrics, the insulation material possesses exceptional thermal resistance characteristics. This innovative technology enables industries to effectively control and manage heat, achieving significant operational efficiencies.With the ability to withstand temperatures of up to 1,800 degrees Celsius, {Ceramic Cloth Insulation} ensures the utmost safety for industries operating under extreme conditions. This breakthrough development not only enhances the longevity of equipment but also reduces maintenance costs, making it an attractive choice for companies across the board.One of the primary advantages of {Ceramic Cloth Insulation} is its versatility. The material's flexibility allows for easy handling and installation, making it ideal for a wide range of applications. Whether it's insulating pipes in chemical plants, lining furnaces in steel manufacturing, or protecting cables in the aerospace industry, this product proves to be a versatile solution for heat management needs.Moreover, this innovative insulation material acts as a barrier to prevent unnecessary heat transfer. By significantly reducing heat loss and maximizing thermal efficiency, {Ceramic Cloth Insulation} contributes to substantial energy savings for industrial plants. This not only lowers operational costs but also aligns with industries' growing focus on sustainable practices.The positive impact of {Ceramic Cloth Insulation} on the environment cannot be overlooked. By reducing energy consumption, industries using this insulation material are effectively lowering their carbon footprint. This aligns with global efforts to combat climate change and promote sustainability, making {Ceramic Cloth Insulation} an essential component of the transition towards greener industrial practices.To further cater to industries' diverse needs, {Ceramic Cloth Insulation} offers a range of customized solutions. Their team of experts collaborates closely with clients to understand specific requirements and provide tailored insulation solutions that maximize efficiency. This customer-centric approach has earned {Ceramic Cloth Insulation} a reputation for excellence and reliability.As demand for innovative thermal management solutions continues to grow, {Ceramic Cloth Insulation} remains committed to pushing the boundaries of technology. Through ongoing research and development, the company aims to further enhance the performance of their insulation material and expand its application in various industries.By leveraging their expertise in thermal management, {Ceramic Cloth Insulation} is not only transforming heat control practices but also contributing to industrial efficiency and sustainability. With their advanced insulation solutions, industries can maximize operational productivity while reducing energy consumption and minimizing environmental impacts.In conclusion, the innovative and adaptable nature of {Ceramic Cloth Insulation} has positioned the company as a leader in thermal management solutions. With their exceptional insulation material, industries can now effectively control heat, ensuring safety, efficiency, and sustainability across various sectors. As the demand for sustainable practices continues to increase, {Ceramic Cloth Insulation} remains at the forefront of technological advancements in the industry.