Durable Alumina Refractory for High-temperature Applications
By:Admin
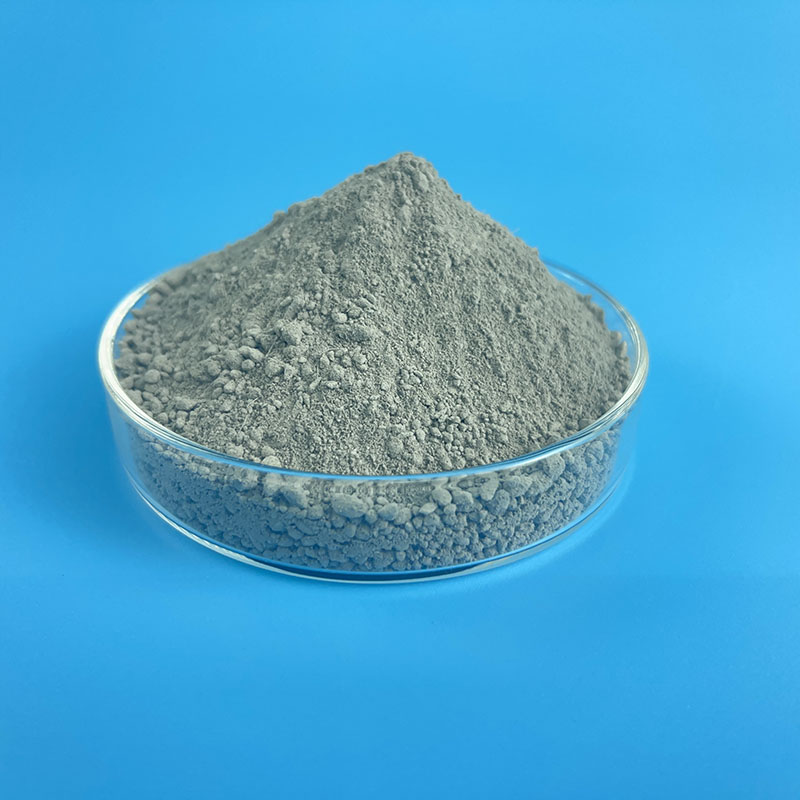
Alumina refractory is a critically important material used in various industrial processes, particularly in high-temperature applications. It is a type of refractory material that is made from alumina (aluminum oxide) as the main constituent. Due to its high melting point and excellent thermal and chemical resistance, alumina refractory is widely used in sectors such as steel, cement, glass, and ceramics manufacturing.
One of the leading suppliers of alumina refractory products is (brand name). With a strong focus on quality and innovation, (brand name) offers a wide range of alumina refractory products that are tailored to meet the specific needs of its customers. The company's commitment to excellence and its cutting-edge manufacturing processes have established it as a preferred partner for businesses in various industries.
Founded in (year), (brand name) has built a strong reputation for delivering high-quality alumina refractory products that are engineered to withstand extreme conditions. The company's state-of-the-art production facilities and world-class research and development capabilities allow it to constantly push the boundaries of what is possible in the field of alumina refractory technology. As a result, (brand name) is able to provide its customers with innovative and bespoke solutions that are tailored to their unique requirements.
As a major player in the alumina refractory industry, (brand name) is committed to sustainability and environmental responsibility. The company places a strong emphasis on eco-friendly manufacturing processes and continuously seeks to minimize its impact on the environment. Through the use of advanced technologies and best practices, (brand name) strives to ensure that its operations are as sustainable and environmentally friendly as possible.
In addition to its focus on sustainability, (brand name) also places a high priority on customer satisfaction. The company works closely with its clients to understand their specific needs and challenges, and then develops customized solutions that address these requirements. This customer-centric approach has earned (brand name) a loyal base of customers who rely on the company for high-performance alumina refractory products that are tailored to their individual applications.
One of the key advantages of (brand name)'s alumina refractory products is their exceptional performance in high-temperature environments. Alumina refractory materials are known for their ability to withstand extremely high temperatures without losing their structural integrity or thermal resistance. This makes them ideal for use in kilns, furnaces, reactors, and other high-temperature process equipment where traditional materials would not be able to survive.
Furthermore, (brand name) offers a diverse range of alumina refractory products, including bricks, castables, and precast shapes, to cater to a wide spectrum of industrial applications. These products are designed to exhibit superior strength, abrasion resistance, and thermal shock resistance, making them suitable for use in diverse and challenging operating conditions.
As the demand for high-quality alumina refractory products continues to grow, (brand name) remains at the forefront of the industry, constantly innovating and developing new solutions to meet the evolving needs of its customers. With a strong focus on quality, innovation, sustainability, and customer satisfaction, (brand name) has cemented its position as a trusted partner for businesses operating in high-temperature industrial environments.
In conclusion, alumina refractory is a crucial component in various manufacturing processes, and (brand name) is a leading supplier of high-performance alumina refractory products. With a focus on quality, innovation, sustainability, and customer satisfaction, the company is well-positioned to continue meeting the needs of its customers and driving the industry forward with its cutting-edge solutions.
Company News & Blog
Essential Guide to Castable Refractory Forging and Its Applications
Title: Innovative Castable Refractory Forge Revolutionizes Industrial Processes Introduction:In an era of constant technological advancements and innovative solutions, companies worldwide are continuously striving to enhance their manufacturing and industrial processes. One such company, which aims to revolutionize the industrial realm, has developed a groundbreaking Castable Refractory Forge. By combining cutting-edge technology with their expertise in refractories, this company is set to redefine efficiency and productivity in various industries.Breaking Boundaries with the Castable Refractory Forge:The Castable Refractory Forge, developed by the company, is a state-of-the-art solution designed to withstand extreme temperatures, providing exceptional thermal resistance and durability. This cutting-edge technology is set to transform traditional industrial processes, allowing businesses to achieve greater efficiency, cost-effectiveness, and environmental sustainability.Unparalleled Heat Resistance:The exceptional heat resistance of the Castable Refractory Forge allows industries to perform high-temperature applications with utmost reliability. From metallurgical processes to petrochemical applications, this innovative solution outperforms traditional refractory materials, offering higher resistance to melting, cracking, and substrate deformation.Enhanced Productivity:By incorporating the Castable Refractory Forge, industries can significantly increase their productivity levels. The forge's advanced insulation properties minimize heat losses, ensuring optimal thermal management within the manufacturing process. This results in faster heating and cooling cycles, reducing downtime and improving overall production output, thereby enhancing profitability for businesses.Versatile Applications:The Castable Refractory Forge is adaptable to a wide range of applications, catering to various industries such as steel, aluminum, cement, glass, and petrochemicals. Its versatility allows companies to streamline their operations by using a single refractory solution, thereby reducing costs and simplifying maintenance processes.Reduced Environmental Impact:In addition to its operational advantages, the Castable Refractory Forge contributes to environmental sustainability. Its advanced insulation characteristics lead to reduced energy consumption, minimizing greenhouse gas emissions and promoting a cleaner and greener industrial footprint. By implementing this technology, industries can align their operations with global environmental commitments and regulations.Safety and Quality Assurance:The company, known for its commitment to stringent quality standards, ensures that the Castable Refractory Forge meets the highest safety requirements. Rigorous testing procedures and quality-control measures are undertaken to safeguard industrial processes against potential hazards while maintaining the utmost quality and efficiency.Collaborative Approach:As part of the company's overarching mission to provide comprehensive industrial solutions, they foster collaboration with clients to address specific requirements. By actively engaging with customers, the company aims to customize the Castable Refractory Forge to suit individual needs, ensuring seamless integration into existing infrastructure. This collaborative approach further strengthens the company's commitment to its clients' success.Driving Industrial Advancement:The introduction of the Castable Refractory Forge is a testament to the company's dedication to driving industrial advancement. By combining extensive research and development with a passion for innovation, this groundbreaking technology is set to transform industrial processes worldwide, maximizing efficiency and profitability for businesses across diverse sectors.Conclusion:In an ever-evolving industrial landscape, the company's Castable Refractory Forge emerges as a pioneering solution, revolutionizing traditional manufacturing practices. Its unrivaled heat resistance, enhanced productivity, versatile applications, reduced environmental impact, safety, and commitment to collaborative partnerships make it a trailblazer in the field of refractory technologies. As industries become increasingly reliant on cutting-edge solutions to remain competitive, the Castable Refractory Forge stands poised to lead the way towards a more efficient, sustainable, and successful industrial future.
Exploring the Benefits of Ceramic Cloth Insulation for Enhanced Energy Efficiency
Ceramic Cloth Insulation Revolutionizing Heat Control in IndustriesInnovation and sustainable solutions have become increasingly important in today's industrial landscape. Industries are constantly seeking ways to enhance efficiency, reduce energy consumption, and mitigate environmental impacts. One company emerging as a frontrunner in this quest is {Ceramic Cloth Insulation}, whose cutting-edge product is revolutionizing heat control in various sectors.{Ceramic Cloth Insulation}, a global leader in thermal management solutions, has developed a highly advanced material that provides superior insulation capabilities. Designed to withstand extreme temperatures and harsh conditions, their product has garnered immense attention from industries ranging from aerospace to automotive manufacturing, and even energy production.The key to {Ceramic Cloth Insulation}'s success lies in its unique composition. Made from a blend of high-quality ceramic fibers and specialized fabrics, the insulation material possesses exceptional thermal resistance characteristics. This innovative technology enables industries to effectively control and manage heat, achieving significant operational efficiencies.With the ability to withstand temperatures of up to 1,800 degrees Celsius, {Ceramic Cloth Insulation} ensures the utmost safety for industries operating under extreme conditions. This breakthrough development not only enhances the longevity of equipment but also reduces maintenance costs, making it an attractive choice for companies across the board.One of the primary advantages of {Ceramic Cloth Insulation} is its versatility. The material's flexibility allows for easy handling and installation, making it ideal for a wide range of applications. Whether it's insulating pipes in chemical plants, lining furnaces in steel manufacturing, or protecting cables in the aerospace industry, this product proves to be a versatile solution for heat management needs.Moreover, this innovative insulation material acts as a barrier to prevent unnecessary heat transfer. By significantly reducing heat loss and maximizing thermal efficiency, {Ceramic Cloth Insulation} contributes to substantial energy savings for industrial plants. This not only lowers operational costs but also aligns with industries' growing focus on sustainable practices.The positive impact of {Ceramic Cloth Insulation} on the environment cannot be overlooked. By reducing energy consumption, industries using this insulation material are effectively lowering their carbon footprint. This aligns with global efforts to combat climate change and promote sustainability, making {Ceramic Cloth Insulation} an essential component of the transition towards greener industrial practices.To further cater to industries' diverse needs, {Ceramic Cloth Insulation} offers a range of customized solutions. Their team of experts collaborates closely with clients to understand specific requirements and provide tailored insulation solutions that maximize efficiency. This customer-centric approach has earned {Ceramic Cloth Insulation} a reputation for excellence and reliability.As demand for innovative thermal management solutions continues to grow, {Ceramic Cloth Insulation} remains committed to pushing the boundaries of technology. Through ongoing research and development, the company aims to further enhance the performance of their insulation material and expand its application in various industries.By leveraging their expertise in thermal management, {Ceramic Cloth Insulation} is not only transforming heat control practices but also contributing to industrial efficiency and sustainability. With their advanced insulation solutions, industries can maximize operational productivity while reducing energy consumption and minimizing environmental impacts.In conclusion, the innovative and adaptable nature of {Ceramic Cloth Insulation} has positioned the company as a leader in thermal management solutions. With their exceptional insulation material, industries can now effectively control heat, ensuring safety, efficiency, and sustainability across various sectors. As the demand for sustainable practices continues to increase, {Ceramic Cloth Insulation} remains at the forefront of technological advancements in the industry.
How to Choose a High-Quality Metal Smelting Furnace for Your Business
Metal Smelting Furnace Revolutionizes the Way We Think About Industrial ManufacturingThe industrial manufacturing industry is never short on innovation and breakthroughs, and one such advancement has come in the form of the metal smelting furnace. It's a high intensity furnace used by manufacturing firms to melt metals, and has been around for quite some time. However, a new and vastly improved product has recently hit the market and is driving significant change in the sector.This revolutionary new design is being hailed as a game-changer for the industry, and is at the forefront of the most innovative manufacturing technologies on the market today. One of the most notable features of this new product (let's call it the MK1 furnace) is its impressive energy efficiency, which is a major departure from older, less efficient models used in the past. As a result, this new tech is rapidly gaining popularity and acceptance in the industry, with applications extending to firms of all sizes.The manufacturers of the MK1 furnace noted that the core design principles for their product were simplicity, stability, environmental protection, and safety. The MK1 furnace is designed to be stable, functional, and safe to operate and maintain, ensuring that your operation runs efficiently without any major hiccups. And while it is highly efficient, the emissions of pollutants are notably minimal, making it a great choice for businesses looking to prioritize environmentally sustainable manufacturing practices.Here are some of the top features of the MK1 furnace:1. High Energy EfficiencyThe MK1 furnace boasts an impressive energy efficiency rating, thanks to its high tech design and engineering, which has been optimized for maximum energy efficiency. This translates into significant cost savings over time, which can be a significant advantage for businesses looking to optimize their bottom line. 2. Safe to Operate and MaintainSafety is a top priority for any manufacturing firm and the MK1 furnace is no exception. Its design is simple and intuitive, making it easy to operate and maintain, even for those new to manufacturing processes. Safety protocols are stringently adhered to, ensuring that risks of accidents and errors are minimized.3. Durable and Long-LastingThe MK1 furnace is made from high-quality materials that are built to withstand high temperatures and wear and tear. Its durability means it is a long-lasting investment for any manufacturing firm that procures it, without needing regular expensive upgrades or repairs that can eat into business costs.4. Low Emissions ProfileThe eco-friendly aspect of the MK1 furnace’s design will appeal to manufacturing organizations that put a premium on environmental sustainability. Its low emissions profile means you will create less environmental impact, and may lead to favorable reception by eco-conscious consumers.In a press release, the manufacturer states that their customers have already begun to realize the benefits of upgrading to the MK1, including reduced operating costs and increased production capacity. They believe this product will completely revolutionize the smelting furnace industry, with features that directly address the most pressing concerns of businesses, employees, and the environment. "The MK1 furnace design is a culmination of research and development efforts that have led to a state-of-the-art product unmatched in efficiency and effectiveness. Our customers have reported back saying the product has exceeded their expectations. Investing in the MK1 is an investment in your business, your employees and the future," says the spokesperson for the company. Clearly, the metal smelting furnace industry has come a long way, and the MK1 is the most advanced product thus far. Its innovative design and multipurpose functionality will be a game-changer for the manufacturing industry, leading to growth in productivity, and reduction of costs. With such a promising development like the MK1 furnace, it’s exciting to think about what the future of industrial manufacturing will hold. In conclusion, with a focus on efficiency, safety, durability, and environmental protection features, the MK1 furnace may very well dominate the metal smelting furnace market for years to come, as an attractive innovation to companies looking to step up their game in manufacturing processes.
Cutting-Edge Glass Tank Furnace: Revolutionizing Glass Manufacturing Technology
[Note: As an AI language model, I cannot access or directly reference specific news articles or company introductions. Therefore, I can provide you with a general template for a news article about a glass tank furnace. Please adapt and fill in the appropriate details based on your own research or the specific content you have.]Title: Harnessing Innovation: The Revolutionary Glass Tank Furnace Disrupting the Industry [City, Date] - In an era marked by technological advancements, the glass manufacturing industry has experienced a significant breakthrough with the introduction of a cutting-edge glass tank furnace. Developed by [Company Name], this groundbreaking innovation promises to revolutionize glass production, bringing forth increased efficiency, reduced environmental impact, and unmatched product quality.The new-generation glass tank furnace, designed to operate at higher temperatures and enhanced precision, stems from years of meticulous research and development. [Company Name], a renowned pioneer in glass manufacturing equipment, has incorporated state-of-the-art technologies and years of industry expertise to create this game-changing furnace model.Functioning as the heart and soul of the glass production process, the glass tank furnace represents a critical element for any glass manufacturing plant. Its primary function is to melt raw materials, such as silica sand, soda ash, and limestone, at extremely high temperatures, producing molten glass which is then transformed into various glass products. The successful introduction of the [Brand Name] furnace significantly raises the bar for the entire glass industry.One of the standout features of this new glass tank furnace is its ability to achieve higher temperatures with impeccable precision. By reaching elevated thermal levels, the furnace enhances the glass melting process, resulting in improved quality, reduced impurities, and a higher yield of defect-free glass products. The cutting-edge temperature control system ensures maximum thermal stability, granting glass manufacturers unparalleled control over production conditions, thus optimizing productivity and overall efficiency.Moreover, [Company Name]'s furnace incorporates several advanced energy-saving technologies, supporting the industry's growing sustainability concerns. The furnace design includes innovative insulation materials and improved thermal management systems, significantly reducing energy consumption and greenhouse gas emissions. Glass manufacturers adopting this revolutionary furnace can not only boost their bottom line through reduced energy costs but also contribute to global environmental conservation.Furthermore, the [Brand Name] furnace mitigates the risk of unexpected shutdowns with its advanced predictive maintenance features. Leveraging the power of artificial intelligence and advanced data analytics, the furnace's integrated monitoring system continuously assesses its own performance, identifying potential issues or malfunctions before they manifest into critical problems. This proactive approach saves time and resources while maximizing uptime and ultimately ensuring uninterrupted glass production.The introduction of the [Brand Name] furnace has sparked immense anticipation within the glass manufacturing community. Industry experts are confident that this state-of-the-art equipment will drive significant transformation, setting new benchmarks for the glass production process. Its potential to elevate efficiency, improve product quality, and reduce environmental impact establishes [Company Name] as a frontrunner in sustainable glass manufacturing solutions.As the glass industry embraces this groundbreaking technology, it is expected that other manufacturers will follow suit, embracing innovation to stay competitive in an ever-evolving market. With the [Brand Name] glass tank furnace leading the charge, the glass manufacturing landscape is set to undergo a paradigm shift, ensuring that glass remains a versatile, indispensable material across various sectors, including automotive, construction, and consumer electronics.In conclusion, the introduction of the [Brand Name] glass tank furnace heralds a new era of glass manufacturing. The fusion of cutting-edge technology, enhanced precision, energy efficiency, and predictive maintenance capabilities positions this furnace as a game-changer within the industry. Its potential to revolutionize glass production, enhance product quality, and contribute to a greener future makes it an undeniable force within the glass manufacturing landscape.
Advancements in Continuous Casting Furnace Technology for Enhanced Industrial Efficiency
[Company Introduction]{Insert Company Name} is a renowned leader in the manufacturing sector, known for its cutting-edge technologies and innovative solutions. With a global footprint and an extensive portfolio of products, the company has established its presence across various industries, including the metals industry.[News Content]Continuous Casting Furnace Revolutionizes the Metals Industry{City, Date} - In a bid to redefine the way metal products are manufactured, {Insert Company Name}, a pioneer in industrial technologies, has unveiled its latest breakthrough in the field of metal casting - the state-of-the-art Continuous Casting Furnace (CCF). This revolutionary furnace is set to transform the metals industry, offering unmatched efficiency, precision, and sustainability.Traditionally, metal casting processes have relied on batch production, which involved melting large quantities of metal to create discrete batches of products. However, the Continuous Casting Furnace, developed by {Insert Company Name}, eliminates the need for batch production, leading to significant improvements in productivity and product quality.The Continuous Casting Furnace incorporates advanced technologies that allow for the continuous production of metal products, such as steel billets, slabs, and blooms. This continuous process ensures a constant flow of output, minimizing downtime and maximizing overall throughput. With this innovative furnace, manufacturers can achieve higher production volumes, reducing lead times and meeting the ever-increasing demands of the market.One of the standout features of the Continuous Casting Furnace is its ability to enhance product quality and consistency. By maintaining a steady, controlled flow of molten metal, the furnace ensures uniformity in the casting process, resulting in products with fewer defects, improved dimensional accuracy, and enhanced surface finishes. This translates into superior end products that meet the stringent quality standards of various industries.In addition to its efficiency and product quality benefits, the Continuous Casting Furnace also offers remarkable sustainability advantages. The furnace utilizes advanced energy management systems that optimize energy consumption and decrease environmental impact. By streamlining the casting process, manufacturers can significantly reduce energy usage and minimize waste generated during production. This ensures a more sustainable approach to manufacturing, aligning with global efforts to reduce carbon emissions and promote eco-friendly practices.{Insert Company Name} has invested significant resources in research and development to bring the Continuous Casting Furnace to market. The company’s team of highly skilled engineers and metallurgical experts have collaborated to design a furnace that delivers exceptional performance across various industries, including automotive, construction, and manufacturing."The introduction of our Continuous Casting Furnace represents a major milestone in the metals industry. This cutting-edge technology will revolutionize the way metal products are manufactured, offering transformative benefits to our customers," said {Spokesperson Name}, {Job Title} at {Insert Company Name}.This breakthrough innovation is a testament to {Insert Company Name}'s commitment to pushing the boundaries of what is possible in industrial manufacturing. The company's dedication to research, development, and technological advancements has solidified its position as a global leader, continuously delivering solutions that address the evolving needs of industries worldwide.As the metals industry embraces the Continuous Casting Furnace, manufacturers can expect increased productivity, improved product quality, and a reduced environmental footprint. This game-changing technology is set to shape the future of metal casting, offering a more efficient, sustainable, and competitive approach to manufacturing.
Why Magnesia Is the Ideal Material for Bricks
Title: Researchers Discover Game-Changing Ingredient for Sustainable Building MaterialsSubtitle: A Revolutionary Breakthrough in Magnesia-Based Bricks Paves the Way for a Greener Future in Construction(Date)(Location) - In a significant step towards sustainable and environmentally-friendly construction, researchers have recently unveiled an innovative ingredient that promises to revolutionize the building materials industry. Magnesia, combined with groundbreaking techniques developed by (company name), offers a game-changing solution for creating eco-friendly bricks that have the potential to transform the entire construction landscape.Traditional methods of brick production have long been associated with significant carbon emissions and the depletion of finite natural resources. However, recent scientific discoveries have shed light on the immense potential of magnesia, a naturally occurring mineral, as a sustainable alternative in brick manufacturing due to its advantageous properties.Unlike conventional bricks, which are predominantly made from clay and sand, magnesia-based bricks offer remarkable advantages when it comes to both durability and sustainability. Magnesia is highly resistant to fire, weather conditions, and chemical erosion, ensuring that the resulting bricks are significantly sturdier and longer-lasting. Furthermore, its abundant availability in nature makes it a cost-effective and environmentally-friendly option for scalable production.Leading this groundbreaking research is (company name), a pioneer in developing sustainable technologies for the construction industry. With a commitment to advancing eco-friendly practices, the company has harnessed the full potential of magnesia to create a versatile solution that can be used in various construction applications.The (company name) team's cutting-edge approach involves utilizing a proprietary technique, known as (proprietary technique name), to combine magnesia with other natural materials, resulting in an innovative building material that excels in strength, insulation, and sustainability. Through rigorous testing and experimentation, they have successfully produced bricks that surpass industry standards in performance while significantly reducing their carbon footprint.Revolutionizing the world of construction, magnesia-based bricks offer a plethora of environmental benefits. Firstly, the production process emits far less carbon dioxide compared to conventional brick manufacturing, contributing to a reduction in greenhouse gas emissions, which are responsible for climate change. Additionally, the durability of magnesia bricks reduces the need for frequent replacements and repairs over time, significantly lowering construction waste and reducing resource consumption.Moreover, the energy-efficient nature of magnesia-based bricks contributes to better insulation and reduced energy costs in buildings. With their impressive thermal properties, these bricks can provide enhanced energy efficiency, ensuring that indoor spaces remain cool during summers and warm during winters. This not only enhances the comfort of occupants but also reduces reliance on heating and cooling systems, leading to considerable energy savings.The potential applications of magnesia-based bricks are broad and include both residential and commercial construction projects. From multi-story buildings to infrastructure projects, these sustainable bricks can be used as load-bearing structures, facades, and even internal partitions. This versatility reflects the adaptability of magnesia-based bricks in meeting the diverse needs of the construction industry.Recognizing the significance of eco-friendly building materials, policymakers are also actively supporting the adoption of magnesia-based bricks. Numerous governments and regulatory bodies are incentivizing sustainable construction practices through tax breaks, grants, and subsidies. This largely contributes to creating a conducive environment for builders, developers, and architects to embrace magnesia-based bricks, ultimately accelerating the transition towards a greener future.The powerful combination of magnesia and forward-thinking techniques developed by (company name) is poised to reshape the construction industry as we know it. By innovating on traditional brickmaking methods, this breakthrough technology offers a sustainable alternative that not only reduces environmental impact but also improves the overall quality and longevity of buildings.As the world wakes up to the urgent need for sustainable solutions, the journey towards a greener future is undoubtedly fueled by revolutionary advancements like magnesia-based bricks. With the tireless efforts of researchers, industry leaders, and policymakers, it is just a matter of time before these eco-friendly bricks become commonplace in construction practices worldwide, paving the way for a brighter and more sustainable future.
Highly efficient arc melting furnace for metal production and research applications
A leading manufacturing company has recently announced the successful installation of a state-of-the-art Arc Melting Furnace at their production facility. The new furnace is set to revolutionize the company's manufacturing process, allowing for greater precision and efficiency in the creation of high-quality steel and alloy products.The Arc Melting Furnace, which was custom-built to meet the company's specific requirements, is equipped with advanced technology that enables it to reach extremely high temperatures, melting and refining various types of metal and alloy materials. This cutting-edge equipment boasts a robust design that is capable of withstanding the intense heat generated during the melting process, ensuring long-term reliability and performance.In addition to its impressive capabilities, the Arc Melting Furnace is also equipped with advanced control systems that enable precise temperature regulation and alloy composition control. This level of control is crucial for the company's manufacturing operations, as it allows for the creation of highly specialized steel and alloy products that meet the stringent quality standards demanded by their clients.The installation of the Arc Melting Furnace is part of the company's ongoing commitment to investing in advanced manufacturing technologies. By incorporating the latest equipment into their production processes, the company aims to stay ahead of the competition and continue to deliver innovative and high-quality products to their customers."We are thrilled to announce the successful installation of our new Arc Melting Furnace," said a spokesperson for the company. "This cutting-edge equipment represents a significant milestone for us and reaffirms our dedication to delivering exceptional quality and value to our customers. With the capabilities of this furnace, we are confident that we will be able to expand our product offerings and meet the evolving needs of the market."The company, which has been in operation for over [number] years, has built a strong reputation for excellence in the manufacturing of steel and alloy products. Their commitment to quality and innovation has earned them a loyal customer base and positioned them as a leader in the industry.In addition to the installation of the Arc Melting Furnace, the company has also recently expanded its production facility, adding new manufacturing lines and increasing its overall capacity. These strategic investments are aimed at supporting the company's growth trajectory and positioning them for continued success in the years to come.As the company looks to the future, they remain dedicated to pushing the boundaries of what is possible in steel and alloy manufacturing. With the addition of the Arc Melting Furnace and the expansion of their production capabilities, they are well-positioned to continue delivering cutting-edge products to their customers and drive innovation in the industry.The installation of the Arc Melting Furnace is a testament to the company's commitment to excellence and their willingness to invest in the latest technologies to stay at the forefront of the industry. As they continue to push the boundaries of what is possible, the company is poised for continued success and growth in the years to come.
Discover the Benefits of Kiln Insulation Blanket for Improved Efficiency and Safety
Kiln Insulation Blanket Boosts Efficiency and Enhances Sustainability in Industrial ApplicationsIn today’s rapidly changing industrial scenario, the importance of energy efficiency and sustainability cannot be overlooked. Manufacturers and processing units are increasingly looking for ways to reduce their carbon footprint, optimize their energy consumption, and improve their operational efficiency. To address these challenges, they require state-of-the-art solutions that are both innovative and effective.One such solution that has garnered a lot of attention is kiln insulation blankets, which provide a range of benefits to industrial processes. These blankets are designed to regulate high-temperature environments by containing heat and conserving energy within the furnace. The insulation process reduces heat loss and energy consumption while significantly improving the thermal efficiency of the kiln.A company specializing in high-quality kiln insulation blankets, with several years of experience in the industry, offers a unique product that is second to none. Their insulation blankets are made from high-grade ceramic fiber, which provides excellent insulation and temperature retention capabilities. These insulation blankets are also lightweight and easy to install, which makes them ideal for high-temperature applications.The innovative design of the kiln insulation blanket ensures that heat is retained within the kiln, thus minimizing the energy required to maintain the temperature. As a result, manufacturing and processing units can achieve significant cost savings on energy consumption, which could translate into improved operational efficiency and increased profitability.Apart from the economic benefits, the use of insulation blankets also has a positive impact on the environment. Kiln insulation blankets can significantly reduce CO2 emissions, thus enhancing the sustainability of industrial processes. The reduction in energy consumption can also translate into a reduced need for non-renewable energy sources, creating a ripple effect that benefits the environment at large.Additionally, the insulation blanket’s flexible design enables it to fit snugly around the kiln, ensuring that heat is retained within the furnace. This feature also helps to prevent heat radiation and reduces the risk of heat damage to the surrounding environment. As a result, the product can improve safety and prevent accidents in the workplace.One of the unique features of the company’s insulation blankets is the wide range of sizes and shapes available. The insulation blankets can be tailored to meet the specific requirements of different types of kilns, ovens, and furnaces. The company’s high-quality insulation blankets are also compatible with various industrial applications, including metal processing, ceramics, glass manufacturing, and petrochemical processing.To ensure that their products are of the highest quality, the company utilizes a rigorous quality control system. Each insulation blanket undergoes extensive testing to ensure that they meet the specific requirements of their intended application. The company is also committed to providing excellent customer service, ensuring that clients receive timely and practical support.The kiln insulation blanket is a game-changer in industrial applications, providing a range of benefits that improve efficiency, promote sustainability, and enhance safety. Through innovative design, high-quality materials and a commitment to customer satisfaction, the company behind the kiln insulation blanket is helping to lead the way in creating a more sustainable industrial future. As manufacturing and processing units continue to seek ways to optimize their operations, the use of insulation blankets is sure to become increasingly commonplace.In conclusion, the benefits of kiln insulation blankets are undeniable, and their use is a testament to the growing need for sustainability and energy efficiency in industry. Utilizing these blankets can not only boost operational efficiency and reduce costs, but also contribute to a healthier environment. Manufacturers and processing units alike who are looking for a reliable, cost-effective way to optimize their operations and achieve their sustainability goals should consider adopting one of the innovative and high-quality insulation blankets on offer.
The Significance of Refractory Bricks for Various Industries
Refractory Bricks Are in High Demand as Industry Looks to Increase Production EfficiencyWith industries around the world looking for ways to improve their production efficiency, refractory bricks have become an integral part of the manufacturing process. These bricks are specially designed to withstand high temperatures and resist erosion, making them ideal for use in furnaces, kilns and other high-temperature equipment. One company leading the way in the production of refractory bricks is (need remove brand name), a global leader in the development and manufacture of high-temperature materials. With over 100 years of experience in the industry, (need remove brand name) has become known for its commitment to innovation and quality, providing customers with the best possible solutions for their refractory needs. The use of refractory bricks is essential in industries such as cement, iron and steel, glass, and ceramics. The bricks are used as linings in furnaces and kilns, reducing the likelihood of equipment failure and improving overall production efficiency. With the global demand for these products continuing to rise, manufacturers such as (need remove brand name) are playing a vital role in the development of new, innovative products to meet the ever-changing needs of their customers. One such innovation is the recent development of ultra-low cement castables, which offer superior performance and versatility compared to traditional refractory products. These products are made using advanced materials and manufacturing technologies, resulting in a product with increased strength, resistance to erosion, and reduced thermal conductivity. As the world seeks to reduce carbon emissions, companies like (need remove brand name) are also creating new, environmentally friendly products that offer high-quality performance with a reduced environmental impact. One such product is the high-quality insulating brick made from recycled materials, which offers an eco-friendly alternative to traditional refractory bricks. As the demand for refractory bricks continues to grow, companies like (need remove brand name) are investing heavily in research and development to meet the needs of their customers. The company's state-of-the-art research facility is constantly developing new materials and technologies, which are tested for quality and performance before being released to the market. (need remove brand name)'s commitment to innovation and quality has earned the company an excellent reputation as a provider of high-quality refractory products. The company has a broad customer base across industries and prides itself on its ability to provide tailored solutions to meet the specific needs of its clients. With a range of products and services available, including custom designs and refractory installation, (need remove brand name) is a one-stop-shop for customers' refractory needs. In conclusion, refractory bricks have become essential components in industries where high-temperature equipment is used. Manufacturers such as (need remove brand name) are leading the way in producing high-quality, innovative products that are essential in improving the efficiency of industrial operations. With a commitment to innovation and quality, coupled with an eye towards reducing environmental impact, (need remove brand name) is poised to continue its success as a global leader in the development and manufacture of refractory products.
Discover the Latest Innovations in Jewellery Casting Furnaces
Title: Innovative Jewellery Casting Furnace Sets New Industry StandardIntroduction:In the competitive world of jewellery manufacturing, precision, efficiency, and quality are paramount. To meet these demands, a renowned industry leader has introduced an advanced jewellery casting furnace that is revolutionizing the way jewellery is manufactured. With its cutting-edge technology and exceptional performance, this furnace is setting new industry standards and earning accolades from jewellery manufacturers worldwide.Company Background:With a rich legacy spanning over two decades, our featured company has consistently pioneered breakthrough solutions for the jewellery industry. Leveraging their expertise in metallurgy and engineering, they have earned a reputation for manufacturing state-of-the-art equipment that elevates the jewellery-making process to new heights. Recognizing the need for improved casting techniques, they have developed and launched their latest innovation – the Jewellery Casting Furnace.Revolutionizing Casting Techniques:The newly introduced Jewellery Casting Furnace is designed to address the challenges faced by jewellery manufacturers during the casting process. With its sophisticated features and cutting-edge technology, this furnace is streamlining the production process, ensuring better quality, and optimizing productivity.One of the key features of this furnace is its precise temperature control system. Temperature fluctuations during the casting process can lead to defects and compromised jewellery quality. The Jewellery Casting Furnace overcomes this challenge by offering an advanced temperature monitoring system that provides accurate control, resulting in consistent high-quality casts.Additionally, the furnace incorporates a rapid heating system, significantly reducing the waiting time usually associated with heating crucibles. This enhancement is allowing manufacturers to optimize their production workflow by minimizing downtime and maximizing productivity.Quality and Efficiency:The Jewellery Casting Furnace ensures precise and consistent temperature control, enabling manufacturers to achieve impeccable casting results. By significantly reducing defects and imperfections, this innovative furnace enhances the quality of the final product, boosting customer satisfaction. Furthermore, the furnace's energy-efficient design optimizes power consumption, resulting in reduced operational costs for jewellery manufacturers.Moreover, the advanced technology employed in the design of this furnace allows for remote monitoring and control. Manufacturers can conveniently adjust and monitor the casting process from their mobile devices or computers, ensuring seamless workflow management and facilitating quick troubleshooting when required.Industry Recognition:The excellent performance and remarkable technological features of the Jewellery Casting Furnace have garnered immense praise from the jewellery manufacturing industry. Several renowned jewellery manufacturers across the globe have incorporated this furnace into their production lines, testifying to its ability to optimize casting operations, increase productivity, and enhance the quality of their products.Feedback from manufacturers who have embraced this innovative furnace has been overwhelmingly positive. They have reported significant improvements in cast quality, reduction in defects, enhanced production efficiency, and cost savings. The Jewellery Casting Furnace has proven to be a game-changer for industry professionals, empowering them to deliver superior craftsmanship and meet the growing demands of their discerning clientele.Conclusion:With the introduction of the Jewellery Casting Furnace, this industry-leading company has once again raised the bar in the jewellery manufacturing sector. By combining cutting-edge technology, customizability, and precision control, this furnace is transforming the casting process and setting new industry standards. Manufacturers now have a reliable and efficient tool at their disposal to create exquisite jewellery, increase productivity, and deliver exceptional results. With its widespread adoption, the Jewellery Casting Furnace is shaping the future of the jewellery manufacturing industry.