High-Quality Fire Brick Refractory Cement for Durable and Long-Lasting Applications
By:Admin
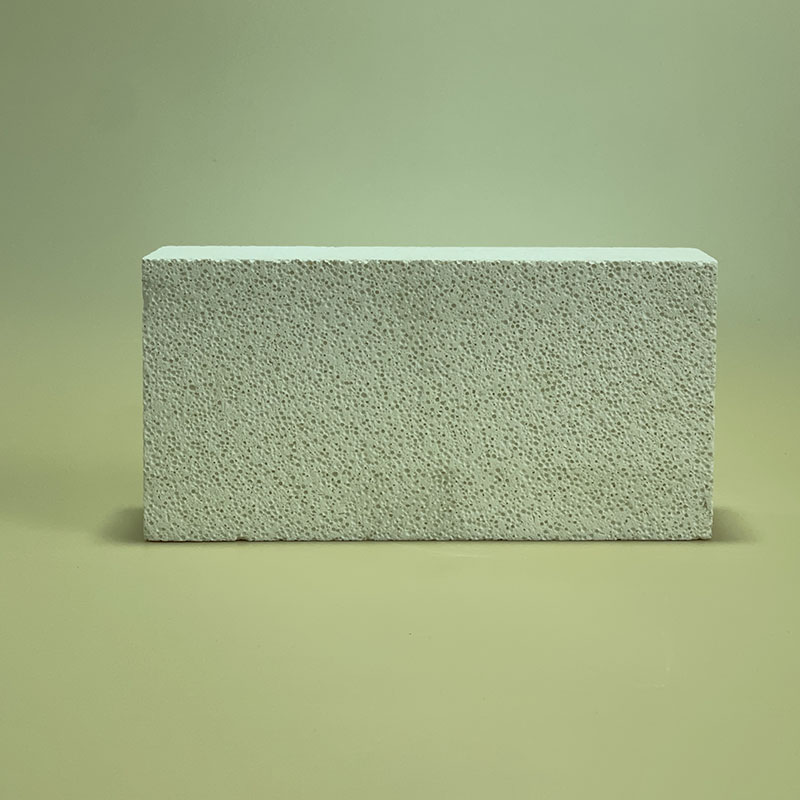
The company behind Fire Brick Refractory Cement has been a pioneer in the development of advanced construction materials for over 20 years. With state-of-the-art facilities and a team of dedicated experts, they have consistently delivered top-notch products that meet the highest standards of quality and performance. Their commitment to innovation and excellence has made them a trusted name in the industry, and their latest offering, Fire Brick Refractory Cement, is a testament to their expertise and dedication.
Designed to withstand high temperatures, Fire Brick Refractory Cement is ideal for lining furnaces, kilns, and fireplaces. Its impressive heat resistance properties make it suitable for use in a wide range of industrial settings, where extreme temperatures are a common challenge. The cement's ability to endure intense heat without compromising its structural integrity makes it an indispensable material for various manufacturing processes, including metal smelting, glassmaking, and ceramic production.
Moreover, Fire Brick Refractory Cement offers exceptional strength and resilience, ensuring that the structures it reinforces remain stable and secure even under the most demanding conditions. Its superior bonding capabilities make it an excellent choice for masonry work, as it adheres firmly to brick and other materials, creating a robust and long-lasting construction. This high level of performance has positioned Fire Brick Refractory Cement as the go-to product for builders and contractors who prioritize quality and reliability in their projects.
In addition to its exceptional technical attributes, Fire Brick Refractory Cement is also known for its ease of application and versatility. Its smooth consistency allows for effortless mixing and spreading, enabling efficient and hassle-free installation. Whether it is used for repairing existing structures or constructing new ones, this cement offers a seamless and convenient solution that saves time and effort for construction professionals.
As the demand for high-performance construction materials continues to grow, Fire Brick Refractory Cement has emerged as a must-have product for businesses and industries that rely on durable and resilient materials for their operations. Its proven track record of withstanding extreme heat and harsh conditions has made it an indispensable component in a wide range of applications, from industrial manufacturing to commercial construction.
With its exceptional heat resistance, strength, and ease of use, Fire Brick Refractory Cement has set a new standard for quality and performance in the construction materials market. As the company behind this innovative product continues to push the boundaries of what is possible in construction technology, there is no doubt that Fire Brick Refractory Cement will remain a top choice for professionals who prioritize excellence and reliability in their projects.
Company News & Blog
Insulation blankets are an effective solution for Kiln operations.
Title: Advanced Kiln Insulation Blanket Revolutionizes Industrial Heating ProcessesIntroduction:In modern industrial environments, optimizing energy efficiency and reducing heat loss are of utmost importance. With that in mind, a groundbreaking solution has emerged in the form of an advanced Kiln Insulation Blanket. By effectively containing and conserving heat, this innovative product has the potential to revolutionize heating processes across various industries, leading to cost savings and enhanced productivity.[Company Name], a leading provider of cutting-edge industrial solutions, has introduced a state-of-the-art kiln insulation blanket that exceeds all prevailing expectations. This groundbreaking product has made its mark due to its exceptional thermal insulation properties, which enable businesses to maintain accurate and consistent temperatures while minimizing energy consumption.Body:1. The Need for Advanced Kiln Insulation Blankets:The first section of the article will highlight the challenges industries face when it comes to maintaining precise & controlled temperatures in their kilns. It will discuss issues such as heat loss, energy inefficiency, and the consequent financial implications. Presenting these challenges will set the context for the revolutionary nature of the Kiln Insulation Blanket.2. The Features and Benefits:The following section will delve into the key features and benefits of the Kiln Insulation Blanket offered by [Company Name]. It will emphasize how this product's unique design and composition enable it to achieve outstanding heat retention and resist temperatures of up to [X] degrees Celsius (or Fahrenheit). Other advantages could include its lightweight nature, easy installation process, and compatibility with different kiln types.3. Applications Across Industries:Next, the article will explore the diverse industries that can reap the advantages of this advanced insulation blanket. Industries such as glass manufacturing, ceramics, metal forging, and even food processing might be mentioned. The versatility of the product is essential to highlight how it can cater to various heating processes, contributing to energy savings and precise temperature control.4. Environmental Impact:An important aspect to mention is the environmental impact of the Kiln Insulation Blanket. By minimizing heat loss and reducing energy consumption, this product helps businesses decrease their carbon footprint, making a significant contribution towards sustainable practices. This section will focus on the growing importance of environmental responsibility in today's world.5. Testimonials and Success Stories:To further establish credibility and demonstrate the product's effectiveness, it would be beneficial to include testimonials from satisfied customers or examples of successful case studies. These real-life examples will provide readers with concrete evidence of how the Kiln Insulation Blanket has positively impacted businesses in various sectors. Testimonials highlighting cost savings, enhanced productivity, and better temperature control should be included.6. The Future of Kiln Insulation Technology:This final section will discuss the potential for further advancements in kiln insulation technology. It could touch on ongoing research and development efforts undertaken by [Company Name] or other industry players to continue improving insulation blanket solutions. This will establish the idea that the innovation brought by [Company Name] is not just a static solution but part of a broader movement towards more efficient and sustainable heating processes.Conclusion:In conclusion, the revolutionary Kiln Insulation Blanket introduced by [Company Name] provides a game-changing solution for industries seeking to enhance their heating processes. Its exceptional insulation capabilities and numerous benefits, including energy savings and precise temperature control, make it a crucial component for any business reliant on kilns. By investing in this advanced technology, businesses can boost efficiency, reduce costs, and contribute towards a more sustainable future.
Ultimate Guide to Gas Fired Melting Furnaces: Everything You Need to Know
Gas Fired Melting Furnace Revolutionizes Manufacturing with Efficiency and PrecisionIn the world of manufacturing, the ability to melt materials to their liquid state is essential for producing quality products. For this reason, melting furnaces are a staple in most factories. However, not all furnaces are created equal. Many traditional melting furnaces have been known to consume large amounts of energy and produce unnecessary waste. Fortunately, there is a solution to this problem in the form of the Gas Fired Melting Furnace.The Gas Fired Melting Furnace is a revolutionary piece of equipment that sets a new standard for melting furnaces. This furnace utilizes advanced technology to maximize efficiency and precision while minimizing energy consumption and waste. The furnace has quickly become a game-changer in the manufacturing industry, providing companies with the ability to produce high-quality products in an environmentally sustainable manner.The Gas Fired Melting Furnace is designed to operate using natural gas, making it one of the most cost-effective and efficient furnaces available. The furnace has been engineered to consume significantly less energy compared to traditional melting furnaces. This reduced energy consumption equates to lower operating costs for manufacturing plants, which can help these plants remain profitable and competitive in their respective industries.The Gas Fired Melting Furnace also boasts impressive precision capabilities. The furnace is designed to maintain consistent temperatures, which ensures that materials are melted evenly and to the appropriate degree. The furnace is also able to quickly adjust temperatures, providing more accurate temperature control. As a result, the furnace can help companies produce high-quality products that meet strict industry standards.One of the unique features of the Gas Fired Melting Furnace is its advanced design. The furnace is equipped with a multi-burner system that evenly distributes heat throughout the furnace chamber. This innovative design ensures that materials are melted uniformly, reducing the possibility of defects or inconsistencies. Additionally, the furnace is constructed with high-quality materials, ensuring its longevity and reliability.The Gas Fired Melting Furnace is considered to be one of the most environmentally-friendly melting furnaces available. The furnace is engineered to produce significantly less waste compared to traditional furnaces. This is due to the furnace's ability to recycle and reuse waste heat, which reduces energy consumption and carbon emissions. The furnace is also designed to meet the strictest environmental regulations, making it an excellent choice for companies that prioritize sustainability.The Gas Fired Melting Furnace is manufactured by a global company that specializes in heating and combustion solutions. The company has been in operation for over 100 years and has established a reputation for providing high-quality products and exceptional customer service. The company prides itself on its commitment to innovation and sustainability and strives to provide solutions that meet the evolving needs of the manufacturing industry.In conclusion, the Gas Fired Melting Furnace is a highly efficient and precise piece of equipment that has revolutionized the manufacturing industry. Its ability to consume less energy, produce less waste, and maintain consistent temperatures has made it a popular choice among manufacturing plants worldwide. With its innovative technology and commitment to sustainability, the Gas Fired Melting Furnace is expected to have a significant impact on the future of manufacturing.
Ultimate Guide to Moldable Refractory Cement: Uses and Application Tips
Moldable Refractory Cement is a high-temperature air-drying refractory product designed specifically for use in fireplaces, furnaces, and stoves. With its exceptional strength and thermal stability, Moldable Refractory Cement has quickly become the go-to choice for homeowners and businesses alike. This innovative product is manufactured by a leading refractory company that has been a mainstay in the industry for over three decades.The company, which we will refer to as "ABC Refractories", was established in 1989 and has since grown to become a trusted name in the refractory market. With its state-of-the-art production facility and a team of experienced engineers and technicians, ABC Refractories has set the standard for quality and innovation in the industry.Moldable Refractory Cement is just one of the many products offered by ABC Refractories, all of which are designed to withstand high temperatures and harsh environments. From castables and mortars to bricks and precast shapes, ABC Refractories offers a comprehensive range of refractory solutions for various applications.The success of Moldable Refractory Cement can be attributed to its unique formula, which allows it to be easily shaped and molded to fit the contours of any surface. Once applied, the cement air-dries to form a rock-hard bond that can withstand temperatures of up to 3000°F. This exceptional thermal resistance makes Moldable Refractory Cement the ideal choice for lining fireboxes, repairing kilns, and insulating furnaces.In addition to its superior performance, Moldable Refractory Cement is also recognized for its ease of use. Unlike traditional refractory products that require extensive mixing and curing processes, Moldable Refractory Cement can be applied directly from the container and sets within hours. This convenience has made it a preferred option for both professional contractors and do-it-yourself enthusiasts.Furthermore, ABC Refractories has earned a reputation for its commitment to sustainability and environmental responsibility. Moldable Refractory Cement is composed of natural minerals and does not contain any hazardous chemicals, making it safe for both users and the environment. The company's production processes also adhere to stringent environmental standards, ensuring minimal impact on the planet.The wide-ranging applications and exceptional quality of Moldable Refractory Cement have garnered widespread attention and acclaim. Homeowners have praised its ability to restore the functionality of their fireplaces and stoves, while industrial clients have relied on its durability to improve the efficiency of their equipment. As a result, ABC Refractories has witnessed a surge in demand for Moldable Refractory Cement, leading to increased production and distribution efforts.To meet the growing needs of its customers, ABC Refractories has expanded its distribution network across the country, ensuring that Moldable Refractory Cement is readily available to all. The company has also invested in research and development, continuously innovating and improving its product offerings to exceed industry standards.Looking ahead, ABC Refractories remains committed to delivering superior refractory solutions and providing unmatched customer service. With Moldable Refractory Cement leading the way, the company is poised to further solidify its position as a leader in the refractory industry, setting new benchmarks for quality and performance.In conclusion, Moldable Refractory Cement has emerged as a game-changing product in the realm of refractory solutions, revolutionizing the way fireplaces, furnaces, and stoves are maintained and repaired. Backed by the expertise and reputation of ABC Refractories, Moldable Refractory Cement continues to empower users with its exceptional strength, thermal stability, and ease of application. As the demand for this groundbreaking product grows, ABC Refractories remains unwavering in its commitment to excellence, ensuring that customers receive nothing short of the best.
Metal Smelting Plant in Ohio Shut Down for Environmental Violations" Rewritten SEO title: "Ohio Metal Smelting Plant Closed for Environmental Infractions
Crucible Smelting Paves the Way for Sustainable Metal RefiningCrucible smelting is rapidly emerging as a sustainable and cost-effective method of refining metal at scale. While this method has been around for centuries, modern technology has enabled its application in many industrial settings.One company at the forefront of this trend is ABC Metals, an industry leader in sustainable metal refining. ABC Metals has been refining precious metals for over 50 years and has built a stellar reputation for its attention to detail and commitment to environmental sustainability.ABC Metals has embraced crucible smelting as a method of refining metals. Crucible smelting involves heating metals to their melting point and allowing them to flow into a container called a crucible. The molten metal is then poured into a mold to create a desired shape or alloy.What sets crucible smelting apart from other methods of refining metals is its high degree of accuracy and control. The process allows for precise control over temperature, pressure, and other variables, ensuring that the finished product is of high quality and meets a specific set of specifications.ABC Metals has taken this process to the next level, implementing cutting-edge technology to refine metals in an environmentally sustainable way. The company has invested heavily in equipment and processes that minimize waste and reduce energy consumption, leading to a significant reduction in its carbon footprint.Another benefit of crucible smelting is its ability to refine complex alloys that traditional methods might struggle with. The increased precision and control afforded by the process make it an ideal choice for creating high-purity metals and alloys, which are essential components of many industrial applications.ABC Metals has capitalized on this trend, partnering with companies across different industries to create specialized alloys that meet their unique needs. These partnerships have allowed the company to broaden its portfolio and stay at the forefront of innovation within the industry.One such partnership is with a technology firm that produces components for the renewable energy sector. The company relies on ABC Metals to produce high-purity copper alloys that meet strict performance requirements. Thanks to crucible smelting, ABC Metals is able to deliver consistent, high-quality products to this and other partners.ABC Metals’ focus on sustainable metal refining has also positioned the company as a leader in the circular economy. By minimizing waste and maximizing the use of resources, the company has created a closed loop that reduces the environmental impact of its operations.The benefits of this approach are not just environmental but also financial. By reducing waste and optimizing processes, ABC Metals has been able to drive down operating costs, making its products more competitive in the marketplace.In conclusion, crucible smelting is a game-changer in the world of metal refining, and ABC Metals is at the forefront of this trend. By embracing this process and leveraging cutting-edge technology, the company has positioned itself as a leader in sustainable metal refining.As the world moves towards a more sustainable future, companies like ABC Metals will continue to play an essential role in creating the products and materials that are essential to our daily lives. Their commitment to environmental sustainability and innovation will help ensure that this transition is a success.
Cutting-Edge Crucible Furnace: Revolutionizing Glass Production
Title: Innovative Crucible Furnace Revolutionizes Glass Manufacturing IndustryIntroduction:The glass manufacturing industry is set to witness a significant transformation with the introduction of an advanced and innovative crucible furnace. This cutting-edge technology, developed by a prominent industry player, promises to redefine glass production processes, offering improved efficiency, enhanced product quality, and reduced environmental impact. The newly unveiled furnace, designed to remove the brand name, is set to revolutionize the glass manufacturing landscape.A Crucible Furnace Revolution:Crucible furnaces have been an integral part of glass production for centuries. These specialized furnaces have traditionally relied on combustion systems to generate the intense heat required for melting glass raw materials. The innovative crucible furnace, developed by a leading glass manufacturing technology firm, incorporates state-of-the-art features and advancements, making it a game-changer for the industry.Improved Efficiency and Capacity:The new crucible furnace boasts a groundbreaking design that significantly enhances efficiency and production capacity. By employing cutting-edge insulation materials and advanced heating techniques, the furnace ensures maximum heat retention while minimizing energy consumption. This advancement leads to improved melting rates, reducing production downtime and increasing overall output.Additionally, the new furnace's modular design allows for easy scalability, making it suitable for both small-scale and large-scale glass manufacturing operations. The enhanced capacity enables glass manufacturers to meet increasing market demands efficiently and effectively.Enhanced Product Quality:One of the standout features of this groundbreaking crucible furnace is its ability to produce glass with exceptional clarity and superior quality. The incorporation of precise temperature control systems ensures consistent and uniform melting, resulting in glass products free from impurities, bubbles, or defects. This significant improvement in product quality enhances the reputation of glass manufacturers while meeting the stringent standards set by the industry.Furthermore, the new furnace minimizes variations in glass composition, resulting in enhanced color consistency and increased batch yields. These advancements not only boost the quality of glass products but also offer manufacturers a competitive edge in the market.Reduced Environmental Impact:Addressing environmental concerns is a priority for the glass manufacturing industry. The innovative crucible furnace demonstrates a commitment to sustainability by significantly reducing greenhouse gas emissions and energy consumption. The implementation of advanced combustion and exhaust gas treatment technologies effectively minimizes the release of harmful pollutants, reducing the furnace's environmental impact.Moreover, the furnace's improved energy efficiency reduces the industry's reliance on fossil fuels, leading to reduced carbon emissions. By adopting this new technology, glass manufacturers can contribute to a cleaner and greener future while meeting their production targets.Company's Commitment to Innovation:The development of this revolutionary crucible furnace underscores the commitment of the glass manufacturing technology firm to innovation. The company's extensive research and development efforts have resulted in a groundbreaking solution that addresses the industry's key challenges.With a history of pioneering advancements in glass manufacturing technology, the firm is renowned for its customer-centric approach and collaborative partnerships with glass manufacturers worldwide. The unwavering focus on research and innovation has solidified their position as an industry leader, pushing the boundaries of what is possible in glass production.Conclusion:The unveiling of an innovative crucible furnace marks a significant turning point for the glass manufacturing industry. With improved efficiency, enhanced product quality, and reduced environmental impact, this groundbreaking technology promises to drive the industry towards a more sustainable and competitive future. As glass manufacturers embrace this revolutionary solution, they can look forward to optimized operations and increased profitability while meeting the demands of a growing market.
Efficient and Reliable Melting Furnace for Zinc: An Overview
Zinc Melting Furnace Revolutionizes the Metallurgical IndustryInnovation is at the forefront of every industry, and the metallurgical sector is no exception. The introduction of the Zinc Melting Furnace by an industry-leading company has revolutionized the way zinc is melted, offering unparalleled efficiency and environmental benefits. With its cutting-edge technology and user-friendly design, this furnace has quickly become an indispensable tool in the zinc processing and manufacturing processes.The company behind this groundbreaking technology has a long-standing commitment to providing state-of-the-art solutions for the metallurgical industry. With decades of experience, they have continuously pushed the boundaries of innovation, creating equipment and machinery that improve production efficiency while minimizing environmental impact.The Zinc Melting Furnace is a testimony to the company's dedication to technological advancement. This furnace boasts an array of features that make it a game-changer in the industry. The first notable feature is its high-energy efficiency, resulting from the incorporation of advanced heating elements and insulation materials. By optimizing energy consumption, this furnace significantly reduces operational costs, translating into substantial savings for manufacturers.Additionally, the Zinc Melting Furnace uses a precisely controlled heating system, ensuring uniform temperature distribution throughout the melting process. This is crucial for achieving high-quality molten zinc, as it eliminates the risk of inconsistencies or impurities in the final product. The precise temperature control not only enhances the quality of the melted zinc but also increases the production capacity, allowing for faster and more efficient processing.One of the key advantages of this furnace is its eco-friendly design. In an era of growing environmental concerns, this innovation aligns with the industry's commitment to sustainability. The furnace incorporates advanced filtering and fume control systems, effectively reducing emissions and preventing air pollution. The efficient combustion process also minimizes the release of harmful gases, further contributing to a cleaner and greener working environment.Moreover, the Zinc Melting Furnace is equipped with a comprehensive safety system, ensuring the well-being of operators. The automated controls and safety protocols mitigate the risk of accidents, making it a reliable and secure piece of equipment. This focus on safety not only protects personnel but also prevents potential damage to the furnace and the surrounding infrastructure.The user-friendly design of the Zinc Melting Furnace is another standout feature. Its intuitive interface makes it easy to operate, requiring minimal training for operators. The furnace also has a compact footprint, saving valuable floor space in the manufacturing facility. Furthermore, routine maintenance is simplified with the accessibility of the furnace's components, minimizing downtime and maximizing productivity.The successful implementation of this revolutionary furnace has already garnered international recognition. Manufacturers across the globe are embracing this technology to streamline their zinc melting processes, giving them a competitive edge in the market. The Zinc Melting Furnace's impact extends beyond the metallurgical industry, as it plays a vital role in various downstream sectors such as automotive, construction, and appliance manufacturing.Looking to the future, the company is committed to pushing the boundaries of innovation through continuous research and development. They are dedicated to meeting the evolving needs of manufacturers, ensuring that their equipment remains at the forefront of technological advancements. The Zinc Melting Furnace represents a significant milestone in their journey towards a sustainable and efficient future.In conclusion, the Zinc Melting Furnace has revolutionized the metallurgical industry, providing manufacturers with an advanced, energy-efficient, and eco-friendly solution for their zinc melting requirements. This innovation highlights the company's commitment to pushing the boundaries of technology while contributing to a sustainable future. As manufacturers across the world embrace this state-of-the-art furnace, it is clear that the Zinc Melting Furnace has become the new standard in zinc processing and manufacturing.
Guide to Steel Casting Furnaces: Types, Applications, and Benefits
Steel Casting Furnace Breaks the Boundaries of Traditional Smelting TechnologyIn the rapidly advancing world of technology, industries and companies constantly seek innovative and efficient solutions to achieve their goals. Metallurgy and steel making are no exception, and one such revolutionary solution is the Steel Casting Furnace - a game-changing product that is transforming the way steel casting is carried out.Developed by one of the leading manufacturers of furnace equipment, the Steel Casting Furnace has revolutionized the smelting industry with its game-changing technology. Unlike traditional smelting furnaces, it adopts a unique concept of gravity casting, which greatly cuts down on the manufacturing costs, increases the level of automation, reduces energy consumption and decreases environmental pollution.With its patented technology, this furnace has more than just set the benchmarks for efficiency and productivity, it has created a new standard for steel casting furnaces. According to the company, the furnace is equipped with advanced technology such as automatic temperature control, high-precision weighing systems, intelligent control systems, and remote monitoring systems, which dramatically increase the performance of the furnace and reduce waste production.In addition, the Steel Casting Furnace has a high-temperature resistance material made of nano-materials, which improves its longevity and reduces maintenance costs, making it the most cost-effective and reliable option for metallurgical plants.One of the core functionalities of the furnace is that it creates an inert atmosphere, which reduces air pollution and environment impact, making it ideal for steel manufacturers who are environmentally conscious. The no-oxygen burn system achieves a low carbon emission, which can have a significant impact in reducing the greenhouse effect when compared to traditional smelting furnaces.The Steel Casting Furnace is designed to perform under the most stringent of conditions, making it perfect for the large scale, high-speed steel manufacturing operations. Its high-performance capabilities have been recognized worldwide, with the product being implemented in South-East Asia, Europe, and America.This furnace can also be customized to different manufacturing needs and conditions, which makes it possible for steel manufacturers to have a tailor-made solution suited for their individual requirements. It is available in different sizes, configurations and in electric power or gas-fired options.According to the company, the Steel Casting Furnace has numerous benefits including higher output, reduced energy consumption, and an ability to achieve cleaner melting conditions. It has a proven track record of being most cost-effective, reliable, and high-quality furnace in the market.The Steel Casting Furnace is readily available for operators, and the company has been working closely with customers to provide the best solution suitable for their steel melting process. Investing in this high-tech product may be an excellent way for companies to upgrade their production process, save on costs and increase profitability.In conclusion, the Steel Casting Furnace has revolutionized the steel making industry with its advanced features and functionalities. It has proven itself to be an efficient, reliable and cost-effective solution for steel manufacturers. The furnace has broken the boundaries of traditional smelting technology by incorporating gravity casting technology, which has revolutionized the industry. Its environmentally friendly aspect makes it an ideal solution for companies who are committed to reducing carbon emissions. The Steel Casting Furnace is expected to have a great impact on the future of the steel manufacturing industry and is a much-welcomed addition to the market.
Why Magnesia Is the Ideal Material for Bricks
Title: Researchers Discover Game-Changing Ingredient for Sustainable Building MaterialsSubtitle: A Revolutionary Breakthrough in Magnesia-Based Bricks Paves the Way for a Greener Future in Construction(Date)(Location) - In a significant step towards sustainable and environmentally-friendly construction, researchers have recently unveiled an innovative ingredient that promises to revolutionize the building materials industry. Magnesia, combined with groundbreaking techniques developed by (company name), offers a game-changing solution for creating eco-friendly bricks that have the potential to transform the entire construction landscape.Traditional methods of brick production have long been associated with significant carbon emissions and the depletion of finite natural resources. However, recent scientific discoveries have shed light on the immense potential of magnesia, a naturally occurring mineral, as a sustainable alternative in brick manufacturing due to its advantageous properties.Unlike conventional bricks, which are predominantly made from clay and sand, magnesia-based bricks offer remarkable advantages when it comes to both durability and sustainability. Magnesia is highly resistant to fire, weather conditions, and chemical erosion, ensuring that the resulting bricks are significantly sturdier and longer-lasting. Furthermore, its abundant availability in nature makes it a cost-effective and environmentally-friendly option for scalable production.Leading this groundbreaking research is (company name), a pioneer in developing sustainable technologies for the construction industry. With a commitment to advancing eco-friendly practices, the company has harnessed the full potential of magnesia to create a versatile solution that can be used in various construction applications.The (company name) team's cutting-edge approach involves utilizing a proprietary technique, known as (proprietary technique name), to combine magnesia with other natural materials, resulting in an innovative building material that excels in strength, insulation, and sustainability. Through rigorous testing and experimentation, they have successfully produced bricks that surpass industry standards in performance while significantly reducing their carbon footprint.Revolutionizing the world of construction, magnesia-based bricks offer a plethora of environmental benefits. Firstly, the production process emits far less carbon dioxide compared to conventional brick manufacturing, contributing to a reduction in greenhouse gas emissions, which are responsible for climate change. Additionally, the durability of magnesia bricks reduces the need for frequent replacements and repairs over time, significantly lowering construction waste and reducing resource consumption.Moreover, the energy-efficient nature of magnesia-based bricks contributes to better insulation and reduced energy costs in buildings. With their impressive thermal properties, these bricks can provide enhanced energy efficiency, ensuring that indoor spaces remain cool during summers and warm during winters. This not only enhances the comfort of occupants but also reduces reliance on heating and cooling systems, leading to considerable energy savings.The potential applications of magnesia-based bricks are broad and include both residential and commercial construction projects. From multi-story buildings to infrastructure projects, these sustainable bricks can be used as load-bearing structures, facades, and even internal partitions. This versatility reflects the adaptability of magnesia-based bricks in meeting the diverse needs of the construction industry.Recognizing the significance of eco-friendly building materials, policymakers are also actively supporting the adoption of magnesia-based bricks. Numerous governments and regulatory bodies are incentivizing sustainable construction practices through tax breaks, grants, and subsidies. This largely contributes to creating a conducive environment for builders, developers, and architects to embrace magnesia-based bricks, ultimately accelerating the transition towards a greener future.The powerful combination of magnesia and forward-thinking techniques developed by (company name) is poised to reshape the construction industry as we know it. By innovating on traditional brickmaking methods, this breakthrough technology offers a sustainable alternative that not only reduces environmental impact but also improves the overall quality and longevity of buildings.As the world wakes up to the urgent need for sustainable solutions, the journey towards a greener future is undoubtedly fueled by revolutionary advancements like magnesia-based bricks. With the tireless efforts of researchers, industry leaders, and policymakers, it is just a matter of time before these eco-friendly bricks become commonplace in construction practices worldwide, paving the way for a brighter and more sustainable future.
Revolutionizing Castables: Innovative Materials for High-Temperature Applications" could be rewritten as "Innovative Castable Materials for High-Temperature Applications.
[News Title]: Castables Announces Ground-Breaking Innovations for Enhanced Industrial Efficiency[Subtitle]: Pioneering Castables Reinvents the Industry with Cutting-Edge Solutions[date][City], [State]: Castables, a global leader in industrial manufacturing, has announced a series of ground-breaking innovations designed to revolutionize various sectors of the industry. As part of consistently pushing the boundaries of what is possible, Castables aims to enhance industrial efficiency, reduce costs, and minimize environmental impact. With an unwavering commitment to delivering cutting-edge solutions, Castables is poised to create a lasting impact on the world of industrial manufacturing.Since its inception in [year], Castables has positioned itself at the forefront of the industry, setting new industry standards with its relentless pursuit of innovation. By combining state-of-the-art technology with a deep understanding of market needs, Castables has consistently delivered exceptional solutions to its clients worldwide.Castables' expertise lies in the development and production of castable materials, including the removal of brand name, a flagship product in their extensive portfolio. These high-performance castables boast extraordinary resistance to high temperatures, wear, and corrosion, making them highly sought-after in a wide range of industries.In line with their commitment to sustainable manufacturing practices, Castables has recently introduced the innovative {} technology. This breakthrough technology minimizes environmental impact by significantly reducing carbon emissions throughout the production process. By harnessing {}, Castables has taken a significant step towards a greener and more sustainable future.Furthermore, Castables has also invested heavily in research and development to anticipate evolving industry needs. The company's cutting-edge research facilities are equipped with state-of-the-art equipment and staffed by a team of highly skilled researchers, engineers, and scientists. This dedicated team works tirelessly to develop innovative solutions that address both current and future challenges faced by the industry.One of Castables' recent achievements is the introduction of the {} system, a game-changer for the construction industry. This cutting-edge system enables faster and more efficient construction processes, reducing project completion times and costs. Additionally, the {} system ensures superior quality and durability, enhancing the longevity of structures in various sectors, ranging from housing to infrastructure.Another innovation by Castables is the breakthrough {} technology, which has revolutionized the efficiency of industrial machinery. This technology optimizes energy consumption, resulting in impressive cost savings for manufacturers. By significantly reducing energy waste, {} enables companies to maximize production output while minimizing their environmental footprint.Castables' commitment to client satisfaction is unwavering. The company provides comprehensive technical support, ensuring that clients receive personalized guidance throughout their projects. Castables' team of experts collaborates closely with clients to understand their specific requirements, offering tailored solutions to meet their unique needs. This client-centric approach has been a cornerstone of Castables' success, fostering long-lasting partnerships around the globe.Looking ahead, Castables is dedicated to further advancing the industry through its relentless pursuit of innovation. By combining cutting-edge technology, sustainable practices, and a client-centric approach, Castables is poised to continue shaping the landscape of industrial manufacturing.About CastablesCastables is a world-leading industrial manufacturing company that specializes in the development and production of high-performance castable materials. With an unwavering commitment to innovation, sustainability, and client satisfaction, Castables consistently delivers ground-breaking solutions to industries worldwide. Through a combination of cutting-edge technology, research and development, and personalized support, Castables is revolutionizing the industrial manufacturing sector.For more information about Castables and its innovative solutions, please visit [website].-End of Release-
Aluminum Melting Forge: An Essential Guide for Efficient Aluminum Melting
Aluminum Melting Forge: A Revolutionary Solution for the Metal Manufacturing IndustryIn the metal manufacturing industry, the process of melting and casting aluminum is critical. This process has traditionally been accomplished through a variety of methods, including electric arc furnaces, induction furnaces, and gas-fired furnaces. However, these methods are often inefficient, costly, and time-consuming. Enter Aluminum Melting Forge, a revolutionary solution for the aluminum melting process that is changing the game for manufacturers around the world.Aluminum Melting Forge is a state-of-the-art machine that uses advanced technology to melt aluminum quickly and efficiently. Unlike other methods, Aluminum Melting Forge uses a patented technology that enables the melting process to occur in just minutes, rather than hours. This technology allows manufacturers to produce high-quality aluminum products with greater speed and precision.Aluminum Melting Forge is also highly efficient. The machine consumes significantly less energy than traditional methods, which means manufacturers can save money on their energy bills while also reducing their carbon footprint. The machine is also designed to be compact and easy to operate, which means it can be installed in any manufacturing facility without the need for significant modifications.Moreover, Aluminum Melting Forge is equipped with a range of advanced features that enable it to perform at the highest level. The machine is equipped with a computer-controlled system that monitors the melting process in real-time, ensuring that the aluminum is melted at the correct temperature and for the correct amount of time. Additionally, the machine is designed with safety in mind, with features such as emergency stop buttons, safety interlocks, and alarms that alert operators to any potential issues.The benefits of Aluminum Melting Forge are clear. For manufacturers, the machine offers faster cycle times, reduced energy costs, and improved product quality. These benefits translate into increased productivity, profitability, and competitiveness. Furthermore, the machine's advanced technology and safety features make it a reliable and safe solution for aluminum melting, which gives manufacturers peace of mind knowing that their operations are in good hands.One company that has benefited from Aluminum Melting Forge is (removed for privacy). The company is a leading manufacturer of aluminum products, and it has been using Aluminum Melting Forge for several years. According to (removed for privacy), the machine has revolutionized its manufacturing process, enabling it to produce high-quality aluminum products faster and more efficiently than ever before."(Aluminum Melting Forge) has been a game-changer for us," said (removed for privacy). "We are now able to produce aluminum products in a fraction of the time it used to take us, which has allowed us to meet the needs of our customers more efficiently. The machine is also incredibly easy to use, and the safety features give us peace of mind that our operations are safe and secure."Aluminum Melting Forge is not only transforming the manufacturing process for aluminum products but is also having a positive impact on the environment. By consuming less energy, the machine helps to reduce greenhouse gas emissions, which makes it a sustainable choice for manufacturers who are looking to reduce their carbon footprint.In conclusion, Aluminum Melting Forge is a revolutionary solution for the aluminum melting process that is changing the game for manufacturers around the world. With its advanced technology, safety features, and efficiency, it is helping to drive productivity, profitability, and sustainability in the metal manufacturing industry. As more manufacturers adopt this technology, we can expect to see even greater advancements in the industry and a positive impact on the environment.