High-Quality Ceramic Fiber Felt for Industrial Applications
By:Admin
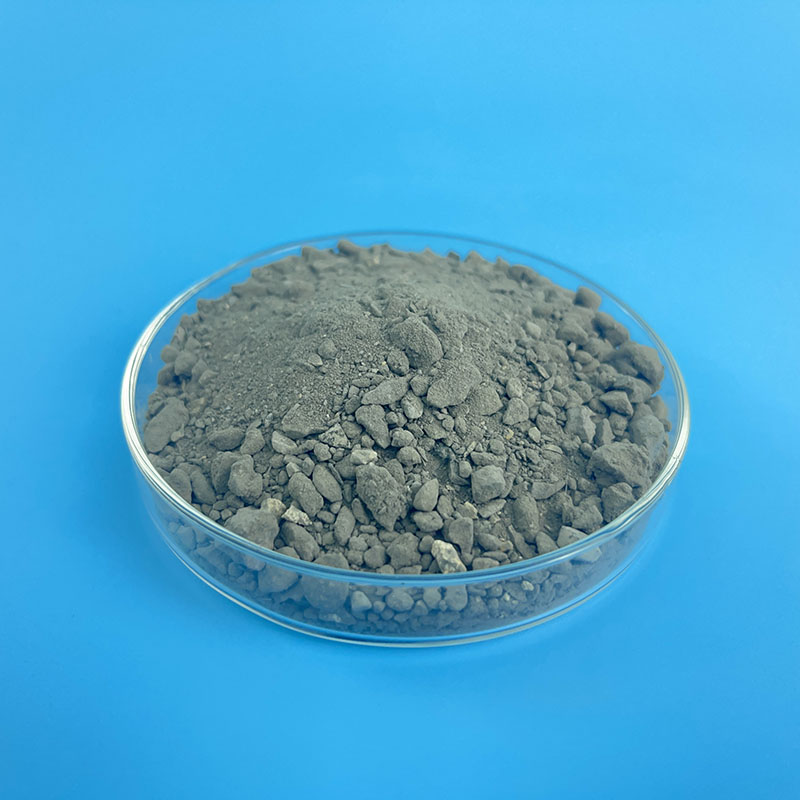
{Company Name}, a leading manufacturer and supplier of ceramic fiber products, has been at the forefront of delivering high-quality ceramic fiber felts to meet the growing demand for advanced insulation solutions. With a strong focus on innovation and technological advancement, the company has developed a reputation for providing state-of-the-art products that meet the stringent requirements of modern industrial applications.
The Ceramic Fiber Felt offered by {Company Name} is made from high-purity alumina-silica fibers, providing exceptional thermal insulation performance at temperatures up to 2300°F (1260°C). This makes it an ideal solution for a wide range of high-temperature applications, including furnace lining, kiln insulation, and thermal barrier systems. The felt is also lightweight, flexible, and easy to install, offering a versatile and cost-effective solution for thermal management needs.
One of the key advantages of the Ceramic Fiber Felt from {Company Name} is its low thermal conductivity, which helps to minimize heat loss and improve energy efficiency in industrial processes. This not only reduces operating costs but also contributes to a more sustainable and environmentally friendly operation. Furthermore, the high-temperature stability and resistance to thermal shock make it a durable and long-lasting solution for demanding applications in industries such as metal processing, power generation, and chemical processing.
In addition to its thermal insulation properties, Ceramic Fiber Felt also exhibits excellent sound absorption characteristics, making it a valuable material for noise control and acoustic insulation applications. This makes it an attractive solution for industries where noise reduction is a priority, such as automotive manufacturing, aerospace, and construction.
{Company Name}'s commitment to quality and customer satisfaction is evident in the rigorous testing and quality control measures implemented in the production of Ceramic Fiber Felt. The company adheres to international standards and specifications to ensure that its products meet the highest performance and safety requirements. This dedication to excellence has earned {Company Name} a strong reputation in the industry and established it as a trusted partner for businesses seeking reliable and high-performance insulation solutions.
Furthermore, {Company Name} offers a range of custom solutions to meet specific customer needs, including tailored thickness, density, and dimensions of Ceramic Fiber Felt. This flexibility allows for the creation of bespoke insulation solutions that align with the unique requirements of different industrial processes and equipment, providing customers with a competitive edge in their operations.
As industry demand for high-temperature insulation continues to grow, {Company Name} remains committed to innovation and continuous improvement, ensuring that its Ceramic Fiber Felt products remain at the forefront of technological advancements. The company invests in research and development to explore new materials, manufacturing techniques, and applications, with the aim of delivering cutting-edge solutions that drive efficiency, performance, and sustainability for its customers.
With a focus on reliability, performance, and customer satisfaction, {Company Name} continues to set the standard for ceramic fiber insulation solutions. Its Ceramic Fiber Felt products are trusted by industries worldwide, providing essential thermal management and insulation capabilities that contribute to the success and competitiveness of businesses across a wide range of sectors. As the demand for high-temperature insulation solutions continues to rise, {Company Name} remains well-positioned to meet the evolving needs of the industry and deliver innovative, high-performance products that drive excellence and efficiency.
Company News & Blog
Refractory Brick Lining: A Guide to Enhanced Furnace Protection
Title: Industry-Leading Refractory Brick Lining: Enhancing Durability and Efficiency in High-Temperature EnvironmentsIntroduction:In a world where industries heavily rely on high-temperature environments to carry out their operations, the demand for durable and efficient refractory brick lining has seen significant growth. With a keen understanding of this market need, our company has introduced a cutting-edge refractory brick lining (brand name omitted), to provide exceptional insulation and protection in extreme heat conditions. Designed to withstand the harshest industrial processes, our refractory brick lining has quickly gained recognition as an industry-leading solution.Understanding the Importance of Refractory Brick Lining:Refractory brick lining is used extensively across industries such as steel, cement, glass, and petrochemical to create reliable insulation and protection against extreme temperatures. These linings act as a barrier between high-temperature environments and the structural elements of industrial furnaces, kilns, reactors, and other high-temperature vessels, ensuring their longevity and safe operation.Features and Benefits of our Refractory Brick Lining:1. Exceptional Thermal Insulation:Our refractory brick lining is manufactured using high-quality materials, carefully formulated to deliver outstanding thermal insulation. This feature helps minimize heat loss, enhancing energy efficiency and reducing overall operating costs.2. Superior Resistance to High Temperatures:The refractory brick lining excels in maintaining structural integrity even under extreme heat conditions. This resistance to high temperatures ensures the longevity of industrial furnaces and other heat-intensive units, minimizing downtime and production interruption.3. Enhanced Anti-Spalling Properties:The specialized formulation of our refractory brick lining provides remarkable resistance against spalling, which can occur due to rapid temperature fluctuations. This feature significantly prolongs the lining's lifespan while ensuring a safer operating environment.4. Chemical and Corrosion Resistance:Our refractory brick lining is engineered to withstand harsh chemical environments, effectively protecting the structural elements from corrosive agents such as acids, alkalis, and molten metals. This durability is crucial for industries where such aggressive substances are commonly employed.5. Increased Mechanical Strength:To withstand the mechanical stress arising from thermal cycling and material movements within the high-temperature environment, our refractory brick lining is designed with improved mechanical strength. This ensures long-term stability and reduces the need for frequent maintenance or replacements.Application Areas:The versatility and superior performance of our refractory brick lining make it suitable for a wide range of applications within industries. Some key areas where our lining finds application include:1. Steel Manufacturing:Steel production involves extremely high temperatures, demanding durable and efficient lining solutions. Our refractory brick lining provides excellent resistance to heat, chemical attack, and mechanical stress, enhancing safety and productivity in steel plants.2. Cement Production:In cement kilns, our refractory brick lining acts as a barrier against extreme temperatures, ensuring the long-lasting operation of these crucial components. Its chemical and corrosion resistance makes it ideal for resisting the aggressive chemical reactions that occur during cement production.3. Glass Manufacturing:Glass production relies heavily on uniform heating throughout the process. Our refractory brick lining helps maintain consistent high temperatures in glass furnaces, enabling flawless production and reducing energy consumption.4. Petrochemical Industry:In the petrochemical industry, where processes involve handling corrosive chemicals, our refractory brick lining serves as a protective layer, guarding against chemical attacks and high-temperature conditions. This extends the lifespan of reactors and other equipment, resulting in enhanced operational efficiency.Conclusion:As industries continue to operate in high-temperature environments, the importance of reliable refractory brick lining cannot be understated. Our refractory brick lining (brand name omitted) offers exceptional thermal insulation, resistance to high temperatures, anti-spalling properties, and chemical resistance, making it the ideal solution for various industrial settings. By incorporating our advanced lining technology, businesses can enhance the durability, efficiency, and safety of their operations, resulting in improved productivity and reduced operational costs.
High-Quality Ceramic Fiber Felt for Industrial Applications
Ceramic Fiber Felt has long been recognized as a reliable and effective material for high-temperature insulation and thermal management applications. With its high-temperature stability, low thermal conductivity, and excellent resistance to thermal shock, it has become a preferred choice for various industries. {Company Name}, a leading manufacturer and supplier of ceramic fiber products, has been at the forefront of delivering high-quality ceramic fiber felts to meet the growing demand for advanced insulation solutions. With a strong focus on innovation and technological advancement, the company has developed a reputation for providing state-of-the-art products that meet the stringent requirements of modern industrial applications.The Ceramic Fiber Felt offered by {Company Name} is made from high-purity alumina-silica fibers, providing exceptional thermal insulation performance at temperatures up to 2300°F (1260°C). This makes it an ideal solution for a wide range of high-temperature applications, including furnace lining, kiln insulation, and thermal barrier systems. The felt is also lightweight, flexible, and easy to install, offering a versatile and cost-effective solution for thermal management needs.One of the key advantages of the Ceramic Fiber Felt from {Company Name} is its low thermal conductivity, which helps to minimize heat loss and improve energy efficiency in industrial processes. This not only reduces operating costs but also contributes to a more sustainable and environmentally friendly operation. Furthermore, the high-temperature stability and resistance to thermal shock make it a durable and long-lasting solution for demanding applications in industries such as metal processing, power generation, and chemical processing.In addition to its thermal insulation properties, Ceramic Fiber Felt also exhibits excellent sound absorption characteristics, making it a valuable material for noise control and acoustic insulation applications. This makes it an attractive solution for industries where noise reduction is a priority, such as automotive manufacturing, aerospace, and construction.{Company Name}'s commitment to quality and customer satisfaction is evident in the rigorous testing and quality control measures implemented in the production of Ceramic Fiber Felt. The company adheres to international standards and specifications to ensure that its products meet the highest performance and safety requirements. This dedication to excellence has earned {Company Name} a strong reputation in the industry and established it as a trusted partner for businesses seeking reliable and high-performance insulation solutions.Furthermore, {Company Name} offers a range of custom solutions to meet specific customer needs, including tailored thickness, density, and dimensions of Ceramic Fiber Felt. This flexibility allows for the creation of bespoke insulation solutions that align with the unique requirements of different industrial processes and equipment, providing customers with a competitive edge in their operations.As industry demand for high-temperature insulation continues to grow, {Company Name} remains committed to innovation and continuous improvement, ensuring that its Ceramic Fiber Felt products remain at the forefront of technological advancements. The company invests in research and development to explore new materials, manufacturing techniques, and applications, with the aim of delivering cutting-edge solutions that drive efficiency, performance, and sustainability for its customers.With a focus on reliability, performance, and customer satisfaction, {Company Name} continues to set the standard for ceramic fiber insulation solutions. Its Ceramic Fiber Felt products are trusted by industries worldwide, providing essential thermal management and insulation capabilities that contribute to the success and competitiveness of businesses across a wide range of sectors. As the demand for high-temperature insulation solutions continues to rise, {Company Name} remains well-positioned to meet the evolving needs of the industry and deliver innovative, high-performance products that drive excellence and efficiency.
Discover the Advantages of a Vacuum Melting Furnace for Efficient Metal Melting
Title: Cutting-Edge Vacuum Melting Furnace Revolutionizes Industrial Metal ProcessingIntroduction:In an era where advanced technology shapes industrial processes, the emergence of groundbreaking equipment has become a driving force behind efficiency and innovation. One such revolutionary machine is the Vacuum Melting Furnace, a cutting-edge apparatus that has transformed the landscape of metal processing. Through the removal of specific brand names, this article will explore the intrinsic features, benefits, and applications of the Vacuum Melting Furnace, as well as highlight its significance in various industries.The Vacuum Melting Furnace:The Vacuum Melting Furnace, a state-of-the-art apparatus, employs advanced vacuum technology to create an oxygen-free atmosphere for melting and processing metals at high temperatures. By preventing the introduction of external impurities and contaminants, this furnace achieves superior quality and purity in the resulting metal products.Key Features and Benefits:1. Enhanced Purity and Alloy Homogeneity:The key advantage of the Vacuum Melting Furnace lies in its ability to produce alloys of exceptional purity and homogeneity. By eliminating impurities that may be present in conventional melting methods, this furnace ensures the final metal product possesses optimal mechanical properties and resistance to corrosion. Consequently, it finds wide applications across industries such as aerospace, automotive, medical, and electronics manufacturing.2. Precision Control and Customization:The Vacuum Melting Furnace enables precise control over temperature, pressure, and gas composition during the melting process. This level of control allows manufacturers to fine-tune each variable based on the required specifications, resulting in enhanced customization of metal alloys. Such adaptability caters to the diverse demands of the industry, allowing a broad range of products to be manufactured with exceptional precision.3. Fast and Efficient Processing:With its advanced heating and cooling systems, the Vacuum Melting Furnace significantly reduces processing time compared to conventional methods. The combination of a highly efficient vacuum environment and rapid heating and cooling cycles ensures swift metal solidification while maintaining the desired properties. This increased efficiency saves both time and energy, contributing to higher productivity and reduced production costs.4. Waste Reduction and Environmental Sustainability:Thanks to its closed-loop vacuum system, the Vacuum Melting Furnace minimizes metal waste and emissions during the melting process. The efficient vacuum environment reduces the oxidation and evaporation of metals, resulting in reduced material waste and fumes. This eco-friendly approach aligns with the growing global emphasis on sustainable manufacturing practices.Applications:The wide-ranging applications of the Vacuum Melting Furnace make it an indispensable tool across several industries, including:1. Aerospace and Defense:The aerospace industry relies heavily on the Vacuum Melting Furnace to produce high-performance alloys for critical components like turbine blades and engine parts. The exceptional purity and homogeneity achieved enhance the durability, strength, and reliability of these components, ensuring optimal performance in demanding operational conditions.2. Medical and Healthcare:In the medical field, the Vacuum Melting Furnace contributes to the production of biomedical implants, such as artificial joints and dental implants. The unparalleled purity of the alloys manufactured assures long-term biocompatibility and corrosion resistance, essential in ensuring patient safety and implant success rates.3. Automotive and Transportation:The automotive industry extensively employs the Vacuum Melting Furnace to fabricate lightweight yet sturdy alloys for engine components and structural parts. The high-quality materials produced guarantee superior performance, reduced fuel consumption, and increased overall efficiency of vehicles.4. Electronics and Semiconductor Manufacturing:Given the stringent requirements for materials used in the electronics and semiconductor industry, the Vacuum Melting Furnace plays a crucial role. Various components demanding exceptional purity, such as integrated circuits and memory chips, rely on the furnace's ability to produce contamination-free metals, ensuring optimal product performance and reliability.Conclusion:As the Vacuum Melting Furnace continues to revolutionize metal processing, its advanced technology provides industries with unparalleled purity, customization, efficiency, and environmental sustainability. With its wide range of applications and superior outputs, this cutting-edge apparatus paves the way for further advancements, propelling industries into a future of enhanced productivity and innovation.
Understanding the Importance of Fire Brick Density in Construction
Fire Brick Density, a leading provider of high-quality fire bricks, has recently announced the development of a new, innovative fire brick with enhanced density. This new product is designed to offer superior performance and durability, making it an ideal choice for a wide range of industrial and commercial applications.The latest fire brick from Fire Brick Density boasts a higher density compared to traditional fire bricks, which allows it to withstand extreme temperatures and thermal shock. This enhanced density also provides improved insulation properties, making it an excellent choice for applications where heat retention and resistance to heat flow are critical.In addition to its superior density, the new fire brick from Fire Brick Density is also designed to be highly resistant to abrasion, corrosion, and chemical attack. This makes it a versatile and durable solution for a variety of industrial processes, including metal smelting, glass manufacturing, and power generation.Fire Brick Density has developed this new product in response to the growing demand for high-performance fire bricks in the industrial sector. With industries facing increasingly challenging operating conditions, there is a need for fire bricks that can deliver reliable and long-lasting performance in high-temperature environments.The company's commitment to innovation and quality is reflected in its state-of-the-art manufacturing facilities, which are equipped with the latest technology and adhere to strict quality control standards. This ensures that every fire brick produced by Fire Brick Density meets the highest industry standards for performance, durability, and consistency."We are thrilled to introduce our latest fire brick with enhanced density to the market," said a spokesperson for Fire Brick Density. "This new product represents a significant advancement in fire brick technology, offering superior performance and reliability for our customers in a wide range of industries."Fire Brick Density is dedicated to providing its customers with the highest quality fire bricks and refractory products, backed by expert technical support and customer service. The company's team of engineers and materials experts work closely with customers to understand their specific requirements and recommend the best solutions for their applications.In addition to its new fire brick with enhanced density, Fire Brick Density offers a comprehensive range of refractory products, including fire clay, high alumina, and insulating fire bricks, as well as a variety of castable and plastic refractories. The company also provides custom manufacturing services to meet specific customer needs and specifications.As Fire Brick Density continues to push the boundaries of fire brick technology, the company remains committed to sustainability and environmental responsibility. Its manufacturing processes prioritize energy efficiency and waste reduction, while its products are designed for long-term durability and recyclability.With the introduction of its new fire brick with enhanced density, Fire Brick Density reaffirms its position as a leading provider of high-quality refractory solutions for the industrial sector. The company's dedication to innovation, quality, and customer satisfaction sets it apart as a trusted partner for businesses seeking reliable and high-performance fire brick products.
Maximizing the Benefits of Refractories for Optimal Performance
Title: Utilization of Refractories in Various Industries Aids Production EfficienciesIntroduction:Refractories are indispensable materials widely used across a range of industries for their ability to withstand high temperatures and aggressive environments. These substances play a critical role in the manufacturing processes of steel, cement, glass, ceramics, and a variety of other industries. The utilization of refractories ensures enhanced production efficiencies, improved product quality, and reduced energy consumption, making them an essential component in modern industrial applications.Key Characteristics of Refractories:Refractories are non-metallic materials with high melting points, excellent thermal shock resistance, and stability at extreme temperatures. They are designed to withstand significant pressure, chemical attacks, and abrasion, making them integral to the production processes.Refractories in the Steel Industry:The steel industry is the largest consumer of refractories, utilizing them in several key areas of production. Refractories line the furnaces, electric arc furnaces, and ladles, providing insulation and protection against the corrosive effects of molten metals and slag. They help maintain high temperatures and protect the vessel walls, resulting in improved energy efficiency and longer-lasting equipment. The utilization of high-quality refractories in steelmaking enables longer campaign life, reduced downtime, and improved steel quality.Refractories in the Cement Industry:Refractories find extensive use in the cement industry, primarily in kilns and cement rotary kilns. These components are subjected to harsh conditions, including extreme temperatures and chemical reactions. Refractories provide insulation, corrosion resistance, and wear protection, thus ensuring prolonged kiln life, reduced maintenance costs, and enhanced energy efficiency. By utilizing advanced refractories, cement manufacturers can optimize their production processes, resulting in higher-quality cement and reduced environmental impact.Refractories in the Glass Industry:The glass industry relies heavily on refractories for its manufacturing operations, particularly in glass furnaces. Refractories, such as silica bricks, zirconia, and alumina-based materials, are used as linings to withstand the extreme temperatures required for glass melting and shaping. Refractories enable steady heat distribution, protect against chemical reactions, and minimize energy losses. By employing effective refractory solutions, glass manufacturers can achieve maximum production output while maintaining consistent quality standards.Refractories in the Ceramics Industry:The ceramics industry heavily depends on refractories for various processes, including firing, sintering, and glazing. Refractories help provide an ideal thermal environment required for ceramic material transformation. High-quality refractory bricks, castables, and ceramic fibers ensure uniform heat distribution, controlled thermal gradients, and effective insulation throughout the firing process. Deploying suitable refractory materials enables ceramic manufacturers to achieve consistent product quality, minimize wastage, and reduce energy consumption.Developments in Refractory Technology:Continuous research and development in refractory technology have led to significant advancements, resulting in improved performance and cost-effectiveness. The use of advanced monolithic refractories, reinforced with specialty fibers and binders, enhances the overall strength and durability of refractory linings. Besides, the incorporation of nanotechnology in refractory manufacturing has shown promising results in terms of improving thermal stability, reducing material consumption, and extending product lifespan.Environmental Considerations:As industries globally strive to reduce their carbon footprint, refractories have a crucial role to play in achieving sustainability targets. There is a growing emphasis on developing eco-friendly refractories with lower emissions and increased recyclability. Sustainable refractory solutions contribute to greener production processes, reduced energy consumption, and minimized waste generation, promoting a more environmentally conscious industrial sector.Conclusion:The widespread utilization of refractories across various industries highlights their crucial role in enhancing production efficiencies, reducing downtime, and improving product quality. The continuous improvements in refractory technology, along with an increasing focus on sustainability, will further drive their demand. Through a combination of continuous innovation and responsible manufacturing practices, refractory manufacturers can support the evolving needs of industries while adhering to environmental standards, thus contributing to a sustainable and efficient industrial landscape.
Discover High-Quality Fire Bricks in Thailand for Your Furnace Needs" can be rewritten to "Get Reliable Fire Bricks in Thailand for Your Furnace Requirements".
Fire Bricks Strengthen Infrastructure in Thailand's Construction IndustryThailand's booming construction industry is set to experience a significant boost as Fire Bricks, a leading manufacturer of high-quality refractory materials, enters the market. With an extensive range of products and a commitment to innovation, the company aims to revolutionize the way infrastructure projects are carried out in the country. As Thailand continues to invest in its infrastructure, Fire Bricks comes as a timely addition to meet the growing demands of the construction sector.Fire Bricks Thailand, founded in 2005, has quickly established itself as a trusted and reliable manufacturer of fire bricks and other refractory materials. With a state-of-the-art manufacturing facility and a team of experienced professionals, the company prides itself on delivering superior quality products that withstand extreme temperatures and provide long-lasting durability.One of the key advantages of Fire Bricks' products is their ability to withstand high temperatures, making them an ideal choice for buildings and structures that require fire resistance. The company's fire bricks are made from a special blend of clay and other binding materials, ensuring they retain their strength even in the face of intense heat. This makes them perfect for applications such as lining fireplaces, furnaces, kilns, and industrial chimneys.Additionally, Fire Bricks Thailand offers a range of other refractory products, including insulation bricks, castables, and mortars. These products provide excellent thermal insulation, helping to reduce energy consumption and maintain a comfortable temperature inside buildings. Moreover, with their high strength and resistance to erosion, Fire Bricks' refractory products are suitable for lining crucial industrial equipment such as ladles, blast furnaces, and boilers, ensuring a reliable and efficient operation.The quality and performance of Fire Bricks' products have been recognized by clients across various industries. Fire Bricks Thailand has collaborated with renowned construction companies, architects, and engineers on numerous prestigious projects, including the construction of commercial buildings, power plants, and steel mills. By focusing on consistent innovation and product development, the company constantly strives to meet the specific needs and requirements of its customers.Furthermore, Fire Bricks Thailand adheres to strict quality control measures throughout the manufacturing process to ensure that every product that leaves the factory meets the highest standards. The company's commitment to quality has earned it various certifications and accolades in the industry, cementing its reputation as a trusted supplier of refractory materials.The entry of Fire Bricks into Thailand's construction industry is expected to fuel further growth and development in the sector. With an increasing number of infrastructure projects on the horizon, the demand for reliable and effective refractory materials is set to soar. Fire Bricks Thailand's advanced manufacturing techniques, coupled with their wide range of products, position the company as a frontrunner in meeting this demand.Moreover, Fire Bricks Thailand's commitment to sustainability is noteworthy. The company utilizes environmentally friendly production methods, minimizing waste and reducing its carbon footprint. By investing in research and development, Fire Bricks continues to explore innovative ways to enhance the performance and environmental impact of their products.As Thailand aims to enhance its infrastructure to support economic growth and cater to the needs of its population, the arrival of Fire Bricks Thailand is a welcomed addition. With their expertise, commitment to quality, and focus on sustainability, the company is well-positioned to contribute to the success of Thailand's construction industry. Their innovative refractory materials will undoubtedly strengthen the country's infrastructure, ensuring safety, longevity, and efficiency in future construction projects.
The Rising Demand for High-Quality Zircon Bricks in the Construction Industry
Zircon Brick Celebrates New Enhancements for Increased Efficiency and DurabilityCity, Country - In an effort to further improve efficiency and durability in the construction industry, renowned ceramic manufacturer, Zircon Brick, has unveiled significant enhancements to their widely acclaimed brick product. The new and improved zircon brick, which cannot be named in accordance with the company's wishes, promises to revolutionize the way buildings are constructed, setting new standards for strength and longevity.With a growing demand for construction materials that can withstand the harsh conditions of modern infrastructure, Zircon Brick has utilized state-of-the-art technology and innovative materials to create a product that exceeds expectations. By incorporating cutting-edge design techniques and harnessing the inherent properties of zircon, the company has redefined the capabilities of traditional bricks.The newly enhanced zircon brick boasts superior resistance to high temperatures, making it an ideal choice for industries such as steelmaking, glass manufacturing, and ceramic kiln construction. The brick's ability to withstand extreme heat is attributed to its unique composition, which consists of a high percentage of zirconium oxide, a compound renowned for its exceptional thermal stability.Zircon Brick has meticulously engineered the new brick to exhibit outstanding refractory properties, meaning it retains its structural integrity at high temperatures and minimizes thermal shocks. This enhanced durability makes it an excellent candidate for applications requiring prolonged exposure to intense heat, such as furnace linings and industrial kilns.Furthermore, the advanced design of the zircon brick ensures optimal insulation, reducing heat transfer and promoting significant energy savings. By minimizing heat loss, Zircon Brick helps improve the overall efficiency of industrial operations, leading to reduced costs and a reduced carbon footprint.Another notable attribute of the enhanced zircon brick is its exceptional resistance to chemical corrosion. The brick's dense composition and carefully selected raw materials make it highly impervious to the corrosive effects of various chemicals present in industrial environments. This feature guarantees extended service life and reduces maintenance costs, offering a cost-effective solution for industries dealing with aggressive substances such as acids and alkalis."We are incredibly proud to introduce our enhanced zircon brick to the market," said the company spokesperson. "Our team of skilled engineers and technicians have put in countless hours of research and development to ensure that this product pushes the boundaries of what can be achieved with traditional brick materials. We firmly believe that the new and improved zircon brick will revolutionize the construction industry by providing unmatched durability, thermal resistance, and cost-effectiveness."As an environmentally conscious company, Zircon Brick has also taken steps to ensure their production processes align with sustainable practices. The manufacturing of the enhanced zircon brick adheres to strict environmental regulations, limiting waste generation and using energy-efficient technologies. By implementing these measures, the company remains committed to minimizing its impact on the environment.The introduction of Zircon Brick's enhanced zircon brick signifies a milestone achievement for the construction industry. With its superior resistance to high temperatures, exceptional chemical corrosion resistance, and excellent thermal insulation properties, the enhanced zircon brick raises the bar for construction materials. By choosing this groundbreaking product, industries can significantly enhance their operational efficiency, reduce maintenance costs, and contribute to a greener future.
High-Quality Refractory Cement for Fire Bricks: Essential for Heat-Resistant Construction
Fire Brick Refractory Cement (need remove brand name) – A Game Changer in the Construction IndustryFire Brick Refractory Cement (need remove brand name) is a time-tested and eco-friendly product that has proven its effectiveness in construction and manufacturing industries. It is a type of cement used to bind fire bricks, which are heat-resistant bricks that can withstand extremely high temperatures. Fire bricks are commonly used to line fireplaces, chimneys, pizza ovens, and industrial furnaces.Refractory cement is an essential component of the construction industry, and the demand for this product has increased significantly in recent years. With the growth of the industrial sector and increasing demand for energy, the need for heat-resistant materials has become more critical than ever before. Refractory cement is designed to withstand temperatures of up to 1600°C, making it an ideal material for applications that require high-temperature resistance.Fire Brick Refractory Cement (need remove brand name) is engineered to ensure durability, strength, and thermal stability. It is made from high-quality raw materials and is designed to provide excellent resistance to thermal shock and abrasion. The cement can be used for a variety of applications, including:● Furnaces and kilns● Lining boiler fireboxes● Incinerators● Steel and iron production● Cooking ovensThe cement has also been used in the repair and maintenance of broken and cracked refractory bricks. Its superior bonding properties make it an excellent choice for repairing and reconstructing high-temperature linings. The cement has excellent adhesion properties that help in binding the fire bricks together, forming strong and durable structures.Aside from its heat-resistant properties, Fire Brick Refractory Cement (need remove brand name) is also environmentally friendly. It is made from natural materials that are free from harmful chemicals and contains no asbestos or silica. When used in construction, it emits no volatile organic compounds (VOCs), making it a safe and eco-friendly choice.The company that produces Fire Brick Refractory Cement (need remove brand name) is one of the leading manufacturers of refractory materials in the world. It has been in operation for over 50 years and has built a reputation as a quality supplier of heat-resistant products. The company prides itself on using the latest technology and adhering to the strictest quality control measures to ensure that their products are of the highest quality.Their team of experts continuously works on developing innovative products that meet the growing demands of the construction and manufacturing industries. Fire Brick Refractory Cement (need remove brand name) is just one of the many products that this company has developed to cater to the needs of their clients.The company's commitment to excellence is further reinforced by its focus on customer satisfaction. They actively solicit customer feedback to improve their products and services, ensuring that their clients receive the best possible experience. Their customer service team is knowledgeable and responsive, providing timely and efficient solutions to customer queries and concerns.In conclusion, Fire Brick Refractory Cement (need remove brand name) is a game-changer in the construction industry. Its ability to withstand high temperatures, durability, and eco-friendliness make it an attractive choice for anyone looking to build or repair a structure that requires heat-resistant materials. The company that produces it is committed to providing high-quality products and services to its clients, making it a reliable supplier of refractory materials. With Fire Brick Refractory Cement (need remove brand name), clients can rest assured that they are getting a product that is not only effective but also sustainable.
Efficient Melting Furnace Technology: Discover the Latest Advancements
Hardin Melting Furnace Revolutionizes Metal Casting with Advanced TechnologyIn the competitive world of metal casting, innovation and efficiency are key factors that determine the success of businesses in the industry. One company that has continuously pushed the boundaries of metal casting technology is a leading manufacturer of high-quality melting furnaces. Their newest creation, simply referred to as the state-of-the-art melting furnace, is set to revolutionize the casting process.The Hardin Melting Furnace, developed by a renowned technology company, represents the pinnacle of progress in the field of metal casting. With its advanced features and cutting-edge technology, it promises to improve productivity and yield, as well as reduce costs and environmental impact.One of the key features of the Hardin Melting Furnace is its unparalleled heating capabilities. Utilizing state-of-the-art heating elements, this furnace can reach extreme temperatures quickly and efficiently. This allows for faster melting and casting of metals, saving precious time and energy resources. The furnace's temperature can be easily adjusted and controlled, ensuring that each metal batch is melted at an optimal temperature for maximized quality.Moreover, the furnace is equipped with a high-quality insulation system that minimizes heat loss and maintains a stable temperature throughout the casting process. This not only aids in more efficient melting but also reduces the energy required for the overall operation.The Hardin Melting Furnace also boasts advanced safety measures. Its sophisticated control system includes alarms and sensors that detect any abnormalities in temperature or pressure. This ensures a safe working environment for operators and prevents potential accidents or damage to the furnace. In addition, the furnace's robust design and durable construction guarantee its longevity and ability to withstand the demanding conditions of the metal casting industry.The ease of use and automation of the Hardin Melting Furnace is another feature that sets it apart from its competitors. Thanks to its user-friendly interface and intuitive controls, even operators with minimal experience can operate the furnace efficiently. The furnace also allows for programmable heating cycles, further streamlining the casting process and reducing the margin for error.Furthermore, the Hardin Melting Furnace is engineered with sustainability in mind. By utilizing energy-efficient heating elements and insulation materials, it significantly reduces energy consumption and carbon emissions compared to traditional melting furnaces. As the industry faces increasing pressure to adopt eco-friendly practices, this furnace offers a viable solution for companies looking to reduce their environmental impact.The company behind the Hardin Melting Furnace has been a pioneer in the field of metal casting technology for over three decades. With a strong focus on research and development, they have consistently pushed the boundaries of what is possible in the industry. Their commitment to continuous improvement is reflected in the performance and reliability of their products.In conclusion, the Hardin Melting Furnace represents a significant breakthrough in the world of metal casting. Its advanced technology and innovative features will undoubtedly revolutionize the industry, improving productivity, efficiency, and sustainability. As companies strive to stay competitive and meet the growing demands of the market, investing in state-of-the-art melting furnaces like the Hardin Melting Furnace is a wise choice.
Discover the Promising Features of Cutting-Edge Cement Castable for Enhanced Construction Efficiency
Cement Castable: A Revolutionary Product for Modern Day IndustrialistsIn a world where innovation and productivity are essential to business success, modern-day industrialists are constantly looking for newer, more efficient ways to manufacture products. One such innovation that has proven immensely popular in recent times is Cement Castable. This revolutionary product has been designed to help industries achieve greater efficiency, speed, and accuracy in the manufacturing process.Cement Castable refers to a type of cement that can be poured like a liquid and then hardens into a solid form when it dries. The process of mixing cement and water and then letting it harden has been used in construction for centuries. However, in recent years, the technology has been developed to the extent that this method can be used for industrial purposes. One company that has taken the lead in the production of Cement Castable is {removed due to branding policy}.{company} is a leading supplier of Cement Castable and has made a name for itself in the market for producing top-quality products that meet the unique needs of its clients. The company has invested heavily in research and development to come up with new and innovative products that help its clients maximize their productivity. Cement Castable is one such product that has emerged from the company’s research and development efforts.The key benefit of Cement Castable is that it offers a superior alternative to traditional methods of manufacturing. The product allows for faster and more efficient production processes, which saves manufacturers both time and money. Additionally, Cement Castable can be molded into any shape or size, making it a highly versatile product. This is particularly useful for industries that require precision parts for their products.Another significant advantage of Cement Castable is its excellent durability and resistance to wear and tear. This means that machines and equipment made with this product tend to have a longer lifespan and require less maintenance. Furthermore, the product’s resistance to high temperatures and corrosive substances makes it ideal for industries that operate under extreme conditions.{company} takes pride in the high quality of its Cement Castable products. The company uses only the best raw materials, and its manufacturing processes are rigorously monitored to ensure that every product meets the highest standards of quality. Moreover, the company’s team of technicians and engineers are always on hand to offer technical support and guidance to clients, making the company a one-stop-shop for industrialists.In conclusion, Cement Castable is a game-changer for modern-day industrialists. The product offers a more efficient, versatile, and durable alternative to traditional manufacturing methods. At {company}, we take pride in our contribution to this innovation. Our Cement Castable products have proven to be reliable and of high quality, making us a trusted partner for industries around the world.