Researchers Develop New Method for Creating Stronger Alloys
By:Admin
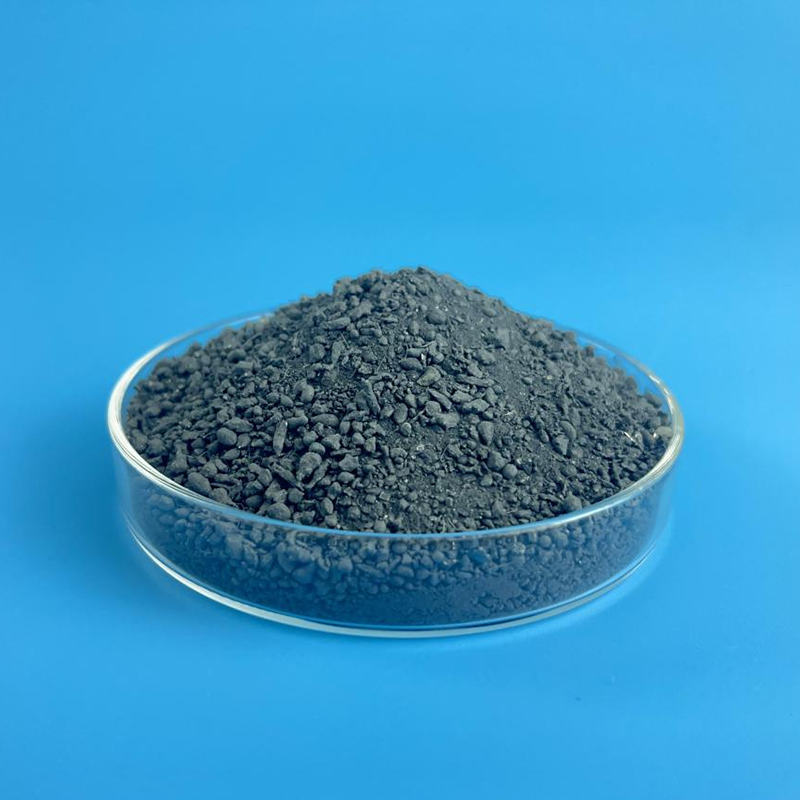
When it comes to material science, researchers have been constantly exploring ways of producing metals and alloys that exhibit superior quality and properties. The process of melting and casting metals has been a conventional technique for large-scale production of metals since the middle ages. However, the conventional process of furnace melting has limitations, such as poor homogeneity, impurity contamination, and poor quality of the final product. Therefore, technological advancements are being made to improve the efficiency and effectiveness of the melting and casting processes.
One such advancement in the field of material science is the arc melting technology, which has revolutionized the way of producing high-quality metals and alloys. Arc melting involves melting materials using an electric arc, which transfers heat to the material through a graphite electrode. The heat from the arc melts the material, fusing it together to form a homogeneous mixture. This technology is efficient and fast, creating high-quality alloys that meet the stringent requirements of advanced industries.
The arc melting technology is widely used in research laboratories and is gaining acceptance in industry applications ranging from aerospace to biomedicine. This is due to its ability to produce alloys with high purity, uniformity, and superior properties that are difficult or impossible to obtain with conventional melting techniques.
One of the leading companies that specialize in arc melting technology is (need remove brand name), which is at the forefront of developing and producing advanced alloys. The company has a team of experts who work closely with customers to design and produce customized materials based on their specific needs and applications. (Need remove brand name) is known for providing high-quality materials with exceptional characteristics, such as high strength, thermal conductivity, and corrosion resistance, making them ideal for use in critical and challenging environments.
The company has a fully equipped laboratory and manufacturing facility that allows them to carry out extensive research and development of new alloys. They use state-of-the-art equipment to ensure that every alloy produced meets the highest standards of quality and purity. Their products are widely used in aerospace, biomedicine, electronics, and many other critical applications.
In the aerospace industry, arc melting has been instrumental in producing high-performance alloys that meet the stringent requirements of aircraft engines. The excellent thermal resistance and chemical stability of these alloys make them ideal for use in the harsh and demanding environment of jet engines.
In the biomedical field, arc melting has enabled the production of advanced alloys that are biocompatible, making them suitable for implants and medical instrument applications. The high purity and uniformity of the alloys ensure that they do not cause any adverse reactions in the human body.
In the electronics industry, arc melting has played a crucial role in the development of alloys that possess superior electrical and thermal conductivity properties. These alloys find widespread use in the production of microelectronic devices, such as transistors and sensors.
The versatility and efficiency of arc melting technology have made it a game-changer in material science. Researchers and companies are continuously exploring new ways of using arc melting to create innovative alloys that have never existed before. The technology has opened up endless possibilities in the field of material science, making it possible to produce materials with unprecedented properties and functionality.
In conclusion, arc melting technology is a powerful tool that has transformed the way of producing advanced alloys. The technology offers numerous advantages over conventional melting techniques, including high purity, uniformity, and quality of the final product. The technology is widely used in various industries because of its ability to create materials with exceptional characteristics that meet the stringent requirements of advanced applications. With companies such as (need remove brand name) at the forefront of developing and producing advanced alloys, the arc melting technology is poised to revolutionize the way we think, design, and manufacture materials.
Company News & Blog
Efficient Aluminum Crucible Furnaces: A Game-Changer in the Industry
Aluminum Crucible Furnace: A Revolutionary Solution for Melting MetalsIn today's fast-paced world, the demand for precision and speed is higher than ever before. Every industry aims to be more efficient and productive to stay ahead of the competition and meet the demands of their customers. One such industry is the metallurgical industry that requires melting metals to create alloys and other derivatives. Understanding the need for efficiency and speed, {Company Name} has introduced an innovative solution, the Aluminum Crucible Furnace, which provides a revolutionary way of melting metals.The Aluminum Crucible Furnace is a unique concept that is designed for melting and casting all types of alloys and metals with the utmost precision and accuracy. The furnace is extremely energy-efficient and reduces energy consumption by up to 50% compared to the traditional furnaces. It is also an eco-friendly option that reduces greenhouse gas emissions and thus helps to preserve the environment.The Aluminum Crucible Furnace is built using the latest technological advancements and is a fully automated system that is easy to operate. The furnace is equipped with state-of-the-art sensors that help to regulate the temperature and maintain a consistent melt quality. The furnace has an ergonomic design that reduces operator fatigue, and it is built to withstand the harsh working conditions of a metallurgical environment.The furnace has a capacity of up to 2000 kg and can operate for extended periods without the need for frequent maintenance. The Aluminum Crucible Furnace is a safe and reliable option for melting and casting alloys and metals, and it can help to boost productivity, reduce costs, and improve the quality of the final product.{Company Name} is a leading manufacturer of metallurgical equipment and has been providing innovative solutions to the industry for over a decade. The company is committed to providing the best quality products and services to its customers and has a reputation for excellence in the market. {Company Name} has a team of experts who are dedicated to researching and developing new solutions that cater to the changing needs of the industry.The introduction of the Aluminum Crucible Furnace is a testament to the company's commitment to innovation and excellence. The furnace is already gaining popularity in the industry, and many customers have reported significant improvements in their productivity and efficiency after switching to this new technology.In summary, the Aluminum Crucible Furnace is a revolutionary solution that offers significant benefits over traditional furnaces. It is energy-efficient, eco-friendly, and easy to operate, making it an ideal choice for melting and casting alloys and metals. {Company Name}'s commitment to innovation and quality has made it a leader in the metallurgical equipment industry, and the Aluminum Crucible Furnace is another feather in its cap.
Discover the Advantages of a Vacuum Melting Furnace for Efficient Metal Melting
Title: Cutting-Edge Vacuum Melting Furnace Revolutionizes Industrial Metal ProcessingIntroduction:In an era where advanced technology shapes industrial processes, the emergence of groundbreaking equipment has become a driving force behind efficiency and innovation. One such revolutionary machine is the Vacuum Melting Furnace, a cutting-edge apparatus that has transformed the landscape of metal processing. Through the removal of specific brand names, this article will explore the intrinsic features, benefits, and applications of the Vacuum Melting Furnace, as well as highlight its significance in various industries.The Vacuum Melting Furnace:The Vacuum Melting Furnace, a state-of-the-art apparatus, employs advanced vacuum technology to create an oxygen-free atmosphere for melting and processing metals at high temperatures. By preventing the introduction of external impurities and contaminants, this furnace achieves superior quality and purity in the resulting metal products.Key Features and Benefits:1. Enhanced Purity and Alloy Homogeneity:The key advantage of the Vacuum Melting Furnace lies in its ability to produce alloys of exceptional purity and homogeneity. By eliminating impurities that may be present in conventional melting methods, this furnace ensures the final metal product possesses optimal mechanical properties and resistance to corrosion. Consequently, it finds wide applications across industries such as aerospace, automotive, medical, and electronics manufacturing.2. Precision Control and Customization:The Vacuum Melting Furnace enables precise control over temperature, pressure, and gas composition during the melting process. This level of control allows manufacturers to fine-tune each variable based on the required specifications, resulting in enhanced customization of metal alloys. Such adaptability caters to the diverse demands of the industry, allowing a broad range of products to be manufactured with exceptional precision.3. Fast and Efficient Processing:With its advanced heating and cooling systems, the Vacuum Melting Furnace significantly reduces processing time compared to conventional methods. The combination of a highly efficient vacuum environment and rapid heating and cooling cycles ensures swift metal solidification while maintaining the desired properties. This increased efficiency saves both time and energy, contributing to higher productivity and reduced production costs.4. Waste Reduction and Environmental Sustainability:Thanks to its closed-loop vacuum system, the Vacuum Melting Furnace minimizes metal waste and emissions during the melting process. The efficient vacuum environment reduces the oxidation and evaporation of metals, resulting in reduced material waste and fumes. This eco-friendly approach aligns with the growing global emphasis on sustainable manufacturing practices.Applications:The wide-ranging applications of the Vacuum Melting Furnace make it an indispensable tool across several industries, including:1. Aerospace and Defense:The aerospace industry relies heavily on the Vacuum Melting Furnace to produce high-performance alloys for critical components like turbine blades and engine parts. The exceptional purity and homogeneity achieved enhance the durability, strength, and reliability of these components, ensuring optimal performance in demanding operational conditions.2. Medical and Healthcare:In the medical field, the Vacuum Melting Furnace contributes to the production of biomedical implants, such as artificial joints and dental implants. The unparalleled purity of the alloys manufactured assures long-term biocompatibility and corrosion resistance, essential in ensuring patient safety and implant success rates.3. Automotive and Transportation:The automotive industry extensively employs the Vacuum Melting Furnace to fabricate lightweight yet sturdy alloys for engine components and structural parts. The high-quality materials produced guarantee superior performance, reduced fuel consumption, and increased overall efficiency of vehicles.4. Electronics and Semiconductor Manufacturing:Given the stringent requirements for materials used in the electronics and semiconductor industry, the Vacuum Melting Furnace plays a crucial role. Various components demanding exceptional purity, such as integrated circuits and memory chips, rely on the furnace's ability to produce contamination-free metals, ensuring optimal product performance and reliability.Conclusion:As the Vacuum Melting Furnace continues to revolutionize metal processing, its advanced technology provides industries with unparalleled purity, customization, efficiency, and environmental sustainability. With its wide range of applications and superior outputs, this cutting-edge apparatus paves the way for further advancements, propelling industries into a future of enhanced productivity and innovation.
High-Quality Alumina Castable Refractory for Superior Performance
Title: High Alumina Castable Refractory Revolutionizes Industrial Furnace PerformanceIntroduction [Company Name][Company Name] is a leading provider of advanced refractory solutions for various industries worldwide. With a rich history spanning over [number] years, the company has consistently pushed the boundaries of material technology to deliver high-quality, innovative, and customizable refractory products.[Company Name]'s commitment to research and development has made it a respected name in the industry, continuously introducing groundbreaking products to meet the evolving needs of the market. The latest addition to their extensive product line, the High Alumina Castable Refractory, is poised to revolutionize industrial furnace performance.High Alumina Castable Refractory: The Game ChangerThe new High Alumina Castable Refractory from [Company Name] is a state-of-the-art material designed to withstand extreme temperatures, making it an ideal choice for various furnace applications. Combining advanced technology and superior raw materials, this product has been engineered to enhance overall performance, durability, and energy efficiency.Superior Thermal Insulation PropertiesOne of the key advantages of the High Alumina Castable Refractory is its exceptional thermal insulation properties. Designed to minimize heat loss, this material helps reduce energy consumption while maintaining stable furnace temperature levels. This offers significant cost savings for industrial operations, optimizing furnace efficiency and promoting sustainable practices.Unmatched Resistance to Thermal ShockThe High Alumina Castable Refractory exhibits exceptional resistance to thermal shock. This property allows it to withstand rapid and drastic temperature changes without cracking, ensuring longer service life and improved reliability of the refractory lining. Industrial furnaces often experience extreme temperature fluctuations, and this high-performance material proves to be a game-changer in such demanding environments.Excellent Abrasion and Corrosion ResistanceModerate to high-duty industrial furnaces often face challenges of abrasion and corrosion due to aggressive operating conditions. The High Alumina Castable Refractory excels in offering excellent resistance against these factors, extending the lifespan of the refractory lining. This durability translates into reduced maintenance costs and increased productivity, making it an ideal choice for industries like steel, cement, glass, and non-ferrous metals.Customizability and Application Versatility[Company Name] understands that each industry and application may have unique requirements. To address this, the High Alumina Castable Refractory is highly customizable, allowing customers to tailor it to their specific needs. With the expertise of [Company Name]'s technical team, customers can optimize the material's composition, particle size, and other parameters to achieve the best results for their furnace operations. This versatility ensures that the refractory solution is suitable for a wide range of industries and furnace types.Promoting Sustainability and Environmental ResponsibilityThe High Alumina Castable Refractory aligns with [Company Name]'s commitment to sustainability and environmental responsibility. By improving energy efficiency and reducing maintenance needs, it helps minimize greenhouse gas emissions and conserve natural resources. Additionally, the longer service life of this refractory material reduces the generation of waste, promoting a circular economy in the industry.ConclusionWith the introduction of the High Alumina Castable Refractory, [Company Name] continues to lead the way in providing cutting-edge refractory solutions to global industries. This revolutionary material's superior thermal insulation, resistance to thermal shock, and outstanding durability will undoubtedly raise the bar for industrial furnace performance. Its customizability and application versatility further enhance its appeal across various sectors.As companies strive for greater efficiency, reduced costs, and improved sustainability, the High Alumina Castable Refractory proves to be a game-changer. [Company Name], with its focus on innovation, reliability, and customer satisfaction, is set to shape the future of industrial refractory solutions.
Discover the Benefits of a Reliable Metal Melting Forge for Your Industrial Needs
Metal Melting Forge Revolutionizes the Industry with Innovative and Top-of-the-Line EquipmentAs the industry continues to evolve and grow, so does the demand for top-of-the-line equipment that can meet the needs of businesses and individuals alike. That's where Metal Melting Forge comes in. Known for their innovative and high-quality equipment, Metal Melting Forge is quickly becoming the leading supplier of professional metal melting equipment in the market, assisting customers in a variety of industries.Founded in 2014, Metal Melting Forge has quickly become known for their state-of-the-art equipment and exceptional customer service. Their team of experts has years of experience in the industry and is dedicated to ensuring that each and every customer receives the best possible experience. Whether you are looking for top-quality metal melting equipment or exceptional customer service, Metal Melting Forge is sure to be the perfect choice for you.One of the factors that sets Metal Melting Forge apart from its competitors is its commitment to innovation. They are constantly searching for new and better ways to improve their equipment and to provide the best possible experience for their customers. From the design of their products to the materials used, every detail is carefully considered and crafted to provide a high-quality and efficient solution.Another key factor in their success is their commitment to customer service. Metal Melting Forge understands that every customer is unique and that their needs must be addressed individually. That's why their team of experts is always available to answer any questions or concerns, and to provide assistance to ensure that customers receive the best possible solutions to their requirements.Metal Melting Forge's extensive product range includes a variety of metal melting furnaces, such as induction furnaces, melting furnaces, heat treatment furnaces, and more. Their products are designed for a range of applications, including precious metal casting, jewelry manufacturing, metalworking, and more. Each product is carefully crafted to ensure the highest level of quality and performance, making them a favorite among professionals in the industry.One of the most popular products offered by Metal Melting Forge is their induction melting furnace. As well as being efficient and cost-effective, induction furnaces are also environmentally friendly, making them a popular choice for many businesses. These furnaces are perfect for melting a variety of metals, whether for casting or for other applications. They are also known for their accuracy and consistency, ensuring that the final products are of the highest quality.But it's not just the quality of their products that makes Metal Melting Forge stand out. They also offer a wide range of services such as design consulting, installation, and training to help their customers get the most out of their products. Their team of experienced technicians provides expert advice and support, ensuring that customers are able to get the most out of their equipment.In addition, Metal Melting Forge offers a great warranty on all their products. Their customer service team is available 24/7 to provide assistance with troubleshooting, repairs, and maintenance, ensuring that their customers are always able to get the best possible results from their equipment.When it comes to metal melting equipment, Metal Melting Forge is the go-to choice for professionals in the industry. Their exceptional quality, innovation, and commitment to customer service set them apart as one of the leading suppliers in the market. For those in the market for top-quality metal melting equipment, Metal Melting Forge is sure to provide the perfect solution.
Aluminum Melting Forge: An Essential Guide for Efficient Aluminum Melting
Aluminum Melting Forge: A Revolutionary Solution for the Metal Manufacturing IndustryIn the metal manufacturing industry, the process of melting and casting aluminum is critical. This process has traditionally been accomplished through a variety of methods, including electric arc furnaces, induction furnaces, and gas-fired furnaces. However, these methods are often inefficient, costly, and time-consuming. Enter Aluminum Melting Forge, a revolutionary solution for the aluminum melting process that is changing the game for manufacturers around the world.Aluminum Melting Forge is a state-of-the-art machine that uses advanced technology to melt aluminum quickly and efficiently. Unlike other methods, Aluminum Melting Forge uses a patented technology that enables the melting process to occur in just minutes, rather than hours. This technology allows manufacturers to produce high-quality aluminum products with greater speed and precision.Aluminum Melting Forge is also highly efficient. The machine consumes significantly less energy than traditional methods, which means manufacturers can save money on their energy bills while also reducing their carbon footprint. The machine is also designed to be compact and easy to operate, which means it can be installed in any manufacturing facility without the need for significant modifications.Moreover, Aluminum Melting Forge is equipped with a range of advanced features that enable it to perform at the highest level. The machine is equipped with a computer-controlled system that monitors the melting process in real-time, ensuring that the aluminum is melted at the correct temperature and for the correct amount of time. Additionally, the machine is designed with safety in mind, with features such as emergency stop buttons, safety interlocks, and alarms that alert operators to any potential issues.The benefits of Aluminum Melting Forge are clear. For manufacturers, the machine offers faster cycle times, reduced energy costs, and improved product quality. These benefits translate into increased productivity, profitability, and competitiveness. Furthermore, the machine's advanced technology and safety features make it a reliable and safe solution for aluminum melting, which gives manufacturers peace of mind knowing that their operations are in good hands.One company that has benefited from Aluminum Melting Forge is (removed for privacy). The company is a leading manufacturer of aluminum products, and it has been using Aluminum Melting Forge for several years. According to (removed for privacy), the machine has revolutionized its manufacturing process, enabling it to produce high-quality aluminum products faster and more efficiently than ever before."(Aluminum Melting Forge) has been a game-changer for us," said (removed for privacy). "We are now able to produce aluminum products in a fraction of the time it used to take us, which has allowed us to meet the needs of our customers more efficiently. The machine is also incredibly easy to use, and the safety features give us peace of mind that our operations are safe and secure."Aluminum Melting Forge is not only transforming the manufacturing process for aluminum products but is also having a positive impact on the environment. By consuming less energy, the machine helps to reduce greenhouse gas emissions, which makes it a sustainable choice for manufacturers who are looking to reduce their carbon footprint.In conclusion, Aluminum Melting Forge is a revolutionary solution for the aluminum melting process that is changing the game for manufacturers around the world. With its advanced technology, safety features, and efficiency, it is helping to drive productivity, profitability, and sustainability in the metal manufacturing industry. As more manufacturers adopt this technology, we can expect to see even greater advancements in the industry and a positive impact on the environment.
Revolutionize Your Metal Melting Process with Electric Technology
Electric Metal Melter: A Revolutionary Way to Melt MetalIn the world of metalworking, one of the most important processes is melting metal. This is the first step in creating a wide range of metal products, from jewelry to auto parts to machinery components. While there are many methods for melting metal, some are more efficient and effective than others. One of the most innovative and game-changing methods is the electric metal melter.Electric metal melters are devices that use electricity to create heat and melt metal. They operate by passing an electric current through a wire or electrode, which then heats up and melts the metal. This is different from other methods like gas or coal-fired melting, which rely on combustion to create heat.Electric metal melters have several advantages over traditional melting methods. First, they are much cleaner and more environmentally friendly. They produce no emissions or pollutants, making them safe to use in a variety of settings. Second, they are often more efficient, meaning they use less energy and take less time to melt the metal. Finally, they are more precise, allowing for better control over the melting temperature and process.One company leading the charge in electric metal melting is \[remove brand name\]. Founded in 2008, \[remove brand name\] has quickly become a leader in the metalworking industry. They specialize in creating high-quality electric metal melters, as well as other equipment like laser cutters and CNC machines.\[Remove brand name\] operates out of a state-of-the-art facility in \[location\], where they employ a skilled team of engineers and technicians. They are committed to innovation and constantly pushing the boundaries of what is possible in the world of metalworking. They pride themselves on delivering top-of-the-line products and exceptional service to their customers around the world.One of \[remove brand name\]’s flagship products is their electric metal melter, which comes in a range of sizes and capacities to meet the needs of any metalworking project. These melters are designed to be highly efficient, using less energy and time than traditional methods while providing precise temperature control. They are also incredibly easy to use, with a simple interface and intuitive controls that make them accessible to operators of all skill levels.But \[remove brand name\]’s electric metal melters are more than just a tool for melting metal. They represent a new way of thinking about the metalworking process and what is possible. With their focus on innovation and commitment to excellence, \[remove brand name\] is helping to usher in a new era of metalworking that is faster, cleaner, and more precise than ever before.So whether you’re a jewelry maker, a machinist, or a metal sculptor, an electric metal melter from \[remove brand name\] could be just what you need to take your craft to the next level. With their cutting-edge technology, exceptional quality, and commitment to customer service, \[remove brand name\] is leading the charge in the world of metalworking and helping to transform the industry for the better.
Benefits of Ceramic Paper Insulation: A Revolutionary Solution for Efficient Home Insulation
Title: Innovative Ceramic Paper Insulation Revolutionizes the Construction IndustryIntroduction:{Company Name}, a pioneering company specializing in cutting-edge insulation solutions, has recently unveiled its latest product, Ceramic Paper Insulation. This revolutionary material is set to transform the construction industry, providing a sustainable and highly efficient alternative to traditional insulation methods.Innovation at its Core:Ceramic Paper Insulation is a lightweight and flexible material that offers excellent thermal insulation properties. It is composed of a combination of high-grade advanced ceramics and natural cellulose fibers, making it both environmentally friendly and highly durable. This innovative product provides a versatile solution for various applications, ranging from residential to commercial construction projects.Unmatched Thermal Efficiency:One of the most remarkable features of Ceramic Paper Insulation is its extraordinary thermal efficiency. The material's unique composition enables it to resist heat transfer, effectively minimizing energy loss and reducing heating and cooling costs. This attribute ensures that buildings remain cooler in summer, warmer in winter, and more energy-efficient all year round.Environmentally Sustainable:{Company Name}'s Ceramic Paper Insulation is a game-changer in terms of sustainability for the construction industry. It is free from harmful emissions such as formaldehyde and other volatile organic compounds (VOCs) commonly found in traditional insulation. The material's production process minimizes energy consumption, waste generation, and carbon emissions, further contributing to a greener future.Versatile and Easy to Install:Ceramic Paper Insulation is available in various thicknesses and can be easily customized to fit different structures and applications, including walls, roofing, and pipes. Its flexibility allows for seamless installation, eliminating gaps and preventing air leakage. This ease of installation ensures that the entire construction process is more efficient, saving both time and money.Durability and Longevity:Designed to withstand extreme temperatures, Ceramic Paper Insulation outperforms other conventional insulation materials, guaranteeing longevity and reducing the need for continuous maintenance. The material's exceptional resistance to wear and tear ensures that its insulating properties remain intact even after years of active use, thus providing a sustainable and cost-effective solution to building insulation.Fire-Resistant Properties:Safety is a paramount concern in any construction project, and Ceramic Paper Insulation excels in this area as well. The material possesses excellent fire-resistant properties, making it an ideal choice for a wide range of applications. By significantly reducing the spread of flames and toxic smoke, this insulation solution enhances the overall safety of buildings, ensuring a secure environment for residents, employees, and visitors alike.Contributing to Energy Efficiency Regulations:With the increasing focus on energy efficiency, Ceramic Paper Insulation helps construction projects meet regulatory guidelines and certifications. Its exceptional thermal performance enables buildings to achieve higher energy ratings, thereby fulfilling the requirements set by sustainability standards and contributing to a greener future.Conclusion:The launch of Ceramic Paper Insulation by {Company Name} marks a significant milestone in the construction industry. Its unparalleled thermal efficiency, sustainability, and versatility make it a superior alternative to conventional insulation materials. By incorporating this cutting-edge innovation in their projects, architects, contractors, and homeowners can significantly contribute to reducing energy consumption, enhancing safety standards, and building a more sustainable tomorrow.
Maximizing the Benefits of Refractories for Optimal Performance
Title: Utilization of Refractories in Various Industries Aids Production EfficienciesIntroduction:Refractories are indispensable materials widely used across a range of industries for their ability to withstand high temperatures and aggressive environments. These substances play a critical role in the manufacturing processes of steel, cement, glass, ceramics, and a variety of other industries. The utilization of refractories ensures enhanced production efficiencies, improved product quality, and reduced energy consumption, making them an essential component in modern industrial applications.Key Characteristics of Refractories:Refractories are non-metallic materials with high melting points, excellent thermal shock resistance, and stability at extreme temperatures. They are designed to withstand significant pressure, chemical attacks, and abrasion, making them integral to the production processes.Refractories in the Steel Industry:The steel industry is the largest consumer of refractories, utilizing them in several key areas of production. Refractories line the furnaces, electric arc furnaces, and ladles, providing insulation and protection against the corrosive effects of molten metals and slag. They help maintain high temperatures and protect the vessel walls, resulting in improved energy efficiency and longer-lasting equipment. The utilization of high-quality refractories in steelmaking enables longer campaign life, reduced downtime, and improved steel quality.Refractories in the Cement Industry:Refractories find extensive use in the cement industry, primarily in kilns and cement rotary kilns. These components are subjected to harsh conditions, including extreme temperatures and chemical reactions. Refractories provide insulation, corrosion resistance, and wear protection, thus ensuring prolonged kiln life, reduced maintenance costs, and enhanced energy efficiency. By utilizing advanced refractories, cement manufacturers can optimize their production processes, resulting in higher-quality cement and reduced environmental impact.Refractories in the Glass Industry:The glass industry relies heavily on refractories for its manufacturing operations, particularly in glass furnaces. Refractories, such as silica bricks, zirconia, and alumina-based materials, are used as linings to withstand the extreme temperatures required for glass melting and shaping. Refractories enable steady heat distribution, protect against chemical reactions, and minimize energy losses. By employing effective refractory solutions, glass manufacturers can achieve maximum production output while maintaining consistent quality standards.Refractories in the Ceramics Industry:The ceramics industry heavily depends on refractories for various processes, including firing, sintering, and glazing. Refractories help provide an ideal thermal environment required for ceramic material transformation. High-quality refractory bricks, castables, and ceramic fibers ensure uniform heat distribution, controlled thermal gradients, and effective insulation throughout the firing process. Deploying suitable refractory materials enables ceramic manufacturers to achieve consistent product quality, minimize wastage, and reduce energy consumption.Developments in Refractory Technology:Continuous research and development in refractory technology have led to significant advancements, resulting in improved performance and cost-effectiveness. The use of advanced monolithic refractories, reinforced with specialty fibers and binders, enhances the overall strength and durability of refractory linings. Besides, the incorporation of nanotechnology in refractory manufacturing has shown promising results in terms of improving thermal stability, reducing material consumption, and extending product lifespan.Environmental Considerations:As industries globally strive to reduce their carbon footprint, refractories have a crucial role to play in achieving sustainability targets. There is a growing emphasis on developing eco-friendly refractories with lower emissions and increased recyclability. Sustainable refractory solutions contribute to greener production processes, reduced energy consumption, and minimized waste generation, promoting a more environmentally conscious industrial sector.Conclusion:The widespread utilization of refractories across various industries highlights their crucial role in enhancing production efficiencies, reducing downtime, and improving product quality. The continuous improvements in refractory technology, along with an increasing focus on sustainability, will further drive their demand. Through a combination of continuous innovation and responsible manufacturing practices, refractory manufacturers can support the evolving needs of industries while adhering to environmental standards, thus contributing to a sustainable and efficient industrial landscape.
New Study Shows Advancements in the Use of Calcium Alumina Cement in Construction
Title: Revolutionary Calcium Alumina Cement Enhances Construction Industry's FutureIntroduction (100 words):In a breakthrough for the construction industry, a pioneering company has unveiled a game-changing innovation – Calcium Alumina Cement (CAC). This remarkable development, which requires the removal of the brand name, is set to redefine the way construction materials are selected, providing unparalleled strength, durability, and versatility. With its unique composition and cutting-edge manufacturing process, CAC guarantees superior performance in various construction applications, making it an ideal choice for engineers, architects, and contractors worldwide. This article aims to provide an overview of this groundbreaking cement, highlighting its key attributes and potential impact on the industry.1. Unleashing the Power of Calcium Alumina Cement (150 words):CAC is a remarkable cementitious material composed of calcium aluminates that possesses outstanding physical properties. It is manufactured using state-of-the-art technology, ensuring a high degree of purity and homogeneity. CAC exhibits remarkable early strength development and rapid curing, making it an excellent choice for time-sensitive construction projects. Its exceptional resistance to chemical attacks, such as from sulfates or alkalis, ensures long-lasting structural integrity. Moreover, unlike traditional Portland cement, CAC exhibits minimal shrinkage during the curing process, reducing the risk of cracking and enhancing the overall durability of concrete structures.2. Versatility in Construction Applications (150 words):One of the key advantages of CAC is its versatility, making it suitable for an extensive range of construction applications. With its exceptional early strength, it is particularly advantageous in precast concrete manufacturing, enabling quick demolding and accelerated project timelines. Its excellent sulfate resistance makes it ideal for marine environments or areas with high sulfate content in soils, ensuring long-term durability of structures. Additionally, due to its resistance to alkalis, CAC is a top choice for constructions with sulfate-resistant cement requirements.3. Environmental Benefits of CAC (150 words):In an era where sustainability is paramount, CAC offers notable environmental advantages over conventional cements. With its lower carbon footprint and reduced energy consumption during manufacturing, CAC aligns with environmentally conscious construction practices. Utilizing CAC as a substitute for ordinary Portland cement can contribute to reductions in greenhouse gas emissions, ultimately minimizing environmental impact. The long-term durability of CAC-enhanced structures further helps in optimizing resources by reducing the need for reconstruction and maintenance.4. Cutting-Edge Manufacturing Process (150 words):The manufacturing process behind CAC involves cutting-edge techniques that ensure consistent and reliable production. Through extensive research and development, the company has perfected the formulation to provide optimum performance. Rigorous quality control measures are employed during manufacturing to maintain the high standards associated with CAC. Moreover, ongoing monitoring and research drive continuous improvement in its production process, ensuring that CAC remains at the forefront of construction innovation.Conclusion (100 words):Calcium Alumina Cement (CAC), whose brand name has been omitted, presents an exciting future for the construction industry. With its unique composition, exceptional strength, and durability, CAC offers unmatched performance, revolutionizing construction material selection. The versatility of CAC allows it to cater to diverse construction requirements, ensuring its wide-scale adoption in various projects worldwide. Additionally, the eco-friendly characteristics of CAC align well with the sustainability goals of the industry. As technology and manufacturing processes continue to evolve, CAC is poised to reshape the construction landscape, offering engineers, architects, and contractors a better, stronger, and greener alternative.